Introduction: Life Size LEGO Batman Movie Batmobile
Black and Yellow, Black and Yellow.....
So the LEGO Batman movie came out this year. My son has been dressed up like Batman for the last 6 months since the movie. I wanted to create a batmobile that was big enough for him to look proportionate to it. I set out to create at 1' from 1" scale from the LEGO model of the Batmobile Speedwagon from the movie. Oddly enough, when I asked my son what he wanted to be for Halloween as he is sitting in the batmobile, he says Iron Man. Kids......
Below is the final results of my build with as many details as I remembered to photograph, and it is very picture heavy.
The build will be used this year for Halloween. First at East Harbor State Park for the Family Friendly Halloween campout which was on September 28 - October 1, and then be transported back to my yard for the rest of October. Following Halloween, I have to find a place to store this beast of a build. It ended up 12 feet long, 6 feet wide, and 6 feet tall at the tip of the wings.
I have to say thanks to my wife for putting up with me during the build. She took care of our two little ones while I was working many hours in evenings and on weekends. She is the best and I couldn't build without her.
I am entering this into the Halloween contest so if you find it fun, please vote for me. If you find something else fun, vote for that. Great competition is what makes a contest awesome.
Step 1: Tools and Supplies Needed: Lots and Lots of Tools
This build tested my tool collection. I had to cut, sand, shape, route, melt, heat, bend, plane, joint, paint, fill, spray, smooth, and glue. To accomplish this, here is a short list of what I used.
Power Tools:
Table saw
Drill press - drill bits, hole saw bits, forstner bits, even router bits
Belt sander
Hand sander
Multimaster tool (FEIN)
Joiner
Planer
Band saw
Miter saw
Hand drills
Angle grinder - with sanding discs
Jig Saw
Scroll saw
Router
Air compressor and nail/staple guns
Hot wire foam cutter (Homemade)
HVLP paint gun
Woodland Pro hotwire mini cutter (4" max)
shopvac - oh so much dust
Dust collector
Hand Tools:
Japanese hand saw
Chisel set
Drywall saw
Hot glue gun
Sanding pads
Razor blades
Paint brushes - all sizes even mini lettering brushes
Caulk gun
Tape measure
Speed square
Framing square
solder iron
wire crimpers/cutters
wood clamps
weights and ratchet straps
Pro foam gun
Soldering Iron
Torch
razor blades
cutting shears
Supplies:
LED lights, wire, controller and power supply - HolidayCoro.com
Shrink solder sleeves
Solder and shrink tubing
Tires - real tires for UTVs or Lawn mowers
Bolts, screws, metal brackets
Foam, tons of foam blocks/ sheets
1/2 , 1/4, 3/4 plywood
2x4s
Plexiglass - 1/4 inch
PVC - 1, 1 1/4, 1 1/2, 2, 3 inch, 3 inch clear,
Bamboo skewers - holds the foam together
Glue - many varieties
PL300 - foamboard caulk/glue
Spray foam - pro version great stuff
foam gun cleaner
Silicone and latex Caulk
Paint - grey, black, yellow, red
Specialty paint - Sherwin Williams Peel Bond
Translucent red, blue, and yellow - Duplicolor
Odds and Ends
Candle jar lids - the flat ones which are so hard to find apparently
3" cardboard tubes
old plastic seat
Step 2: Base Frame and Tires
Tires:
I have two types of tires here because I couldn't find 4 of the same. I wanted 4 tires from a Gator UTV but could not find a dealer with spares or old tires to get rid of.
I bought both sets of tires off of Craigslist. They are 25-13-9 and 26-12-9s. Both will be ok overall but if I could I would have used 4 of the same. One tire has a sidewall tear. I patched it, sealed it with the green goo stuff, and covered the outside with silicone. It still leaks and I fill it each day sigh.....
Base Frame:
The base frame is about 7 feet long and 22.5 inches wide. The fenders and tires add the extra length and width to bring it closer to 11 feet long and 6 feet wide. I used 1/2 inch plywood for the frame and 2x2s for the supporting structure.
