Introduction: Four Person Teardrop Camper With Cocoon
Do you want to camp with four people on a budget?
Is it possible to fit a family of four in a small Teardrop Camper?
Does a lack of "creature comforts" when camping reduce the experience for certain family members?
Do you like the easy setup and small size of a Teardrop Camper but need a bit of extra space?
If you have these questions then please enjoy my instructable on a Four Person Teardrop trailer. In this 'ible I will help with some design resources, describe the build process in detail and give some pointers for your next build. I have tackled a new feature in this 'ible - a slide-out section which allows for easy setup and sleeping room for two children. We call this slide-out section a "cocoon" because it is cosy, snug, and it transforms into something special...
I hope this will inspire you to build a Tiny Camper!
Step 1: Design Phase - Discover, Dream, Develop
There are some phenomenal design resources and support out there to help you with motivation, inspiration, design, support and resources for a Teardrop trailer. Here are some links to assist.
For a great summary on Instructables:
If you want to build a teardrop but do not know where to start, I found these 'ibles most useful and enjoyable to read.
TearDrop Build Awesome - More Awesomeness
TearDrop Build Awesome - Extra Awesomeness
It's important to think differently and evolve designs based on new requirements. I love the following 'ibles as well because they are using new / different materials to resolve their requirements with a unique design.
Using Alternative Materials & Processes - Awesome
Recycling / Balling on a Budget - Awesome
And for all things Teardrop related ... There is a great discussion board with techniques tips and advice:
Step 2: Design Phase - Requirements (Analysis) and Design (Synthesis)
I had many a cuppa and a chat with my stakeholders / customers to understand what am I going to make. This forms some good guidance for the design. Here are some of the key "user stories" that helped me build the design. I will leave it to the reader about the priority for each of these user stories!
- We want to go camping
- We want to be able to see the stars at night in our beds
- We want to be comfortable when camping
- The campsite housing needs to be easy to set up and tow behind or pack into a car
- I want the camping equipment to be all in one place
- The project should not take up too much shed space and be complete in 3 months after hours / weekends
- It should be cheaper to make (taking into account labour costs) than a solution that can be purchased. Should not cost "too much"
- We need to fit two big people and two "little" people in the solution.
This process of having a cuppa and understanding the user needs was fun. In parallel, I started some ideation and design ideas.. These consisted of internet searches, sketchbook doodling and high-level design decisions. Is this a good idea? Half way through the build, my dad had a look at the project and said "you have thought a lot about this and found out what you need to do before building the trailer. I think this is why the project is moving quickly". Thanks dad! More about this in the retrospective section at the end of this 'ible.
Some key design principles for the first design:
- 4x8 trailer to keep cheap, lean and small, fit into the trailer
- Extendable section for the two children (other options possible, but after a bit of sketching this made sense)
- the stakeholders were happy with a palette of white, brushed aluminium, plywood, orange, and black.
- Material system (Aluminium Composite Panel (ACP), Lauan + Epoxy Skin, treated pine stringers, silicone).
I spent a lot of time in the preliminary design phase to develop concepts for the TearDrop. One product I found really useful for this was the Onshape CAD package. Here is my Onshape design as a link below and photo above for you to enjoy.
OnShape Teardrop Trailer preliminary design
Why did I use OnShape?
I know Instructables has been purchased by AutoDesk, but I liked Onshape for the following reasons:
- Easy to setup - up and running within a few hours (assuming some engineering / CAD experience)
- Cloud-based - able to login from a variety of platforms and locations. Did not have to download a heavy client to each instance (PC, laptop, etc).
- Open-source - can provide this data to people who are wanting to build a teardrop trailer, just like this 'ible
- Drawings - able to model parts easily and create 2D drawings to assist with the build
- Import / Export - able to import/export CAD data (eg. GrabCAD)
- I didn't need to do an export to a 3D printer and tolerances weren't critical so this suited my needs just fine.
Armed with some side panel drawings, and with the CAD showing that everything fits! let's proceed with the build...
Step 3: Tools and Materials
Choice of tools and materials is important and covered a lot better in other Teardrop trailer 'ibles.
Below is a list of tools and materials that made my build easier and cheaper than I expected, or contributed well to the end result. If you are starting out, please look at the other 'ibles for a detailed list of tools that you might need.
