Introduction: Etched Glass "Pi" Pie Pans
I like good food and bad puns. Since I've been doing some work engraving glass, and Pi Day is coming up, I thought it would be fun to make some etched pie pans that feature the letter Pi. They are even PYREX brand pans. Get it? Pi-Rex?
Enough with the bad puns, let's make some fun etched glass Pi pans that will make some great gifts.
Step 1: Tools and Materials
In this case, we are starting with regular glass pie plates, and will be etching them with a custom stencil and sandblaster.
Tools:
- Sandblaster
- Computer with vector art software (Illustrator, Corel Draw, Inkscape, etc.)
- Vinyl Cutter (Silhouette Cameo, etc.)
- Xacto or razor knife
- Masking tape
- Adhesive-baked vinyl
- Transfer Paper
- Pie Pans - Mine were all Pyrex brand, purchased used at rummage sales and thrift stores for anywhere from 25 cents to one dollar.
Step 2: Design the Logo
To start with, we need to create a design using vector software. Vector files are based on the SHAPES of images, rather than a grid pattern of pixels. They are easy to resize and are what's used for CNC cutting machines.
In this case, I used Adobe Illustrator to design my pattern.
I started with a graphical web search for "Pi". When I found one I liked, I downloaded the bitmap image and brought it in to Illustrator.
In the vector art program, use TRACE, LIVE TRACE, or IMAGE TRACE (the name varies from one program to another) which will convert the bitmap image to a vector image.
Now, the stroke or fill of the new vector object can be modified. At this step, I used no stroke and a plain black fill.
I also wanted the art sized correctly for the bottom of the pan. So, I measured the pan and decided that artwork about 4" square would work well. I resized the artwork to that size.
Besides this simple Pi logo, I also designed an Apple Pi, Raspberry Pi, and Cherry Pie logos.
Step 3: Paper Preview
I've often found that it's nice to work with a real-world mock-up of parts used in a project. I usually call this C.A.D. - Cardboard Aided Design, as cardboard is a common and cheap material that's easy to work with in place of more expensive or difficult to work with materials.
In this case, we simply need to PRINT OUT the Pi image. With a black fill and 4" size, just print it out on a regular computer printer.
Next, cut it out in a circle and tape it to the BACK of a glass pie pan, so you can see the image through the front.
You now have a real-world physical mock-up of what the etched pie pan will look like. At this point, you can see if the image is the right size, or if there is anything else you have forgotten about. For example, on the back of the pan, there is raised lettering with the Pyrex brand name logo. I wanted to avoid having my Pi art over that, so I scaled the PI to be just large enough to straddle the logo.
Resize or otherwise modify the art as needed in the vector software.
Attachments
Step 4: Cut and Apply Vinyl
Next, we need to cut vinyl to use as a template or stencil in the sandblaster.
I used a Silhouette Cameo vinyl cutter to do this. The Cameo requires .DXF files to cut from.
In Illustrator, I selected my art, then turned off both fill and stroke, and selected OBJECT>UNGROUP and OBJECT>COMPOUND PATH>RELEASE. It's just a quirk between Illustrator and the Cameo software that you need to make sure the file is in it's most basic form. (You might want to use VIEW>OUTLNE, as you won't be able to see the art anymore if it isn't selected.)
Next, save the file as a .DXF by selecting FILE>EXPORT and then saving as AutoCAD Interchange File (.dxf)
Open the vinyl cutter software (in this case Silhouette Studio) and open the Pi.dxf file.
If the file doesn't open at the correct size, rescale it to the 4" square.
Because we will sandblast on the BACK of the pie pan, the image needs to be flipped (mirrored) horizontally. I flipped the image in Silhouette Studio. OBJECT>TRANSFORM>FLIP HORIZONTALLY.
Next, load a 12" x 12" piece of adhesive-backed vinyl onto the cutting mat and into the vinyl cutter. (I originally used white vinyl, but found that black or any dark vinyl works best.)
Make sure the cutter settings are correct for the material being cut (speed, blade depth, etc.) the press CUT in the software.
The CNC Vinyl cutter will automatically cut the material. It only takes a minute for a simple pattern. Once the vinyl is cut, remove it from the machine, and pull the vinyl off the cutting mat.
Peel the part of the vinyl that will NOT be used from the wax-paper backer. In this case, we are making a stencil, so we want a HOLE shaped like the letter PI to sandblast through. So, peel out the PI letter and discard it, while trying not to damage the vinyl around it.
Press transfer paper over the top of the negative PI shape. Transfer paper is basically just a big piece of masking tape. It makes it easy to apply the vinyl to whatever we are going to put it on. If you are using a more complicated design, with separate shapes that don't touch, the transfer paper holds all the pieces at the correct spacing to each other.
Peel the wax paper backing off the vinyl, leaving the vinyl stuck to the transfer paper.
Carefully center the vinyl over the back of the pie pan and press it into place. Alternatively, you could place the transfer paper - face up - taped down to the table, and then press the pie pan down on top of it. This has the advantage of letting you see right through the pie pan to more easily center the artwork.
Rub with your fingers on the back of the transfer paper to press the vinyl solidly to the glass. Then, carefully peel away the transfer paper, leaving the vinyl stencil on the glass.
Next, mask off the rest of the glass with the transfer paper you just used (instead of just throwing it away) and masking tape.
Once the back of the pie pan is completely masked except for the negative space of the Pi logo, it is ready for sandblasting.
In this step, I've included .DXF files of the four images that I used to make Pi Plates.