The rear fenders are angled at 30 degrees. Originally I wanted them to come off for the ability to move and transport but they had too much torque on them so I permanently attached them.
Each fender is 7.5 inches wide and 22.5 inches long, before the foam details are added. They were mostly 2x2s half lapped at the joints for strength to withstand the pressure of the whole build and the tires attached.
Custom pieces were created with 2x8s and plywood to support the tires. Hubs or rotors or whatever you call them were cut to attach to the inside of the rims using the bolt patterns. A hub cap then screws through each rim into the rotors with a lag screw. The front of each hub stick past the rim by about an inch.
Step 3: Fenders
I built up the fenders next as they were already attached by framing to the build and I wanted to get them to the point of running the electrical wires through them. The framing was covered in 3/16th plywood (underlayment board). I cut the plywood to mirror the foam to be shaped on the top to fill it in. This allowed me to use the hot wire cutter and run it against the plywood giving me a clean even cut. Individual foam blocks were cut, shaped and added to the wood frame to give it the detail needed. The front and rear fenders are similar but slightly different.
I used a router here to get the front face plates on the back fenders cut out. Hand work on a router through foam is sketchy. I did cheat it a bit in the future steps using a hole saw bit first to get the round shapes done first. I didn't notice I was missing the face plates on the front fenders until I was painting. I couldn't figure out why I had a yellow block showing on the model but my son kept telling me it was there and needed painted. I went back to the assembly sheet and found I had omitted the pieces on the front fenders. I cut them out, painted them separate and added them on as one of the last pieces to the build.
Step 4: Beginning Foam Work
The main body foam had to begin at this point. I couldn't attach it yet as I needed access underneath for wiring but the biggest block was cut at 22.5" x 85" and 8" thick. The block needed shaped from there to cut into areas for relief cuts in the final look. I used a router bit to get 3/4 down and then a flush cut bit to cut in 2 1/2 inches. But the relief cut needed to be 3 3/4 inch in. No bit I had could cut that so I traced it out and used a Japanese hand saw to cut in the rest, sanding down the best I could to even out the pieces.
Grooves were cut in for the exhaust pipes to go in place with a plywood jig and hot wire cutter. I cut them all the way across so I could support them with a full section of pipe. I didn't do that though. I ended up using 6 inch pieces as support and left the centers open. This allows fog to flow through the exhaust pipes with a 1200 watt fog machine.(later step)
The side panels were next and the top of the hood. Each piece is cut separately and glued into place. To hold the pieces while the glue is setting, bamboo skewers are used. They minimally damage the foam and if you push them in past the foam face, you can leave them for added stability.
Step 5: Electrical
The Batmobile has 4 main headlights, 2 side yellow lights, 2 lower fog lights, 2 rear tail lights, as well as lighting in the cab and some specialty running lights front (yellow) and back (red).
I used LED square waterproof modules from Holidaycoro, what they call dumb LEDs meaning they can't be used with DMX control systems. I ran them with a 44 key remote/ receiver which allows me to change colors if I wanted or fade in and out white. The red lights had both the blue and green wires cut so they would only light up red making the rear lights more vibrant.
Each light has one LED module in it and they are wired together to the control unit housed inside a front fender.
The wires were run before the foam was attached so it would all be hidden.
The specialty lights were added later when the foam work allowed.
In total there are LED 25 modules.
4 clear headlights
2 yellow side lights
2 red tail lights
2 clear fog lights
2 yellow running lights front
2 red running lights rear with 2 modules each
9 modules in the cab to light it up.
Step 6: Body Shaping
Once the main structure frame was built and wired, foam work starting to build out the sides, front and top. The rear engines/ fins were last. I focused on everything from the cab forward. I used a combination of pink and white foam. There is not rhyme or reason to one foam over another. It depending on the size I needed. If it was 1.5 inches then I used pink as it came that way. Everything else was cut from the 8 inch blocks, and some 5 inch foam I had as well.