Tools:
Corded drill with screwdriver bit and drill bit sets
Powered jigsaw with ripping blade and fine blade
Stanley knife (box cutter) with spare blades
Screwdriver set, chisel, socket set
Silicone / Tube gun
Hacksaw
Cheap sawhorses
Irwin Clamps - these were awesome! First time I had bought these and they were so handy. Wish I had them before this build to make some boats! The quick release and easy operation were a plus
Tie-down straps
Rotary sander and sandpaper
Materials:
Aluminium Composite Panel (ACP) in 1.2x2.4m sheets (1 silver, 2 orange at $AUD50/sheet)
1.5mm Lauan plywood (not marine grade) 1.2x2.4m sheets (5 at $AUD18/sheet)
Construction grade F17 formply 1.2x2.4m sheets (4 at $50/sheet)
Treated pine timber (90x45, construction grade) - I forget how much but it might have been 10-15l/m at AUD$2.50/m
Waterproof silicone (5 tubes)
Liquid Nails / construction adhesive (5 tubes)
Various construction screws of different lengths ($50)
Carriage bolts ($25)
Two-part marine epoxy - I used about 400mL (I had this already but this might cost $50-$100)
Door, vent and window - shop around or second hand this was a big part of the budget at around $AUD800
Polycarbonate "stargazing" glass - $AUD25
Mastic Butyl tape for sealing vent, door, window etc - $12
Aluminium siding, angle, strips, plastic hinge etc - $AUD100
Rattle can paint and primer - $AUD40 (on special)
Rail Sliders 228kg - $AUD150 whatever these people tell you it is completely false. These sliders distort and are not capable of holding the rated load. They are still "usable" to some minor extent but you will need a:
750mm trolley jack with handle - $AUD40
Jockey wheel $AUD35
hardware (lockable bolts etc.) - $AUD60
Step 4: Trailer Preparation
Harbour Freight have really great budget trailers suitable for the purpose of making a Teardrop trailer.
In Australia we don't have Harbour Freight (unfortunately).
The kind folks at Elf Trailers made me this wonderful trailer. They make trailers for Tiny Houses if you live in Australia. I'm not on the payroll, just want to pay it forward! Their prices were fair and reasonable, they were interested in the tiny house / teardrop trailer movement, they have high quality standards, could register trailers and were happy to negotiate features on a fixed budget. I would recommend them if you want a good quality, safe and strong, road registered trailer in Australia.
Since I got the trailer for a budget price, I had to prime and paint it myself. Which was fun and after a trip to Bunnings for some cheap rattle can paint, masking tape and a few days the Teardrop trailer was painted and ready for the base.
Step 5: Base Preparation, Walls and Stringers
The base of a trailer gets a lot of water, mud, dust and the like contacting the base. Unattended and unprepared this turns into rust and the like which reduces the trailer's lifetime.
Some of the preparation to prevent this:
- Prepare, spray and coat the trailer base to ensure there are no exposed steel parts of the trailer where possible
- Cut a thick plywood base to fit to the trailer base (17mm)
- Use pine tar paint under the plywood base and the trailer mudguards to provide a mud / waterproof solution
- Drill holes into the plywood base and attach carriage bolts to connect trailer with plywood base (silicone bolt and plywood for waterproofing). Ensure carriage bolt size, number and strength are sufficient for the application.
Install the walls and supports:
- Cut, clamp, glue and screw treated pine "stringers" forward and backward to allow attachment of walls to the base. Allow for a small indent so that the walls can be supported prior to screwing in the walls to the stringers.
- Using the CAD template drawing, cut out the sidewall templates to the right shape. Using the indent for the stringer and some clamps, support the walls, glue the walls (using construction adhesive).
- Cut the crossmembers to fit, clamp, glue and screw them per your CAD file. It helps having an offcut to hold the crossmember from below as you glue and screw it in place.
After this process the trailer should have the begininnings of the "teardrop" shape, walls should be up and once dry you should be able to hang off the side and shake it without breaking anything.
Step 6: Cutting Aperture for Cocoon and Cocoon Rainbow Arch
Using the CAD as a guide, mark up the cocoon aperture (opening) with carpenter's pencil and masking tape.
Cutout the opening for the cocoon with a jigsaw fine blade and if possible use this for the cocoon outside wall.
