Introduction: Saw Pierced Hummingbird Memento Pendant
my mother passed away suddenly on the 13th and she loved many things, hummingbirds were always a favorite of hers. Sitting here wondering about things I thought to myself, instead of mourning and being down in despair...why not channel the love for her and use it for creativity? with that thought, I decided to make her a hummingbird memento pendant.
Step 1: Gathering Your Tools
main tools needed are as followed:
1.a jewelers saw with a selection of blades.( an assortment or a gross of 144 is always good )
2. jewelers bench pin aka a piece of wood with a V cut out. ( mine is a chunk of a pallet simply clamped to an old table )
3. some sort of drill and small sized bits along with a center punch and hammer.
4.. set of needle files and a few other hand files.
5. sandpaper/ emery paper or steel wool, I tend to use grits from 320 up to maybe 800 or even 2000.
6. a marking scribe and other layout tools such as a caliper divider, a compass that holds a pen or
pencil, and a ruler.
7.. last but not least, a work area, for me it is an old table that was salvaged from a dumpster..not the best but it works for no.
it should also be noted that wearing safety glasses during sawing is a good idea because a saw blade to the eye will ruin your day.
Step 2: Your Materials
material wise I am using salvaged copper and a piece of brass that was bought new, the copper itself is from old electrical lines, grounding wire, and pipes that were either found on my property or purchased from a "junk store"
Step 3: Transfering an Idea to Metal and Center Punching the Holes
once an idea has been drawn up, the next step is to transfer the design to the metal.
to do this I simply make a copy of my original drawing, print that out and cut it out with either scissors or hobby knives.
glue it to the metal, once the glue dries i go back with my scribe and trace around the template to ensure there is a solid line that wont accidentally smudge off.
once the template is in place with scribe marks made, it is now time to center punch and drill all pilot holes for the saw blade.
Step 4: Saw Setup and Sawing
This can be the part that will either lead to the most frustration or be the most enjoyable and relaxing.
the saying " slow and steady wins the race" stands true.
jewelers saws are very handy tools however their blades can be as delicate as a human hair. any quick jerk, death grip, sudden twist/ turn, or improper tensions of the blade....will result in broken blades....lots of broken blades.
saw set up steps are as followed:
1. establishing the correct side of the saw teeth, a blade put in backwards will not cut right and will most likely break. easiest ways to find out what way the teeth is pointing is to gently drag it on a fingernail or piece of fabric, if the blade catches then you know the teeth are facing the right way and should remain pointing up, if not then rotate the blade and try again. if neither side catches this indicates either a worn out blade or one of poor quality with no teeth.
2.proper tension of the blades is an important thing to learn as well, a
blade too loose with get stuck and snap, a blade too tight will break, potentially shattering and flying all over( why safety glasses are important to wear)
a proper tensioned blade will produce a pleasant ping sound when plucked as well as not breaking.
3. the grip when using these saws is not very tight either, its more so your thumb and pointer finger gently griping the handle with the rest of the hand simply cradling it for support, the saw itself should move only with a straight vertical up and down motion that remains stationary in one place, while the material being cut is moved around while resting on the bench pin.
two more helpful things to have on hand is saw lubrication( small chunk of beeswax works fine) to prevent blades from feeling " gummy" and a small brush to remove any debris that may block your lines when sawing.
Step 5: Filing and Other Finish Work
Once everything has been sawn out, it is now time to go back and true up some of the lines as well as removing any sharp burs with the small needle files.
Afterwards it can be left as is or any other details can be added.
Step 6: Optional Engraving, Inlay and Patination
These are purely optional however even a slight engraving or patina coloration can enhance the appeal of something.
For this project I chose to do a bit of engraving and some patina coloration along with a brass heart inlay into the center.
The brass heart was carefully cut out, filed and then hammered into place.
Other finish work was a light sanding and a dip into a patina solution I made.
with that said, this project is now completed.
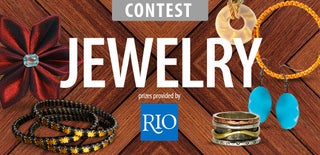
Participated in the
Jewelry Contest 2017