I found density in foams mattered a lot. I had some 2 inch white foam that just broke apart anytime you cut it or shaped it. It was packing foam from some item my work got in several years back. I had super dense white foam that used to be a cap on my attic. Most of the larger foam sheets were a medium (60 psi compression) density but hard enough to do the job well. The pink foam shapes nicely but peel easy on the outer layer. That means that glue is only as strong as a micro layer of foam. Lots of bamboo skewers were used to try to counter the foam from shifting and tearing that micro layer.
Step 7: Plexiglass - Windshield and Running Light Covers
I started with a half sheet of 1/4 inch plexiglass, (Polycarbonate). This was from old stock, over 10 years old sitting in a hot building. The plastic protective coating adhered to the surface with tenacity. I tried everything to get it to come off. boiling water, heat gun, torch, de-greaser, engine cleaner, stripeeze, denatured alcohol, and nothing worked. Several of those ate the plexiglass edges but not the protective film. I ended up using a disposable straight razor blade for shaving, and carefully as I could took off the film. It left some lines and micro scratches but was good enough for what I needed. Scraping it off took hours.
The Plexiglass was cut using a carbide tipped table saw blade and a special blade for a jig saw designed for plastic. Once cut and then scraped, I marked the lines I needed to bend it at and used a combination of hot wire under and heat gun on top to bend the angles required. The hot wire got too hot at the end several times and bubbled/ turned white the plexiglass. Overall, it came out ok and I am happy with the result. It was then painted yellow to match the model. Duplicolor Metalcast was used to get the translucent look.
I used a headlight restoration kit my neighbor had and spent 45 minutes trying to remove the micro scratches. It removed most off of the biggest portion of the windshield but gave it a slight haze I couldn't remove even though it was beautifully polished. It just wasn't quite as clear as the rest so I stopped there and called it a day. 8 days later my son (he is 4) found something with a sharp point and made nice circles all over the front of the windshield. It now looks worse than when I started but I figure that was his addition to the build.
Step 8: More Body Shaping and Details
Progress on the body shaping. Lots of hours cutting and shaping the foam to look just like the model.
Step 9: Fog Machine and Drivers Seat
After starting the project with the intention of it only being a prop, I sat my daughter in it for a picture for scale reference. I quickly figured out I could carve out the center of the main foam block and my son could sit in it as well for a real photo op. I took about 5 inches of the 8" thick foam out of the center and put in an old plastic seat. This allowed for his head to sit low enough to clear the top when put in place. His legs are small enough as well that they stop 5 inches before the center support and fog chamber cavity. Being in the 5th percentile for growth is finally paying off for him.
The fog machine had to be lowered as well. I needed 9 inches in height to clear the hood. I carved out about 3 inches of foam to recess the machine down. Foam was then added to create a smaller chamber for the fog to go funneled directly to the exhaust pipes. At first all the fog hit the end and went out just one or two pipes, i added some spray foam to close off the end pipes a bit to force the fog through some of the others. I may add more baffles yet to direct it a bit better. It will be trial an error to get the spray right.
Step 10: Wings and Engines
The main engine block started out as 15" x 15" x 13.5". It had 3 more additions to go on it, plus the wings/ fins on top. The main block needs supported to hold the weight of the rest of the build up. 3/4 inch plywood was added through the cab frame to support the weight and add stability to the engines.The bottom piece is accurate to the model but the top is not so it was hidden inside the engine. The top of the engine was cut off to add a slot to for the top plywood engine support. It was then notched out to allow a wood piece to attach the wings/ smaller engines above as well.
The engine top was then reattached. The side engines/ wing assemblies are set on a piece of plywood (3/4 x 7 1/2 x 34 1/2). The engine block and the fins/ smaller engines are removable for transport.
Each smaller engine is 7 1/2 inches in diameter and 18 inches long in total, but are made up of several smaller concentric circles and pieces.
The wings or fins are made of 1/4 plywood - (2 sheets glued together) and PVC tubing cut in half, notched, and filled where needed. The wings are 22 inches long and 15 inches high including the supports.The base of each wing had a 2" x 1 3/4 inch x 9 inch support block added. This allowed for the wings to attach to the engine mounts with a screw and come off for transport. I used some left over butcher block counter top for the support blocks. The hard maple would support the weight and not split when driving screws through it.