Use the opening as a template to cut out the other side of the cocoon (internal side). My kids saw this and call it the "rainbow arch". This can be used to hand a privacy curtain on the inside to seperate the cocoon from the main area of the teardrop.
It is important to be precise with your measurements in this stage (measure a number of times, use mm scale or 1/16" for my USA friends). It is also important to be accurate with the measurements (copy the template measurements across from inner to outer wall, check for the fit between parts.
Step 7: Rail Slider and Mounting
This is a tricky part of the build. Please refer to the retrospective for some improvements on this process.
The rail slider and mounting is an integral part of the cocoon / slide-out feature of this trailer.
Mark out the heights you need for the slider and cocoon, and cut some treated pine to this height (vertical slider struts)
Cut out some horizontal bridges to support the slide rails.
Glue and screw the horizontal bridges to the vertical slider struts.
All going well in this phase you will be able to slide out the sliders with relative ease.
Make sure to accommodate the sliders in your design and the CAD. If the slider mounts are too far into the trailer, they take up valuable space for the main sleeping area. On the other hand, if your sliders are too close to the outer walls, the structural integrity or waterproofing may be compromised.
A good result from this step would be slider rails that smoothly track outside and inside the trailer, bridges that add to the structural integrity of the trailer and sufficient space and headroom not to compromise the main sleeping area.
Step 8: Building Cocoon Frame, Check Fitment
Cut the cocoon base to fit and check fitment into the slider section.
Take the cocoon exterior wall from the previous aperture (or if you have screwed it up by accident cut a new one).
Take the rainbow arch wall from the previous step.
Using a similar technique for the main trailer section, cut some stringers and attach the cocoon wall and rainbow arch and attach these to the cocoon base.
If your CAD has been effective you will have the correct dimensions to use. If you do not have CAD data then make sure you take into account the additional material used by the rainbow arch and cocoon exterior wall when attaching it to the cocoon base.
Cut, glue and screw horizontal supports using treated pine for the cocoon in a similar manner to the main trailer section. You may want to use smaller treated pine sections depending on the performance and budget you need for the cocoon (to save interior space).
Check fitment of the cocoon into the main section. You will likely need a friend to help you with this stage as by now the cocoon section is a bit bulky.
Perform fitment and checking of any other structural elements (eg. the vent / window as shown above).
By now you should have a pretty great looking skeleton of a Teardrop trailer.. people will start to believe this project may be completed someday!
Step 9: Stretching the Lauan Plywood Skin
At this stage you should now have a main trailer structure, and a cocoon structure ready.
The next step is to "wrap" the trailer in a thin lauan (plywood) skin.
This plywood is very strong, light and flexible. Be sure to purchase enough to cover the trailer rolling up the short axis of the plywood (the lauan will not bend easily along the long axis).
Make sure to use plenty of silicone to waterproof the interface between the lauan, the treated pine stringers and the plywood walls.
Cut to size and screw the lauan plywood to each section of the trailer. Use tie-down straps to support and gently bend the plywood over compound surfaces.
At the end of this stage the lauan should be nicely screwed and glued across the compound surfaces of the trailer and cocoon.
Step 10: Mounting Windows, Doors and Vent
This is a fun part of the project! It is where the trailer really starts to take shape.
Measure twice and be brave! Use masking tape and a carpenter's pencil to cut out the template shapes for window, door, and vent. You can choose whatever furniture you need but keep in mind your climate and ventilation needs.
For this build the following should be of interest:
1. The cocoon has a stargazing window in the roof of the cocoon. This is made out of acrylic (polycarbonate would work) cut to size and screwed in place. Butyl tape between the cocoon frame and the window keeps everything waterproof.
2. The window and door have templates which can be used to cut out their shapes. Check for fitment. Note that the door should face the road (left side in Australia)
3. If you have checked the structural fitment the vent fitting should be easy. Cutout the lauan, fit the vent and use butyl tape between vent and lauan with silicone to get a good waterproof fit between vent and trailer.
Step 11: Galley Hatch **Fail Number 1**
Based on the CAD model, create a paper curve template and cutout a curved galley hatch strut.
Use this strut as a template to cutout another four (or so) struts.
Clamp the galley hatch struts together and tidy them up (minimise offsets) using a plane and sander.
At this stage you should have four dimensionally similar curved struts.
Use a hole saw to cut three or four orthogonal holes for dowel to fit across the curved struts.
