Introduction: Bottled Beer Shotgun
The rough day at work. Most of us have had at least one ... more likely we've lost count by this point. Mine had just crossed that line where frustration turns into laughing for no logical reason ... when each new problem is more ridiculous than the last, so your brain has hung up the "Gone Fishin'" sign and left the building.
Nothing was going right ... the traffic lights on my route to work had decided to give me the red light tour, end users had managed to forget every password they had ever created over the two day weekend, the coffee machine was broken, and the clocks seemed to be running in reverse.
I'd sell my best friend's liver for a beer right now, but I might need it later ... I've been cultivating that harvest ... I mean relationship for years. I was rapidly moving into "sell my soul" territory and it wasn't even lunch time. Buckle down and keep your eye on the prize, I told myself ... an ice cold beer, a comfortable chair, and some woodworking videos await.
Walking through my front door was like crossing the finish line of a triathlon, which is really just an assumption because I don't run unless I'm being chased and if I can't see the bottom, I don't go into any bodies of water. My tunnel vision was locked onto the keeper of beer (known to some as "The Fridge") ... the prize was within reach ... and then it happened ... the words still send shivers down my spine. "We have to go ... right now."
What?!!? I had a date with beer!! We've been planning this all day (Beer and I)!! You have no idea the pain I have endured this day!! All pleading fell on deaf ears ... "Right now" reverberated though the house ... most notably, off of the closed refrigerator door. "Quick ... think of something," my brain said, which is pretty ironic if you think about it. My immediate thought was a memory from high school ... I mean college at a legal age ... the ole' screwdriver and a beer can method. Brilliant!! It could make a bit of a mess, but it's worth it and very quick, which will make the warden happy in regard to the looming deadline.
Wait a minute ... "We have a problem," I told my brain. We rarely drink canned beer ... and we surely don't keep any in the house. "No problem!! Just use a bottle," my brain retorted. It was at this very moment that I realized my brain has no regard for my personal safety and I should really stop listening to him. However ... I don't necessarily have to puncture the bottle .. I just have to add a second entry point for air ... ideally at the top. The warden turned her back, so I escaped into the workshop.
Step 1: The Initial Parts
Initial material for the construction of this device was some scrap poplar, sprinkler tubing, a PVC 90° elbow, and a section of PVC pipe.
The section of PVC pipe needed to fit around the outside of the elbow, but it was a little too tight, so I increased the inside diameter using the oscillating spindle sander.
The PVC elbow needed a 1/4 hole for the sprinkler tubing, so I made one with a drill bit ... using drill press.
Step 2: Layout and Drilling
The top and bottom pieces were made from a scrap of poplar. I laid out center lines and then measured in from the ends to find the center of my desired holes.
One side is for a 1" dowel, so I drilled out halfway through with a 1" forstner bit, and then finished the hole with a 1/4" bit.
The other side holds the bottle, so I'm dealing with different diameters. For the PVC spout, I just used a forstner bit and increased the hole diameter as necessary using the oscillating spindle sander. For the bottom of the bottle, I wanted a recess and since I don't have a fortsner bit that large (yet), I used a smaller diameter and staggered my plunges. You can see it got away from me a few times, but this isn't fine furniture. Also, using the multiple plunge method left 5-6 center marks from bit's center point. To clean up that ugly mess, I just drilled out the center.
Once all the holes were drilled, I separated the parts and trimmed them down to 3" wide.
Step 3: Dowel Handle
I cut the 1" dowel handle to length on the miter saw, which could vary depending on the type of bottle. I just snuck up on the cut until I was happy with the fit.
The 1/4" sprinkler tubing runs through this handle, so I needed to drill a really deep hole. To keep it centered, I used the top and bottom pieces to hold the dowel parallel to the bit, as well as act as guides for the bit. I drilled as far down as possible using the drill press and then finished the middle section with a hand drill and longer bit.
Step 4: Integrated Clamp
The PVC spout slides up and down for loading of the bottle, so I needed a clamping mechanism to keep everything tight when in use. This was achieved by using 1/4' threaded rod, a nut, and scrap of dowel.
On one side, I drilled a 3/8" hole to recess the nut, and then through drilled with a 1/4" bit. Since my bit wasn't long enough and I wanted to avoid blow out, I finished the 1/4" hole from the other side.
Step 5: Threaded Handle
I make quick and easy scrap wood handles all the time (my awls, drill press fence clamp handles, router lift handle) and this is how.
Find the center of the stock, drill a hole for the threaded rod, glue on the handle with epoxy. Since I had the epoxy out, I glued in the recessed nut and a washer to the clamping side opposite of the nut.
