Introduction: DIY Heavy Lift Fixed Wing RC Aircraft
In order to maximize payload capacity of the aircraft a very minimalistic design of aircraft is required while minimizing parasitic drag. Certain high lift devices are also used in order to increase the amount of lift the wing is able to produce.
The aircraft design features a fuselage consisting of two 48 inch pine wood beams running parallel to each other 2 inches apart and connected by spacers. A small wooden cage would be constructed towards the nose in order to house a majority of the electrical components and act as a mount for the motor. The wing was a single wing with a span of 54 inches and constructed from XSP insulation foam with wooden spars inserted for structural stability. The wing tips were also sanded into Hoerner wing tips. Junker style ailerons extended from below the trailing edge, and fixed leading edge slats were mounted on the leading edge to improve lift. The tail was a V-tail, the two fins attached to the fuselage by a 3D printed sleeve, and angled at 40 degrees above the horizontal. Each tail fin was made with a 6x6” balsa frame wrapped in aluminum foil, but later extensions and the elevators (control surfaces) were added bringing the final area up to 10”x9”. The aircraft’s landing gear featured two wheels positioned underneath the wing, and the tail mount doubled as a taildragger. The water bottle rocket payload would be mounted between the front wheels and adjusted to ensure a stable center of gravity.
Supplies
S.no
1 Wood dowels and skewers - Lowe's - $38.58 (12ft of 1/4" pine wood
2 Uber ride - Lowe's - $18
3 XPS - Foam Lowe's - $44.19
4 Guitar String - Guitar Center - 5.49 (For Hot Wire Cutting)
5 Gorilla Glue - Slocum Hall Store - $2.58
6 Balsa Wood Scraps/Leftover - $0 (Control Surface Sections, Wedges, Rounded Edge Blocks, 1/4", 1/8" & 1/16" Square sections ~ 4ft of each)
7 12V Power Supply - (Borrowed from Link 043) - $0 (Hot Wire Cutting)
8 Aluminum Foil - CVS - $3.00 (Tail Construction)
9 Building Tools - Borrowed - $0
10 2L Bottle - CVS - $1.89 (Rocket Payload)
11 3D Prints - Syracuse University MakerSpace - $0 (Construction/Prototyping)
12 Nuts, Bolts, and Misc. Hardware - Link Machine Shop - $0
13 Spare Propeller - FliteTest - $6.89
15 Landing Gear Aluminum - Link Machine Shop - $0
16 Brushless Motor (2215 1100kV) , ESC (20-25A) , Propeller (8-9") Combo - FliteTest - $40
17 11.1V 1300mAh 20C LiPo - FliteTest - $20
18 4x 9g Servos - Ebay - $10
19 Spektrum DXe Radio and Receiver - $99
20 Control Horns, CA Hinges, Threaded Pushrods and Clevices - Ebay - $10
21 Corrugated plastic scraps - $0
22 3D printer and Laser Cutter (optional)
23 Balloons - CVS - $3
Step 1: Assesment of Wing Design for High Payload Capacity
In this step, I made a list of potential options for the wing and control surface design for effectivity and based on my mission priorities, selected the fixed leading edge slats, trailing edge junker ailerons and a high wing design.
Step 2: Construction of the Core Wing From XPS Foam
Based on preliminary research, I found that the Clark Y was best suited for my application as it provided very good lift characteristics and was suitable for hot wire cutting. I downloaded the coordinates of the file airfoiltools.com and printed them on paper. After printing the airfoil, I pasted it on a scrap cardboard and cut the template out. This template is useful as it serves as a guide while hot wire cutting the foam.
There were several limiting factors such as the output of the power supply used to heat the wire, the length and strength of the wire available, the accuracy of the cut upon scaling up, etc. For our purposes, after having tried out heating element wire from a table top heater, guitar strings, among many others, we found G string of the guitar wire worked the best. The voltage used was 12V and current through the wire was 1.3A hence the resistance of the wire was found to be about 9 ohms. In order to cut the wing in the desired shape, the cut out cardboard templates were held in place using nails on opposite ends of foam core. The cardboard cuts served as a template and allowed to run the hot wire over them without burning through them while cutting the foam. Experimenting with various types of foam, I settled on XPS Lowes 2” thick insulation foam to work best as it was dense, rigid and easy to work with. After many tries, I found the right speed and coordination in order to cut the desired wing without imperfections with the help of buddy. Due to the size constraint of the wire and problems with scalability of the process, I was able to cut only 18” sections of the wing core hence in the following step I joined three sections using a pine wood spar (1/8" dia dowel) and added reinforcement spars (1/16" dia dowel) at the joints of the wings giving the structure more rigidity.
NOTE - Use weights on top of the foam block to prevent it from moving around.
Step 3: Joining the Wing Core Sections, Adding Electronics and Control Surfaces
Due to the size constraint of the wire and problems with scalability of the process, I was able to cut only 18” sections of the wing core hence in the following step I joined three sections using a pine wood spar (1/8" dia dowel, you can also use square sections too) and added reinforcement spars (1/16" dia dowel, you can also use square sections too) at the joints of the wings giving the structure more rigidity. Once the wing was aligned and glued together, it was sanded to get rid of imperfections due to the hot wire cutting process. The tips of the wing were also sanded so as to function as hoerner wing tips increasing the effective span.