Cut the cross sectional members (dowel) to size, glue and pin the dowels into the curved struts.
Cut some plywood for each end to size, glue and pin to the curved struts.
Check for fitment to the Teardrop trailer at each step of this stage.
Using the same technique for the walls - cut, strap and glue some lauan skin to the galley hatch.
At the end of this step you should have a structurally sound Galley Hatch (with a skin).
**Fail Number 1 - it's fun to problem solve during a build. Originally I had thought of using square aluminium angle for strenght as cross sectional members. The plan was to create an interference fit and tap them into place. This did not work. The aluminium tube interference fit cracked the curved struts. Using the dowels as a cross sectional material worked (but this meant a re-build and reassessment of the galley hatch frame). Such is life! ***
Step 12: Epoxy Lauan
To keep the lauan skin waterproof, some sealer is required.
From previous projects involving boats, I decided to use epoxy resin to protect the lauan.
Please use PPE* when using epoxy! It is very important to protect your health. PPE should include disposable gloves, respirator, eye protection, hair net/scarf/hat, long sleeves and any other risk mitigation you can think of to minimise epoxy exposure.
Mix epoxy in the required ratio, and roll the epoxy onto the plywood. Make sure you allow the epoxy to soak in and soak up any drips. Cover any areas that may be exposed at least twice.
Once the epoxy has dried, paint the timber with a shiny / gloss varnish. At least two coats will make it look shiny and keep the trailer waterproof.
*PPE - personal protective equipment.
Step 13: Wall Lining in Aluminium Composite Panel (ACP)
The side panels are lined with Aluminum Composite Panel (ACP).
ACP is wonderful stuff! it is essentially two thin layers of coloured aluminium, forming outer layers of a polymer sandwich. The ACP is covered with film on the outer side to protect from scratches and damage.
ACP can be cut with a jigsaw or stanley knife (box cutter), siliconed and screwed into place and provides a lovely finish.
My weapon of choice for the ACP was the jigsaw for rough cuts followed by the box cutter for internal cuts. The box cutter took about 10 cuts to break through but this made it easy to follow internal cuts (such as the door opening or cocoon opening).
You can use aluminium angle and silicone to reinforce and trim the interface between the ACP and lauan (edges). I had initially wanted a brushed mill finish but the supplier gave me white angle by accident which ended up looking ok.
Keep the ACP film on to the very end to protect your snazzy look and investment.
After this stage you should have the ACP siliconed and screwed in place to the sidewalls of the trailer. The ACP will look good and provide some sidewall insulation to your trailer.
Step 14: Mounting the Cocoon *Fail Number 2*
ACP in - Check.
Sliders in - Check.
Opening for the cocoon - Check.
Cocoon assembled - Check.
Arrghhh!!! Why can't the cocoon fit into the opening!!?!?!
**Fail Number 2** - Tolerances.
I had initially allowed for a tolerance between the outer edge of the cocoon section and the internal opening of the trailer of about 2-3mm. This was way to optimistic, only some of the parts of the cocoon fit this tolerance.
Thanks to some help from a dear friend to lift the cocoon, we were able to identify the problem areas where there was an interference fit between the cocoon and the trailer.
The overall gap was now about 5mm between trailer and cocoon and it slid through nicely without leaving too much gap.
For next time, I would take some more care to align the gaps to within 2-3mm (very tricky) or acknowledge this was the issue and have a friend on hand to help me lift the cocoon in place and work out the areas of interference.
1-2mm in 2m is quite a small tolerance and if you were to tackle this tolerance lots of things add up (the level of the floor etc).
Step 15: Mounting the Cocoon 2 *Fail Number 3*
Phew! my friend and I now had the cocoon sliding dandily in and out of the main trailer.
Oh no!! there is now an offset between the top and bottom edge of the cocoon when it has been slid in place..
See ** Fail number 3** below.
Once this was resolved, some ACP could be cut, glued and screwed to the cocoon with about 50mm extra material to the edge. Using D-strip rubber strip and some clamps, this now makes a water / weatherproof seal when the cocoon is closed (inside the main Trailer). When the cocoon is open, some weatherstrip between the cocoon surface and the trailer keeps the weather out.
