Introduction: End Grain Plywood End Table With Laminated Legs
I had an idea the other week about using plywood with the ends exposed on the faces of an end table and started to think about what legs I could have on the table. I had come across a few mad looking tables and chairs on Pinterest which used strips of wood spread out at one end and laminated/glued together at the other which I thought would look ideal on this table.
One of the tables that I kept on seeing was this one which forms the top of a table. For my first attempt at something similarly large to this may have been too ambitious so a set of small legs would be a perfect start.
Supplies
Materials
Plywood for the main table
Stirps of differnet wood for the legs (I used oak and sapele as I had some already)
Oil
Tools
Table and band saw
Sander
Hand plane
Step 1: Make the Plywood Panels
I started off by collecting loads of offcuts of plywood I had in my workshop, mainly to use up them all up, as I had quite a few left over from the past few months.
I ripped the plywood to a thickness of 22mm (7/8") on the table saw and then cut them to the 270mm (10.5") long. In total I had over 50 pieces of the plywood strips.
I sorted through the plywood to find the pieces with the least amount of holes (the ply I had was not the best quality). I then sorted through them again to find the best ones which I used for the top surface.
To glue them I turned all but the last piece on it's side and glued all the pieces at the same time, clamped them together and waited around an hour to dry before unclamping and going on to the next panel. Once they were all done I cleaned then up and squared them off on the table saw.
Step 2: Make the Main Table
So for the end of the table look it's best I decided to go for a mitred joint as this would retain symmetry and look most pleasing to the eye.
I set the blade on my table saw to 45 degrees using a digital angle meter and cut the edges of each panel. There were a few places, near the points, where part of the plywood lamination had split off but I would deal with this later with the detailing/design features/mistake covering up (they are all similar and generally interchangeable for me!). I also cut a part 45 degree on what would be the front face to add a nice planned detail.
I then cut some holes using a biscuit jointer to add strength to the mitres followed by sanding the internal surface to 180 grit as this would be less accessible later on.
Once sanded I glued the edges and clamped with a band clamp and a few F clamps.
Step 3: Plan the Legs
I started planning the legs on CAD so I could visualise the proportions and angles the strips would make through the main body. After a few iterations I came up with some spacings which looked nice and which I thought I could cut without any massive chunks falling off. The gap between the bottom cuts were less than an inch so I thought that would most likely be fine.
I then transferred the measurements to the sides of the table body, marking them on with pencil.
Step 4: Cutting the Slots
My next dilemma was cutting the slots for the legs. I had a few ideas and originally decided to use a router, guiding it against a fence (clamped bit off wood). I started setting this up but it would mean that the router would be fairly high up and it didn't feel quite right. Then in the middle of setting it up I thought I'd look in to using a cross cut sled so started setting that up as well. Once it was set up, I managed to clamp and wedge the table body in to a fairly stable position, so went for this option instead.
On my cross cut sled I have slots cut for hold down clamps which really helped in this case and could generally clamp the body down and wedge two sides in to place. Some cut positions were easier to stabilise than others but I managed to cut them all safely.
To cut the slots I did two passes, the first one was quite shallow (2 to 3mm deep) followed by a full depth cut. I was hoping to minimise tear out, which I didn't get, so maybe it worked, or maybe I could have just gone full depth first of all and still got minimal tear-out?
The first slot was the worse one as the first cut moved to the main table body, so I had to reposition/re-clamp before cutting again. As it happened the second cut was slightly off so the slot was wider for the first couple of millimetres. All but one other one cut fine with no problems.
Step 5: Cutting and Fitting the Leg Strips
The next step was to set up the bandsaw to make cuts slightly wider than the table saw blade. I set the fence on the bandsaw and took several cuts on some scrap wood, making small adjustments as I went until the strips were as wide as I wanted them.
I wanted them slightly wider as I would need to sand the strips to a nice finish as part of each strip would be visible. This also allowed me to have tighter joints as I could plane, sand and test fit as I went along, it was quite laborious though. When I was happy with the fit I left that strip in the slot and went on to the next one.
I then removed the strips and numbered them so I could fit them back in to the same slot when gluing up.
Step 6: Gluing Legs - Step One
The first step was to glue all the strips in to the slots. I didn't use much glue as it wasn't required since the joints were already very tight. Any excess glue would only lead to more dry glue to contend with.
No clamping was needed either so progress was relatively swift.
Step 7: Gluing Legs - Step Two
So may plan for the legs was to have the bottom of the legs in line with the front/back of the main body.
I place a couple of timbers on my table saw (with the saw blade down) so I could get a clamp on the joining part whilst maintaining the legs and body level. I also used the timber close to the legs as a guide so clamp all the legs in the same place.
In general the method worked but not quite for one of the legs which ended up being a little wonkier than the others.
Step 8: Planing, Filling and Final Sanding
Now the legs were complete I looked at finishing the main body. I started by planning the legs strips so they were almost level with the body, followed by sanding them completely flush.
Due to the quality of the ply there were quite a few holes and due to the quality of two of my cuts there were a couple of gaps that needed filling. I decided that instead of hiding my mistakes I would almost highlight them by filling the gaps with a moisture of epoxy and black reinforcing filler.
Once dried I sanded the whole table.
Step 9: Level Off the Legs
Lastly I trimmed the bottom of the legs by placing the front of the table against the sliding table on my saw so I knew the bottom of the legs would be parallel with the main body.
Step 10: Oiling and Finishing Thoughts
All I had left to do was to oil the whole thing in hard wax oil. For the legs I had to use a paintbrush to get in to all the nooks and crannies.
As a project with a couple of firsts for me I am pleased with how it turned out but I would do a few things differently next time.
To cut the slots I'd look at using a router rather than a table saw to see if that method would results in better cuts.
When clamping the legs I would perhaps looking at doing it by eye. Maybe this would give a more pleasing overall look to the legs.
I'd definitely use a better quality plywood as I think this would really make a difference.
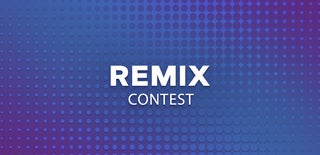
Second Prize in the
Remix Contest