Step 5: Sandblasting
Sand-blasting is pretty straight-forward. The gun sprays sand, which wears away the glass, leaving a frosted effect. It's very similar to spray painting. Try to use even strokes and cover the area entirely.
The vinyl will resist the sand, and prevent the glass from being etched, leaving it clear.
Going over the piece multiple times with the sandblaster will etch deeper, as will using higher pressure on the air control. I found that anywhere from 60-80 PSI gave good results. Higher pressure can damage the vinyl stencil, ruining the intended effect.
Put the pan inside the sand-blasting enclosure and close the door. Turn on the air, check the air pressure, and then blast the pie pan.
Make sure to blast the BACK of the pie pan. I know this seems obvious, but when dealing with a clear object through a dirty window, it can be easy to get confused. If you really want to make sure to do the right side, you could completely mask the front of the pan just to make sure you don't accidentally sandblast the wrong side.
Step 6: Unmask and Wash
After sandblasting, remove all the masking. This is best done right over a garbage can. Remove all the masking tape first, then the vinyl. The vinyl may tear, and it tends to be weaker after sandblasting. That's fine, just make sure to remove it all. A razor blade is often helpful for areas of fine detail.
After the masking is removed, wash the pan with soap and water, and let thoroughly dry. While still wet, the etched pattern will not be as readable. The etching is a much brighter white when completely dry.
Step 7: Advanced Designs - Cherry Pie
My wife's birthday is 3.14 (Pi Day) and she was always a big fan of late 80's/early 90's rock.
A band named Warrant had an album called CHERRY PIE, which had very distinct album art. http://en.wikipedia.org/wiki/Cherry_Pie_(album)
I wanted to create a cherry pie pan based on that album art. I created it through the same process as the other Pi Pans, except that the art was considerably more complicated and detailed.
I downloaded a scan of the original album art, and then spent considerable time tracing it into a simplified vector art file. (Thanks to my sister for helping me with that part!)
I then cut the vinyl on the Cameo cutter. I used BLACK vinyl. It's easier to see black against the white wax paper backer and through transfer paper. The extra contrast helps with picking vinyl and placing the stencil on the glass.
The main challenge was removing the fine cuts from the vinyl. A pair of Xacto Knives helped quite a bit to get at the fine detail. You do have to take a bit more care with the counter-space in the middle of text and with any other fine lines when transferring them.
Sandblasting was the same as with any of the simpler designs.
I'm planning on baking a cherry pie in this pan, and giving it to my wife for her birthday.
EDIT: I gave it to her. She laughed and liked it.
Step 8: Tips and Tricks
- You don't need a CNC vinyl-cutter. Simple designs can be made with masking tape, or adhesive shelf paper and a razor knife. If you are good at hand-cutting, just make your own design!
- When and where to flip your art? Since this is on the back of the pan, the image needs to be mirrored. You could do this in your art program OR in the vinyl cutter software. Either way is fine. I did it in the vinyl cutter software as the final step before cutting. It just seemed like the logical way to do it. Just make sure that you DO remember to flip the image. Nothing like picking vinyl on album art for half an hour and THEN realizing the image hadn't been flipped! (That only happened once….)
- Watch your sandblaster settings. On the first pan I made, I forgot to check the pressure. The last guy to use the sandblaster had it set to over 100 PSI...
- You don't have to use a sandblaster. Glass can also be etched with chemical acid. I had access to a sandblaster, so I used it. I also like that a sandblaster is a mechanical, instead of chemical process, and that you can see the results instantly. There are plenty of tutorials right here on Instructables on etching with acid.
- If you buy vinyl or transfer paper that comes in tight rolls, unroll it and let it lay flat overnight. The material cuts better and is easier to use if it isn't trying to curl up.
- Come up with your own designs and patterns. Once you've done a simple etched glass project, there's nothing stopping you from designing something much more complicated and interesting.
- Fine lines and details are time consuming. I really like how CHERRY PIE came out, but it was considerably more work than the original PI PAN because it was a more complicated pattern. Patience pays off when it comes to picking the vinyl and taking it slow placing and transferring the vinyl.
- Dark vinyl works better for making etched glass than light colors. The dark will show up better against the white frosted glass and can be seen through the transfer paper. The wax paper backing on vinyl is almost always white or some other very light color. It's much easier to see black on white than white on white. Use a dark color for making your stencils.
- In a complicated design, work slow and DON'T let the vinyl you are pulling off accidentally stick to what you want to remain. It will be very hard to get off and will most likely wreck the entire stencil. Use an Xacto knife, a seam ripper, needles, or other tools to more easily get at the small pieces of vinyl. I always tried to start at corners, peel back the waste, and then move it away from my main work piece.
- Don't own a vinyl-cutter or sandblaster? Me neither. That's why I'm a member of the Milwaukee Makerspace. Members of hackerspaces join to use tools & equipment that we wouldn't otherwise have access to.
- Did you remember to flip your artwork? Yes, I already asked that earlier, but it's worth mentioning a second time. Remember to flip your art!
If you like my recycled DIY projects, you can always check out more on my blog at: http://ecoprojecteer.net
See you next time! As for me, I'm off to bake a pie...
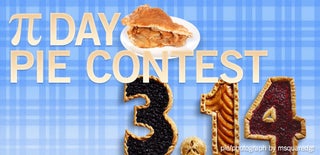
Runner Up in the
Pi Day Pie Contest
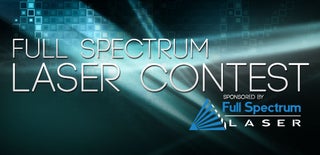
Participated in the
Full Spectrum Laser Contest