Introduction: Servicing and Cordless Strimmer
This happens to be a qualcast but given that name is now owned by bosch and at the time this was brought they were licencing the use of the name to homebase/argos who had them made in China probably by the cheapest supplier I suspect it going to be the same more or less to any other own brand/cheap cordless strimmer.
Step 1: Diagnosis
This can save you hours.
I was initially given this to fix with the cutter line somehow wrapped around the motor shaft, this only took a couple of minutes to disentangle, job done.
About as long again later it was returned. "it's got something else wrapped around it and won't run"
As it did indeed appear to have twine wrapped around the shaft which I couldn't remove the full strip down documented later was embarked on.
I made the mistake of assumeing the operator was using a charged battery, it wasn't. Had I checked that first this Instructable wouldn't have happened.
Step 2: Disassemble
Some photos are staged during reassembly not as I was actually removing bits, and quite a bit of the cleaning actually happens as you are stripping it down.
I started by removing the line spool, as the spool holder appeared to be screwed on to the motor shaft (as it later proved to be) I then removed the top cap with the hope of gaining access to the motor shaft to be able to lock it and unscrew the spool holder. 1screw and some gentle prodding released the cover, no access but 2 case screws and some blocked vents revealed. (Hindsight suggests fabricating a tool to lock the motor shaft from a piece of tube drilling out the screw hole to accept it and using a new screw position to secure the cap might be a worthwhile modification.) a full strip down it had to be then.
What the instruction book calls a plant guard came off first, a simple springy bit of wire, pull sideways until it is clear of the housing then up to free it, the other side then just falls out.
The line guard is held in place with a single screw the head needed picking clean with a scribe/ small flat blade screwdriver (as did the only case screw in the cutting area next to it) the guard then simply pulls out of its locators.
Locate and remove all other case fixing screws, these can sometimes be positioned under labels whilst this keeps things clean it also provides an easy indicator to the manufacture that the product has been dismantled and any guarantee is thus void. I left the one through the pivot until last I didn't want the head falling off the handle too early.
With all screws removed a gentle pull and every thing came apart, unfortunately a little too easily so I didn't get to see how the cables were wrapped/
With the casing set aside it was possible to grip the flats on the back of the motor shaft and unscrew the cord holder from the shaft. (it's at this point I should have made a proper key to hold the shaft still as this would make future cleaning much easier)
Noticing that one of the vent slots was blocked I removed the mounting plate as well to fix this.
Step 3: Clean
Most of the cleaning actually occurred during the strip down. The grime on the motor mount scraped off easily and the remains of the twine unpicked without the need for the knife. The mounting plate had been damaged at some point by something wrapping around the shaft I trimmed the vent holes back to their right shape with a sharp knife Note I'm NOT using my knee as a cutting board merely to stage the photo. I gave the motor a wipe over with a rag, and whilst the front bearing appears to be a sealed ball race(photo) the back looked to be a good sized sintered bronze / olite type (no photo and that would have been more use for identification sorry) so I applied a drop of lubricating oil to that.
Some fine grass cuttings had got inside the casing these were swept out with a small paint brush before reassembly
Step 4: Reassemble
It would be simple to say reassembly is the reverse of dismantling. Whilst in principle this is true it is never that simple. To start with you need to work out where all that cable coils into the housing and where that ferrite suppressor coil goes.
Refit the cord carrier it simply screws on finger tight the direction of rotation keeps it tight holding the shaft still with pliers makes this easier.
Note the 4 indentations on the motor mount these have to engage on the lugs in the housing or it won't close.
One half of the housing clearly had space for the ferrite and paths cut out for the cable the cable that allows for the head angel to be adjusted coils into a depression in the housing opposite the one for the locator lug on the handle. Reassemble with care making sure non of the cable is trapped between the housing and the handle as this is a tight fit and could cut the cable in time if it is jammed there. Holding the lower half of housing in position lower the top section into position the lugs in the housing have to fit into the gaps in the shaft and a slight twist may be required to get the 2 halves of the housing to align correctly, fit the pivot screw first then the rest of the casing screws. Snap the top cover back in place and refit securing screw the line guard refits in much the same way fit the line spool and cover and finally spring the plant protector back into position.
Step 5: The Motor
I've included this step partly because I've not been able to find a match for it online, and it looks to be a potentially useful motor for other applications and I strongly suspect it or its clones crop up in a lot of cheap 18v cordless tools
It drains a 2A/hr battery in 20 minutes so its drawing about 6A a search for 18v 100w DC motor brings up a lot of similar looking motors but not this actual one.
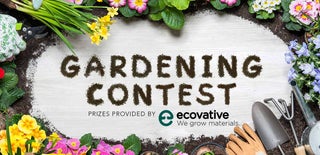
Participated in the
Gardening Contest 2017