Trimmed sheets of balsa were added at the LE and TE of the center section of the wing so as to not get compressed when using rubber bands to mount it to the fuselage. A good technique while bending balsa sheets is rub a damp cloth on the side you want to curve outwards and to blow hot air using a hair dryer on the concave side. Repeat the process until the desired curvature is achieved. After placing the balsa sheets in position and achieving a good fit, use tape over it - this gives added protection.
After the wing is all in one piece, cut out lengths of 22" from the symmetric airfoil shaped balsa section (you could also just use foam board and cut 2x 22" long and 2" wide sections) for the ailerons. Cut 2 slits into the leading edge of your control surface and insert half of the CA hinge into it. Now using a 3D printer cut a similar section that offsets your aileron in the y-axis from the wing by 1/2"-1" (you could also make a wedge shaped section using balsa to achieve this offset) and glue them to the other end of the CA hinge. Glue the surface with the bumps pressed into the foam at the bottom of the wing ensuring that the ends of the ailerons are flush with the wing tips.
At equal distances from the centerline of the wing, mount the control horns and glue/screw them in place at the bottom section of the control surfaces. After doing so attach the pushrod to it with the help of a clevice and approximate the position of the 9g servo with its geared face up and mark it out on the wing.
Now make a template of a 9g servo by tracing out its bottom profile on sheet of balsa and cut it out using a hobby knife. Cut some excess foam out so that the servo can fit in the wing and traces to route its wire. Glue the template on the bottom surface of the wing and check for the fitting. If all fits well, you are ready to go. If not, screw or unscrew the clevice to adjust the length of the pushrod.
Attachments
Step 4: Fixed LE Slats Manufacturing and Assembly
This step required quite a bit of experimenting and thinking since it hot wire cutting the LE section did not work and having entire 3D printed slats would be too heavy. In the end I decided to laser cut the template of the slat airfoil section on balsa wood and make a balsa sheet shell. About 10-12 ribs were laser cut for each LE slat and glued equidistant from each other on two 1/8” pine wood skewers. A sheet of horizontal grain balsa (make sure of the balsa grain orientation) was then cut with the appropriate dimensions so as to wrap around the airfoil structure. By wetting the balsa using tissue and water, I was able to create curvatures in the directions and by the degree I required using the same technique mentioned in the previous step i.e. wetting the convex surface and blowing hot air on the concave surface. After the sheet had taken the desired shape, we glued the ribs in between this balsa shell. These LE slats were then mounted to the wing with 3x 3D printed mounts for each side of the wing and double sided tape mounted equidistant from each other.
Step 5: Fuselage Construction
The fuselage of our aircraft is built out of 3/8” square pine wood dowels and 3D printed sections.
The primary fuselage structure was constructed out of 3/8” Square wooden dowels which were purchased from Lowe’s. Each section had a length of 36” and in order to construct the full length of the fuselage, an adapter was 3D printed in order to join the 36” sections with additional 12” sections separated by 1 1/4” such that the outer width dimensions of the fuselage was 2” and overall length was 48”. 1 1/4” spacers were placed in between the two dowels in order to provide strength and stability to the structure. The 3D printed V-tail mounts were mounted at the end of the fuselage separated from each other by 6” and glued in place with expanding wood Gorilla Glue.
For the electronics housing cage and motor mount a 2” x 2” x 1/4” plate of pine wood was cut from a sheet of 1/4” thick pine wood (other scrap wood can also be used) and drilled with the motor mount hole pattern. This plate was then glued to front of the fuselage and wooden box housing was constructed 12” x 2” x 2” by arranging two additional 12” sections of the wooden dowels as shown with 1 1/4” wooden dowel supports at the end of the wooden box structure.
Two 4” long sections of the 3/8” pine wood were cut and glued at 12” and 22” from the firewall of the fuselage at the bottom. These will serve as mounting points for the rubberbands that will hold the wing in place.
Step 6: V-Tail Construction
The V-tail consists of three components namely the tail surface, control surfaces and V-tail mounts.
Initially the tail surface was constructed as shown below with 1/4” and 1/8” square balsa sections with dimensions of 6” x 6”. The structural design of the tail surface was not decided ahead of time. It was an iterative process and designed such that it was rigid enough. Wood glue was used to join the pieces together allowing it time to dry and us to have time to move it around which is not the case with CA glue. It was then covered with aluminum foil and clear tape as I did not have access to monokote film or the heating iron to cover it with conventional techniques. After running simulations, I found that static margin to trim was not large enough and had to be improved. This was done by adding depron foamboard cut out extensions which were then glued onto the tail in order to increase its aspect ratio and surface area. The final dimensions for the tail surface are 10” x 9”.