**Fail Number 3***
The horizontal rails with the slides were about 20mm offset from horizontal. I suspect this was due to an incorrect datum or moving of the walls from square during the build of the horizontal rails. This meant that the cocoon was sliding in and out at an angle to vertical and there was a 20mm offset between top and bottom of the cocoon when slid into the trailer. This was not cool as the cocoon was not flush! To fix this issue I had to remove the cocoon, trim the vertical struts from the rails, remount the rails and check for a better level. Once this was done the cocoon was flush with the trailer wall when the cocoon was locked away.
Step 16: Galley Installation
Armed with a complete galley hatch, the next step is to construct the galley.
This is well described in other 'ibles, but here are some of the steps I followed to complete the galley.
1. Mount the galley hatch into place.
2. Cut the galley hinge to the right size and length.
3. Clamp, glue and screw the galley hinge into the galley hatch and the main trailer wall.
4. Weatherproof this section and check for fitment and leaks.
5. Attach aluminum weatherstrip to both sides of the galley hatch
6. Measure, cut and attach the back of the galley (made out of ACP cut to size).
7. Cut a box shape out of thick formply and make an internal box to house the galley kitchen.
8. make the galley kitchen frame out of aluminium square section and a plywood table top.
I did not want to go overboard with the galley kitchen, but rather use it as storage space for camping gear. At a later stage once we have been using the trailer more then I will refresh / update the galley frame. The other limitation is that there is limited space for a galley kitchen and cocoon on a 4x8 trailer so the galley section was more for holding camping gear than as a full-blown ready to use kitchen.
Step 17: All Done!
And that's a wrap!!
The Four Person Teardrop Trailer was ready after 3months of after-hours activities to get it ready.
We will use it for camping a couple of times and then look at fine tuning the performance.
To summarise, here are some of the features of this TearDrop trailer:
- Fits four people in a small size (4x8') by the use of a slide-out "cocoon" section
- Use of Aluminium Composite Panel (ACP) and lauan plywood to keep the trailer looking stylish and costs low
- Use of a 12V "jump pack" to provide power for a weekend and charge from the car lighter socket
- Described the design and build process in detail.
On the next step I have some ideas for the next iteration.. hopefully yours!
Step 18: Electrical / Wiring Schematic
A few people have asked me about the wiring for the teardrop trailer and how I did this.
Previous teardrop trailer designs I've seen often have massive battery banks, solar chargers and the like which are bulky, expensive and need a lot of expensive wiring.
In keeping with the "tiny teardrop" approach I used some system engineering principles to complete the wiring.
These principles are:
- standardisation: for Power I used USB and 12V cigarette connections
- modularity: the USB connection and 12V allows me to easily gang up different appliances
- fail-safe: if the main power goes, the 12V parts can be connected to the car USB/12V system via an "extension cord".
- re-use: the power pack is a "jump starter pack" which is a lithium ion battery to provide nearly 60Ah to supply the trailer. An example is here: 12V jump pack. These jump packs can easily be recharged by the car, or "shore power" (mains). This jump pack is much lighter (10x), cheaper (5x) and smaller (5x) than other SLA battery solutions. The disadvantage is that it will not last as long without recharging. This is not a problem for us as we are only away for a couple of nights before we need to recharge, and can use the car for this purpose.
Another option could be solar re-charging of the jump pack.
I have attached a system level schematic, the wiring consists of 12V cigarette lighter cords and USB cables.
Step 19: Retrospective
During all projects it is a good idea to reflect on what could be improved or done differently.. Here are some ideas to help with your Teardrop trailer project.
* For the slide-out section, I would move the rails to be more vertical and higher. This would allow for more space in the main trailer cabin and a gentle curve in the cocoon section.
* Overcoming the project fails means being more precise with the measurements and levels to avoid floatout in the cocoon section, and not using aluminium as an interference fit with plywood (gluing the dowel worked better).
* Thinking about the design and CAD time saves time and money during the build phase.
* Creating a minimum viable product (MVP) that meets the main requirements is important. The main thing is to enjoy camping, there can be refinements and add-ons at a later stage (eg. painting the inside and curtains).
* I would love to see a different approach to solving the problem of a four-person teardrop!
Thanks again and enjoy this 'ible and your own Teardrop journey.
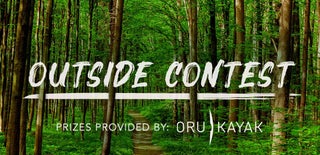
Second Prize in the
Outside Contest 2017