Once the epoxy cured, I used the stock to determine the threaded rod length, cut it with the angle grinder, and cleaned up the threaded end with the bench grinder. A good tip is to thread 1 or 2 nuts onto the rod before you cut and grind it .. that way you can use them to fix any deformed threads by threading them off. I, of course, always get ahead of myself and forget .. learn from my mistakes. You can also see I made a center cut using the bandsaw, which allows the board to actually clamp together.
I also did some quick shaping of the handle on the oscillating belt sander.
Step 6: Pivot Rod
I originally thought I'd just cover the top of the tube with my thumb ... like you would a drinking straw to keep fluid from exiting. This quickly proved to be a true test of dexterity and wasn't going to work. My solution was to make some kind of valve like you would see on a Saxophone.
I needed a pivot point and chose to use a 3/8" dowel cut off. I arbitrarily put mine 1 3/4" down from the top piece of poplar and drilled a 3/8" hole into the dowel handle. I could only drill so deep because I didn't want to blow through and into the hole I created for the sprinkler tubing.
Once that was done, I glued the main assembly together.
Step 7: Valve Fabrication
For the valve, I used a 1" dowel cutoff and self adhesive neoprene. For the valve handle, I used 3/4" poplar cutoffs and left everything long during fabrication because I was designing on the fly. These cutoffs are 3/8" thick.
I started by making the 90 degree joint and I went with a dado because I figured that be the best method for keeping these parts square, as well as adding more gluing surface than a rabbet or butt joint. I made this cut using a table saw sled and just snuck up on it until I had a snug fit.
I eyeballed the location of the hole for the pivot rod and drilled out an oval space using a forstner bit on the drill press. With the valve handle laying parallel to the dowel handle, I laid out and drilled for the pivot pin, which is just a small brad.
With the pin in place, I could then set the valve in its place, add some epoxy and then rotate the handle on it's axis until they met. This way I avoid all calculation and get a perfect alignment.
Once the epoxy cured, I trimmed off the extra length and shaped the valve handle on the oscillating belt sander.
Step 8: Valve Assembly
I needed something to keep the valve closed, therefore creating a tight air seal. I salvaged parts from a broken printer a few months back and included were some small springs, which will be perfect. I used small stainless steel wood screws because I had them and I liked them.
I first drilled a hole in the center of the dowel handle for one end of the spring and screwed that in place. Next I found the location for the spring on the valve handle and pre drilled that on the drill press.
Step 9: Sanding and Oiling
With fabrication complete, it was time for some quick sanding and an application of boiled linseed oil.
Step 10: Air Tube and Final Assembly
With beer can shotguns, the godly nectar exits the bottom hole (made by a screwdriver in my past experience) as air enters through the top. The pop top on a can makes this simple, but we can't do that with a bottle. I snaked the air into the bottle via sprinkler tubing.
First, I threaded the tubing through the hole I made within the dowel handle. I used a bit of superglue to secure the hose at the top. Next, I threaded the tubing through the hole in the PVC fitting and left enough slack to reach the bottom of the bottle. Lastly, I cut the tubing flush at the top so that the valve made a tight seal. The pivot pin (brad nail) also got a dab of of superglue on each side to keep it from working itself out over time.
Step 11: Glamour Shots
Here are some pictures of the finished device from all sides, as well as some close up pictures of the valve assembly.
Step 12: Directions for Use
"So how does it work?," you might be asking.
1. With the fixture upside down, raise the spout [Fig. 1].
2. Insert the bottle, ensuring the tubing is inside and at the bottom of the bottle [Fig. 2].
3. Lower the spout onto the bottle and tighten the clamp to hold it in place [Fig. 3].
4. Rotate the fixture into it's upright position [Fig. 4]. [Unless you want to get wet, have your mouth on the spout]
5. Open the valve [Fig. 5].
6. Fly a finger to your bad day AND stay on the Warden's schedule. [This step is optional]
Important Note: This instructable is for entertainment and workshop fun purposes. I do not condone excessive and/or irresponsible drinking of any kind.
Another Note: I tested this with water and it was ridiculously fast.
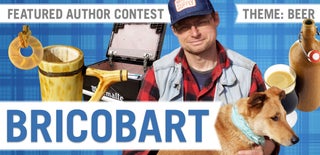
Participated in the
Featured Author Contest: bricobart
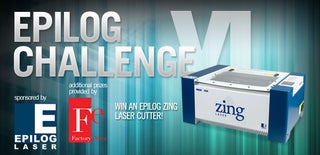
Participated in the
Epilog Challenge VI
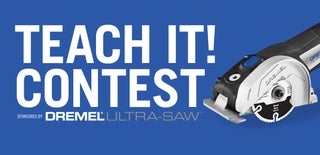
Participated in the
Teach It! Contest Sponsored by Dremel