Step 11: Devil in the Details
I wanted the replica to be as accurate as possible to the model. I tried to not miss a single piece that was visible from the outside. The micro details in this build to make the pieces look identical to the model took some serious time and energy. Painting will also showcase the detail as well as I will paint each block to look like the model including the odd jut outs and angles the blocks have as they are pieced together.
During the build, I needed a 15 inch batarang for the front. My son told me I needed 3 more, 2 for batman, and one for him. I made him a flexible but hard foam batarang a couple days later. He woke up, saw the batarang, didn't pick it up but dressed up like Buzz Lightyear and played space ranger all day. Yep.... 4 year olds....
Step 12: Sanding, Filling, Painting, Sealing
The foam had to be smoothed as much as possible. White foam is bead foam, where it tears out, sometimes easier than I would like. Any tear out had to be patched. Once patching was done and the surface sanded, areas also needed filled to make it look smooth and not like foam. I used Alex Plus caulk for most of this. The majority of the whole surface of the build was skimmed with caulk, watered down a bit with a spray bottle after applied. It was then tooled smooth. This helps to hide the fact that almost all of the build is foam. Anything that was foam or wood was then painted with a thick layer of Sherwin Williams Peel Bond primer. This is a extremely thick build up primer designed to smooth out surfaces where paint has chipped on houses. It is the consistency of ketchup. It also smooths the surface of my foam to get closer to a plastic look. I couldn't afford the epoxy coats as they are over $100 a gallon and my build would have taken 2 or 3 minimum. To cover the build, it took about 1 3/4 gallons of the primer. Most of it was sprayed on through the HVLP sprayer but it didn't spray well and many of the surfaces needed touched up.
Once the primer was done, 2 layers of a black base coat was next. Several areas were taped off to keep the black paint from getting on surfaces which would end up a lighter gray. The HVLP spray gun worked beautifully here. It covered great and left minimal work to be done with a brush for the black base coat. The rest of the colors had to be completed with a brush. This included light gray, dark gray, yellow, blue, and red. The metallic gray for the exhaust and the blue for the engine cap were spray paint.
Hand lettering was then done to complete the sticker set (Graphics). This included the bat symbols, letters, and pin stripes. - Separate section on that.
The cardboard had to be sealed to keep it from getting wet and falling apart. Luckily I have extremely minimal cardboard on this build. Only the upper and lower guns had it. It was sealed with spar urethane finish, primed, and painted.
Step 13: Recreating the Graphics (Stickers)
With the exception of the license plates, all of the stickers were hand painted. I used a cut out of the bat symbol to help with repeat-ability on the sides/ hub caps. I also printed the graphics full size on 11x17 paper to trace into place with pushpins, hand-cutting for patterns, etc.
The license plates I printed out from a high res picture I took and laminated. These were then glued into place on the front and back.
Step 14: Fails, Retries, and Different Directions
6 inch clear tubing - I needed 3" clear rings for the headlights but I didn't have the 3" clear PVC. I had 6 inch Clear PVC so I cut it down on the table saw and miter saw to get the length I needed. I then used a heat gun to melt it into shape. It didn't work well as the plastic would mis-shape or melt unevenly. I did end up finding a scrap piece of clear 3" PVC instead and used that.
Hand shaping round pieces - Several of the foam pieces are round on the ends. I drew out the round shape and tried to hand shape some and use a belt sander on others. Neither worked well. I ended up using a band saw which worked well and allowed me to smooth with a sanding pad later.
Hot wire foam fails
Wire types - There are so many types of wire. Welding wire was used for longer runs as the resistance would hold the heat. .010 Nichrome wire was used for short runs (less than 16") as it was thinner diameter so more accurate cuts. I couldn't get long runs of it to heat up though so I was limited in it's use. The welding wires would break on short runs under 24 inches as it would heat up too much no matter how I adjusted the DC dimmer. It also would heat up to red hot on the ends not going through the foam which would melt the foam on the edges as the heat build up had to go somewhere.
