Introduction: Rubber Band Powered Aeroplane
This one has a balsa wood frame structure but other wood can also be used, provided that it is thin and lightweight. (I used to make the frame from chopsticks cut to size.)
To make one of these you will require: (most of these should be easy to find at home)
- Foam (I use the kind of polystyrene foam found in food packaging)
- Wood (I used balsa about 1.6mm thick)
- Wire/pin/paperclip for propeller shaft (and tailhook if you prefer wire to aluminium can)
- Aluminium can for tailhook and front strengthening.
- Glue
- Tape for foam parts (Most types of glue will dissolve the foam)
- Beads (about 4)
- Plastic (from an ice-cream or yoghurt container etc.)
- Elastic/rubber band
- Tube that the wire you have can fit through easily without being too loose,( eg. pen ink tube for paperclip)
- Scissors
- Craft knife/scalpel
- Pliers
Here is a video of it:
Step 1: Frame
The first picture is really the last of this step but I put it first for easy identification of parts.
Start with the main fuselage beam, its purpose is to hold the elastic and be a bridge between the propeller and wings, as well as to the tail. It is very simple when cut from balsa, just a long rectangle strong enough to not snap when the elastic you will be using is put around it longitudinally. It can be any size, depending on how big you want your completed aeroplane to be. The fuselage beam on this one is 185mm x 1.6mm x 7mm.
Next is the basic construction of the drive system. Start this with the three new parts in the third picture, a small piece of wood (on my model about 6 x 8mm), wire/pin/straightened paperclip and a tube for it to fit into. Bend one end of the wire into a small hook just big enough to hold the elastic you will use later. To support this wire shaft, first glue the small rectangular piece of wood under the fuselage beam at the front end of it. Then glue the section of small tube under the block of wood. Slide the wire part into it to check that it can turn easily. Use picture 4 for reference to the placement of these parts.
After the above construction is complete, bend a rectangular piece of aluminium can into a tall "U" shape and glue it over the parts you just added. This will provide more strength.
For the tailhook assembly, I bent another piece of aluminium from a RedBull can in half and glued it around the aft end of the fuselage beam. You can do it like this or if you prefer, you can bend a piece of wire into a hook shape and glue it on underneath the fuselage in the same place.
To make the wing support, cut another piece of wood to 3 quarters the length of the main beam as shown in the second last picture. Divide this piece as shown in half, and then the one half in half again. Cut the 2 places you just marked and glue them in shape as shown in the last picture. Add small triangular pieces of wood at the two joins. Then glue this onto the fuselage beam about halfway along it. See the first picture for reference.
After I made the first test flight, I discovered that extra support at the base of the wing supports need reinforcing. Glue small rectangular pieces of wood on both sides of both joins to stop the wings from breaking off in-flight.
Step 2: Completing the Drive System
For this step, you will need a rectangular piece of plastic (from ice-cream, etc. container), about 4 beads, a small piece of wood to help support the propeller hub, and some foam for propeller blades.
Start with a 1:3 ratio rectangle of plastic (on this model, 15mm x 45mm) and draw lines from corner to corner. make a small hole (just big enough for the wire to fit through) where these lines cross over. This will be the propeller hub.
Make a hole of the same diameter in the centre of small piece of wood, then glue this onto one side of the propeller hub with the 2 holes lined up.
Slide 2 beads onto the front end of the wire shaft. These beads must not get glue on them because they have to spin freely. Slide on another bead, but glue it in place in front of the other 2. Slide the propeller hub (and piece of wood) onto the shaft and glue it to both the shaft and the glued bead. Glue on another bead (to the front of the propeller hub) to hold the hub in place. Clip off excess wire sticking out the front of the shaft.
To give the blades mechanical advantage, bend the propeller hub along the lines shown in pictures 3-5. I cannot explain exactly how to do it but I hope the pictures are useful enough to the people making one of these.
For the propeller blades you will need a piece of foam with the proportions shown in the 6th picture. On my model this rectangle measured 130 x 30 mm. Cut it in half on the line shown. The blades may be left rectangular but to improve on efficiency and stop the blades from hitting the support of the drive system I suggest trimming the blades to approximately the shape in picture 7.
At the "base" of both blades, make a slit inside for the propeller hub to slide in. Slide the blades on and add tape to hold them firmly in place on both sides of the propeller hub. See the third-last picture for the position of the blades on the hub.
The blades will already have an angle to them from the bent hub, but bend the actual blades too for a better "pull" and longer duration flight. See third last picture. In the last picture of this step, you can see the completed drive system.
Step 3: Adding the Wings and Tail
For better weight distribution, the elastic band does not end at the end of the tail in this model. The fuselage must be extended to provide a support for the tail. Do this by cutting another piece of wood of the proportion shown (on my model it is 80mm long), and gluing it to the top of the tailhook as shown in picture 2.
For the wings, cut two rectangles from foam each with a ratio of about 1 : 2.5 (on my model 60 x 160mm). The length of one should be 3 quarters the length of the main fuselage beam. See picture 3. Shape one rectangle and trace it onto the other. The wings can be left rectangular but the aeroplane will fly in a more stable manner if the wings are cut to a similar shape to the one shown in picture 4. Tape the two wings together (picture 5). Tape the wings on top of the wing support (picture 6).
The horizontal stabilizer must be made in the same way. The ratio of the rectangle (both fins included) is about 1 :1.5 (on my model 55 x 13mm)[length about 3/4 of one of the wings] divided in 2 so that the one fin can be traced onto the other for symmetry.
For the vertical stabilizer or "fin" make another (like the two fins you just made) and cut the bottom end of it as shown in picture 7 so it can slot into the horizontal stabilizer(Which must also be cut as shown in the same picture, so a narrow rectangle is cut out of it). They should be able to fit together as shown in picture 8.
Tape this tail assembly onto the top of the tail support beam.
Hook an elastic between the front and tail hooks and wind the propeller backwards as much as you can without the elastic snapping. Release the propeller and see how it spins before test flying. Test fly and trim/correct the surfaces so that it flies the way you want it to. Do not fly it it enclosed or crowded places and be responsible with it, it could hurt people if used incorrectly.
Happy flying!
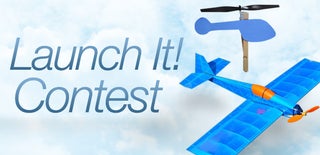
Finalist in the
Launch It! Contest
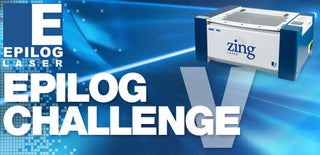
Participated in the
Epilog Challenge V
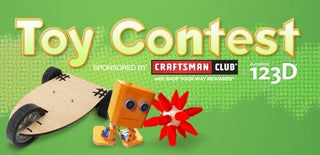
Participated in the
Toy Contest
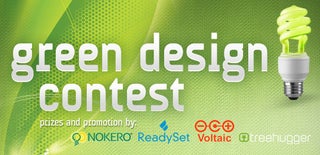
Participated in the
Instructables Green Design Contest