Using 1/4” thick balsa wedges and 1/4” plates, control surfaces of dimensions 3” x 6” were constructed as seen. The edges of the plate were rounded out using sandpaper so as to not bind when rotating. About 1" from the end of the control surface (tapered edge of the control surface which mounts inwards of the fuselage) control horns were mounted and holes drilled in order to mount them with nuts and bolts. Corrugated plastic was cut to form small 1” x 1/4” pieces and creased to function as hinges. Slits were then cut into the trailing edge of tail surfaces and the rounded leading edge of the control surfaces where these hinges were inserted and glued in place using CA glue.
The V-tail mounts were constructed on Fusion 360 and 3D printed such that they had a separation of 100 degrees and arms of 2” to support the tail surface. Once the V-tail mounts had been glued onto the fuselage, mounting holes were drilled into it and and the control surfaces to provide a rigid mounting point. 1/4” diameter pine wood dowels were used in order to align the tail surfaces with the V-tail mounts and glued in place.
Step 7: Adding Servos to the Fuselage for V-Tail Control
Four 1” x 3/8” x 1/4” plates were cut from the 1/4” pine wood sheet and mounted and glued such that the servos were held in place allowing the pushrods to reach the control horns on the control surfaces at the tail. Once these were glued in place, a hand drill was used to drill out suitable diameter holes to screw the servos in place. A truss structure was constructed to provide support to the plastic housing on pushrods to avoid them flexing when under load.
Step 8: Landing Gear
The landing gear was bent using a 1/16" spring steel rod into a suitable shape with a wheel separation distance of 14". Collets were used to hold the wheels in place and 3D printed parts were made to hold the landing gear on to the fuselage however, after testing, this landing gear turned out to be too weak and I ended up bending a 1/4" x 1/8" rectangular section of aluminum of 26" length into shape and used it instead. A simple google search will find you many results on how to bend your own aluminum RC landing gear. The link I used is below
Step 9: Wiring and Radio Set Up
Every RC manufacturer has a different color coding for wires so it is suggested that you follow the manufacturers guidelines on wiring, however, here is how I went about wiring mine -
First I soldered 22AWG wire to each of the servos to ensure that there was sufficient wire to reach receiver which was to be mounted in the electronics cage up front. After that, I ensured that I plugged in all the wires to the correct channels (1 - Throttle, 2 - Elevator, 3 - Aileron, 4 - Rudder, however, these may be different for different systems) and the motor and ESC wires. After powering on the system by connecting the fully charged battery with the propeller disconnected, I centered all the servos - trimmed at neutral and adjusted the length of the pushrod and position of the servo arm such that all control surfaces were neutral at mid stick. I also checked the rotation of the motor, and turns out it was spinning in the right direction. In the case it is spinning in the opposing direction and producing thrust in the wrong direction, switch out 2 of the wires of the three running from the ESC to the motor (of course after making sure you have mounted your propeller in the right way).
I then proceeded to set up a V-Tail Mixing function on my radio, enabling me to mix rudder and elevator together. I ensured that I was getting 25 degrees of throw on all control surfaces and that none of the control surfaces were binding.
I recharged the battery and proceeded to find a suitable flying location.
Step 10: Get Ready to Fly
While installing the rocket payload, fill a balloon with the required amount of water while it is inside the bottle, tie it and anchor it to the mouth of the bottle and close the cap. Then proceed to mount it under the wing using rubber bands. After installing the battery (not plugged in), check that the center of gravity fall at the 1/4 point on the wing behind the leading edge by balancing it by placing two fingers on either side of the wing at the 1/4th mark, if it does not balance, move the payload around to adjust CG.
Once this has been adjusted, plug the battery in and test to see that all control surfaces are moving in the right directions. The Spektrum A636 series of receivers come with SAFE technology which self stabilizes the aircraft when perturbed. In the case you plan to use this feature, ensure that it is set up correctly.
Lastly, do not forget to check your environment for the safety of yourself and others around you before you fly!
Step 11: Backing Out Data and Estimating Efficiency of Design
This design was made as a part of my senior design project at college hence I conducted multiple experiments to back out data from.
The data I backed out for my flying conditions i.e. Syracuse University Carrier Dome were the following.
Weight 3.33 lb
Thrust 1.47 lb
AOA on ground 10 deg
X_cg/c 0.19
C_L0 0.37
C_Lalpha 0.0704
C_Lmax 3.1
C_D0 0.1093
V_stall 13.4 ft/s
Load Factor (n_pos, n_neg) 3.5,-3.5
V_corner 25 ft/s
R_min 4.6 ft
Rolling Friction Coeff 0.25
Take Off Distance 25.9 ft
V_cruise 15.8 ft/s
T_cruise (D_cruise) 0.58 lb
A video of the first successful test flight with a 300g payload can be seen here incase the embeded video doesn't show up - https://www.youtube.com/watch?v=lNQlOtMqTGI&feature=youtu.be
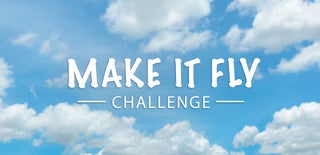
Second Prize in the
Make It Fly Challenge