Introduction: The 8-Bit Skull Concrete USB Hub
I didn't know I needed a concrete USB hub ... until I had one.
My newest computer has four onboard USB ports, most of which were immediately claimed by two external hard drives and an audio interface. I was in need of additional ports for a third external drive, a printer, and then of course jump drives. I searched around online, but everything I liked was an overpriced aluminum strip or block, which would just clutter up desk space. It's bad enough that I'm spatially taunted by a random drink coaster ... wait a minute ... I can combine two annoying things into one useful thing.
It just so happened that a concrete USB hub challenge was taking place on YouTube (circa 2016), which resulted in many creative designs:
Lawing: Desk orgainizer/holding thingy
Jackman: Electronic device storage shelf
Kage: Side table
At first, the idea of concrete was of no interest to me, but further contemplation swayed my opinion. A concrete coaster would be impervious to both hot and cold beverages and the weight would keep it from dancing around while inserting cables and drives. Also, it could be used to bludgeon zombies once the apocalypse happens.
For shape, I decided to go with a shallow block - just thick enough to encapsulate the USB hub.
For the actually Hub, I chose a 7 port octopus (octopod?) style. I guess the male connector counts as the 8th arm? This style allows me to distribute the ports across three sides of the block.
For design, I decided to try an epoxy inlay ... in the shape of an 8-bit skull.
Step 1: Fabricating the Form
The key to concrete casting, aside from an adequate mix, is a quality form. Melamine is a perfect material because it's sturdy and provides no "tooth" for the concrete, therefore releases the casting very easily. It also leaves a smooth and finish ready surface. I happened to have some melamine left over from when I made my large router/assembly/outfeed table.
I sliced a length from the larger sheet using a circular saw and shop made saw track. I further reduced this using the miter saw and then cut my final parts using the table saw. A sharp blade and applying painters tape within your cutting path will greatly minimize melamine chip out.
Bottom: 5 1/2" x 5 1/2"
Sides: 9" x 2".
In true BALES fashion, I obsessively laid out screw locations on the four sides. They don't need to be perfectly spaced since this is just a form, but that's how my brain works. Holes were drilled using a countersink bit and then a 1/8" bit. Within one of the sides, I drilled a recess for the male connector of the USB hub [Fig. 7]. This will keep that part outside of the final concrete cast.
I assembled the form on a flat surface and even used a clamp to ensure the sides were flush. It's a good idea to label the side which will entomb the male USB connector, so that during demolding, you don't pry on that side like a barbarian and destroy everything. It was a close call.
To finish off the form, I ran a small bead of caulk around all the inside seams and spread it nice and smooth with a damp finger.
Step 2: The Foam Skull
Since I want my finished project to have an epoxy inlay, I need to add that negative space to the mold. My initial thought was that 1/8" craft foam would be perfect, since it wouldn't absorb water and it would be easy to remove from the cured concrete. It turns out that my theory was correct.
I knew I wanted an 8-Bit skull, but I wasn't decided on the shape, so I enlisted the help of good ole Googlepants. I found a skull which resonated with my design sensibilities, so I drew it out on 1/4" graph paper. Using spray adhesive, I stuck the paper to 1/8" craft foam and then cut out the skull using a razor knife and straight edge. Spray adhesive was also used to glue the foam skull to the bottom of the melamine form.
Note: I couldn't get all of the paper off of the foam, so I left it. I should've put the paper side down in the form because it actually telegraphed a different texture than the foam to the finished concrete.
Step 3: Fitting the USB Hub
That last job before playing with concrete was assuming the role of a USB contortionist. The male plug was inserted into the melamine recess and I used a bit of hot glue to hold it in place, as well as create a moisture barrier. The remaining 7 USB ports were divided amongst the three remaining faces - 3 in the front (equally spaced) and two on each side (somewhat centered to avoid colliding with the front ports).
Each port was adhered to it's location using hot glue. To ensure consistent alignment, I cut a small wooden spacer. Not only did it's thickness center each hub top to bottom, but it provided a reference plane to keep them all square while the hot glue set.
It was a very tight fit and fortunately for me, the entire hub basically floated in the center of the mold. None of the wiring touched the sides, nor rested against the bottom.