Tension - As the wire heated up, it elongated even if it says pre-tensioned. This allows for way too much wiggle room when trying to cut a square edge. Many times when I didn't adjust it enough as it was heated up, I got an angle cut of 5 degrees or more which over an 8" thick pieces is off by a 1/4 inch.
Square - Keeping the pieces square required the right tension, a good fence to run the pieces against as well as supports on both sides for long pieces coming through the wire. Many tries and fails, and even at the end on my last pieces of foam I cut, it didn't always work well. I love the hot wire cutter. I hate its constistency or lack there of.
Plexiglass
Plastic film removal - The plexiglass I had was old stock. It was at least 10 years old and still had the protective plastic film on it. I scraped it off with a razor blade but it left micro scratches. If I had to do it again, I would not deal with the scraping and such but would just buy new. It just isn't worth the hassle.
Bending - I bent the plexiglass with a hot wire under and a heat gun on top. I tried to use a coil wire from a hair dryer. It sparked and shorted out and tried to catch my basement on fire. Yeah, that one didn't go well. At least I had it on a switch so I could kill it from a distance knowing it may not play nice. I then used my hot wire from the foam cutter with welding wire in it. It heated up nice but then got too hot at the end and discolored the plexiglass right as it was at bending stage. I just never got this one quite right.
I mis-glued a piece in place on the hood of the batmobile. The air intake was 1.5 inches too high or one block of foam. It looked off from the moment I made it and I didn't figure it out until I had primed it. I cut out the whole section with a Japanese hand saw and lowered it the depth it needed. Now you can't even tell.
I painted so many areas the wrong color. I thought I had the block height right and was off or used the wrong color for the wrong area, but they there are a ton of pieces so I was bound to make some mistakes.
Step 15: Character Additions
I started out wanting to create 9 mini figures to go with the display. They were going to be the popular characters from the movie. I finished Batman, Joker, Harley Quinn, Robin, and Bat Girl. I also made Robin's pants as he rips them off in the movie. Since I had 9 to make, I made some plywood jigs to cut out several pieces over and over with the hot wire foam cutter. Lots of hand painting to get the details right.
The head pieces were made from wire, foam, paper and tape, cloth covered in caulk or paint, and foil. Anything I could use to get the design as close to the model. I like how all of them came out but the joker. Looks like he has an afro hair day. Oh well, I like him with an afro. :)
If I get the time later this month I will complete Alfred, Superman, the Condiment King, and Catwoman, as well as Harley Quinns hammer and roller skates, maybe even a few more Batarangs.
Step 16: East Harbor State Park
Traveling with the Batmobile on a trailer was interesting. I had an hour and half drive on highways to get to the park. So many people slowed down and tailed me to see what I was hauling. I did end up with AUTHENTIC BATTLE DAMAGE!! on the way there. I had some pieces to fix, paint, and reattach when I got there. I had to stop 4 times for pieces that I saw come loose or get ripped off to rescue them when things shifted. Luckily I didn't lose any as the netting held it all in place. Still not fun driving though.
I got all of the gear and Halloween stuff on a 16 foot x 8 foot trailer. I used every inch of it plus my whole truck loaded down.
This year we stayed in C181 at East Harbor, and used the adjacent Cul-de-sac to set up in. This allowed for 360 degree view of the display as kids walked around which also meant I couldn't hide details or technical set up behind a curtain. I used a plastic black bin to cover the stereo at times.
We set up a projector and showed the LEGO Batman movie on a 120 inch screen. We had kids camped out in chairs and blankets the whole movie.
We took first place at our weekend for electric sites. Everyone seemed to connect with LEGO Batman. I dressed up as the joker and used an afro wig sprayed green to match the joker I made. Gotta be consistent.
I hope you enjoyed my project. Have an awesome day.
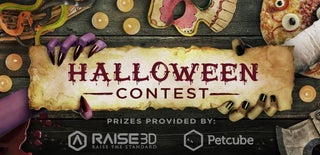
Second Prize in the
Halloween Contest 2017