Step 4: Concrete
With all the prep work complete, it was finally time for the concrete.
I mixed a small batch until I had a consistency which was compatible with my needs. I definitely didn't want the mix too wet and risk water finding it's devious way into the circuit board enclosure. Inversely, I needed the mix loose enough to flow around the nest of cables and fill all the nooks and crannies.
As I added the concrete, I pushed the mix around with my fingers to ensure I didn't end up with voids. I especially focused on the area under the octomess, since that will be the finished top. Once the form was full, I knocked it around to work out any air bubbles and then leveled off the top with a trowel.
Overall, I ended up with a pretty ideal mix. If your new to concrete forms and casting, I highly recommend that you check out the Concrete Class here on Instructables.
Step 5: Demolding
I should've let the concrete cure for another day or two, but I was impatient. As punishment for my haste, I encountered some crumbling along the edges, as well as around some of the USB ports. Nothing major ... more of a natural chamfer, which actually works ok with the overall visual.
The actual demolding was as simple as removing the screws, removing the sides, then removing the bottom panel. In hindsight, as previously mentioned, I should've marked the side which contained the recess for the male connector. That's the side I inevitably started with and if I had continued rotating the side downward, I could've snapped off the connector and/or a chunk of concrete.
I used a precision screw driver to work up one edge of the foam skull and then slowly removed it with my hands. It was like peeling up a sticker with the added concern of more edge crumble.
At this point, I decided not to push my luck any further, and I let the concrete have another full day to cure.
Step 6: Resin
To fill in the skull shaped void, I knew I wanted to use a tinted resin, but I wasn't exactly sure what would work.
The first attempt was with two part epoxy and a few drops of black latex paint - it was a total failure. The latex and epoxy did not play well together and set into a bubblegum consistency mid pour. It was a total sticky mess.
The second attempt was with casting resin and a few drops of leather dye, which was a successful combination.
I poured the resin into the void until it reached the top and then used a torch to release any air bubbles. Apparently, the torch also released some surface tension and the resin flowed out onto the surrounding concrete. Rolling with the punches, I decided to coat the entire top and sides with resin using a small acid brush.
I left the resin cure overnight.
Step 7: Sanding
I could've called the project finished at this point, but I wanted to level out the top a bit, as well as take down the sheen. I worked my way through 80, 100, 150, 220, 320 successive grit discs with the down draft table running and my respirator strapped on. Sanding resin creates fine dust, which you want to keep out of your lungs.
Step 8: Bottom Foam
The bottom face of this concrete block, which was the top during the casting process, was very rough. I'm sure a few hours of sanding could've smoothed it out, but that wasn't going to happen. I decided that a layer of 1/8" craft foam was the perfect solution. I used two part epoxy to glue it on and trimmed off the excess with a razor knife once it had cured.
The added benefit of the foam is that it eliminates any chances of the concrete scratching the top of my desk. Cork mat or felt seem like they could be viable options as well.
Step 9: Finishing
I added a coat of Renaissance wax to finish the concrete. It helped even out the coloring and hopefully will add a layer of protection against any condensation.
No .. I'm not worried about spilling my beer ... I mean coffee ... near my keyboard. I'm a professional.
Step 10: Glamour Shots
There we go!! A USB hub with some heft. It's actually more practical than I thought it would be. I use the remaining computer USB ports to liven up the seven ports on this hydra.
The back left port is home to the printer and a right side port is home to phone charger. The three front ports are used quite often, since I have way more thumb drives than any one person realistically needs.
One hindsight consideration would be a USB hub, which also has an SD card reader. The card slot is located on the back of my computer/screen and I use it quite often to transfer files from cameras. Having one integrated into this concrete hub would be easy to access and therefore very convenient.
Takeaways:
Even if you have no interest in a USB hub, the use of craft form for casting negative space concrete maybe a good item for the old "maker toolbox."
Hot glue is effective at keeping moisture out of electronics as concrete cures.
We also know that leather dye can be used to tint casting resin.
Step 11: The Build Video
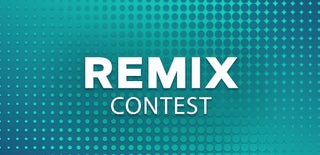
Participated in the
Remix Contest