Introduction: Pallet Coffee Table
"I'm going to buy a new coffee table at IKE ..." was all I heard. My bag of bones was in the shop before that last syllable could soar through the air and offend my cochlea. I can't actually confirm, but I'm 97.6% positive that my departure caused the area rug to bunch up like the pavement in an old Looney Tune. A ribbon of carnage similar to that left by a curious cat whom has just discovered the toilet paper roll.
The Warden, as it turns out, was NOT a fan of my current (now previous) coffee table. She was however, receptive to the idea of a pallet wood table. My disdain for the store which shall not be named was enough motivation initiate Operation Make A Table.
A little history on the predecessor:
In 2002, I was working as an Assistant Superintendent at a nightclub in Boston. While cleaning out some storage, I uncovered some 3/4" plywood and bar top epoxy. Two 40" x 20" pieces of plywood were laminated together and holes were drilled halfway through on the underside, which aligned with the posts/legs on these commercially available, modular, wire shelving units. The plywood top and sides was coated with joint compound to achieve an interesting depth and texture. Once dry, the joint compound was painted black and once the paint was dry, the bar top epoxy was poured.
This wasn't my original idea. The bar tops in the club were made using this method, except they were painted gold. It's a cool visual effect, but a horrible solution for a bar. As you can see from the corners of the tabletop, the finish chips and breaks off. Add moisture from drinks, spills, cleanup and you end up with major failures - the joint compound gets saturated and peels up in large sheets. Even worse is that it is a breeding ground for mold and mildew.
Step 1: The Decimation
First task was to tear off the old finish, which was way too easy. A few taps with a hammer along the sides cracked the epoxy and created an entry point for a putty knife. Most of the joint compound flaked off, but a belt sander made quick work of any stubborn bits.
Step 2: Processing Pallet Slats
I had a stack of pallet slats left over from when I built a trash can corral, but it was all in rough form and I wanted a more polished look for this table. Thicknesses also varied, so I needed to mill them down to a common dimension. Any boards with cupping, twist, or cracks, were sacrificed to the burn pile. Yes, I'm a savage ... I also have no desire to struggle with pallet wood for hours.
Cleaning up the boards wasn't difficult ... it just took time.
1. Joint one edge of each board using the jointer.
2. Use the jointed edge as a reference to cut the opposite edge parallel using the table saw.
Note: I kept each board as wide as possible, but you could cut them to a common width if desired.
3. Run all of the boards through the planer and repeat until they are a common thickness.
4. Run all of the boards through the drum sander to remove any tooling marks and further finesse the standardized thickness. You could skip this step, but I have the machine and it's fun to use.
Note: If you prefer the rough/used look, just plane one face. I chose to plane and sand both faces.
Step 3: Design and Attaching Slats
I knew I wanted somewhat of a random pattern, as opposed to a herringbone or chevron layout, but I didn't have a clear picture in my mind. I decided to just lay down boards in different configurations until something caught my eye. Once I decided on a pattern, I shuffled around different board widths and coloring.
With the layout determined, I spread glue onto the plywood and secured the pallet slats with pin nails. I also took the time to apply glue to the edges of each board and just cleaned up the squeeze out as I went. Board ends were cut square using my small parts cross cut sled as necessary.
I let all the boards run long, so I could cut them all in one fell swoop - same idea used when building decks. I had a few boards which didn't want to lay flat, nor stay tight to their neighbor, so I used a few clamps and wooden cauls.
Tip: Apply packing tape to your wooden calls to avoid gluing them to your work piece.
Step 4: Cutting the Top to Size
Trimming the slats flush with the plywood substrate would've been the quicker and easier method. I would do that by removing the bulk with a circular saw or jigsaw and then using a router with a pattern bit to cut them flush. One concern with that method would be blow out since my design resulted in all four sides being end grain.
My brain however, wanted to do it the more difficult way, which should come as no surprise to those who have seen other projects of mine. I wanted the pallet boards to overhang the plywood and then sit within a rabbet, which would be cut into the side edging. I figured this would add more glue surface and interlocking support. Thanks brain ... you're awesome!
3/8" seemed as good a measurement as any, so I cut myself spacer strip and taped it against the plywood edge. I then aligned my saw track with the edge of the spacer. A scrap of laminated plywood used as a fence makes this very easy. Once the track was clamped in place, I removed the spacer, made the cut, and repeated the process on the other three sides.
Step 5: Fabricating the Sides
For the sides of the table, I decided to use poplar. It's not as hard as Maple and might take some dents/dings, but I had it on hand and it's affordable.
I ripped the boards into 3" widths and then cut the lengths longer than necessary - two at 42" and two at 22". Rabbets were then cut into what I determined to be the top edge of each board. I used a test piece to dial in the perfect blade height (approx 3/8") and fence offset (approx 3/4") to minimize errors. The 3/4" offset is an over cut and will sit higher than the pallet top, but I'd rather have the ability to sand the surplus flush than end up lower than the pallet top.
I used my 45 degree small parts cross cut sled to cut all the miters using the table saw. Instead of fussing with the fence and a stop block, I just snuck up on the cuts until I was happy with the fit.
Step 6: Attaching the Sides
Glue on the miter joints would suffice since I'll be adding miter splines, but I figured dominos would help with alignment and keep the corners from sliding around during assembly. Also, it's a fun tool and I like to use it.
Initially, I was going to attach the sides one at a time, but decided against that tactic because if I didn't get the first board perfect, it could compound errors and create gaps. Instead, I chose to assemble the sides as a large frame, apply some glue to the rabbets, and then drop the tabletop into the frame. This worked perfectly, but I should've let the frame dry overnight before dropping in the top. The glue had set up a bit, but the miters shifted due to leverage and weight and I couldn't get them 100% closed again. Another lesson in patience.
Step 7: Concealing Mistakes
Problems lead to solutions and I addressed the self imposed miter gaps with the proven method of wood glue and sawdust. Just force some glue into the gap and then pack it with sawdust. Once it dries, you can sand it flush and it's barely noticeable. I had a few minuscule gaps around the top edge, which I also filled at this time.
Since I had to wait for glue to dry, I decided to paint the underside with some left over satin black paint.
Step 8: Miter Splines
Time for miter splines - both for strength, as well as visual interest.
My shop built sled is modeled after the Eagle America design. I wouldn't say it's really designed for a large tabletop, but ... I used it for a large tabletop. I balanced the weight, had a stop in the miter track so the sled couldn't advance past the blade and off the table, had the sled stop blocks tight against each side of the table, full PPE, etc. The operation was smooth and without incident.
Note: I cut a notch at each corner, top and bottom - eight in total. Then I adjusted the sled stops and cut them all again so I ended up with 1/4" wide notches.
I chose to make the splines out of some padauk scrap, which believe it or not, also came from a pallet [I included a picture of the find so you could share in my awe].
I resawed a section using the table saw and then reduced the thickness using the drum sander until I had a perfect fit for the notches. Further ripping and cutting was done using the table saw and bandsaw to end up with 8 splines.
I slathered the notches and splines with glue, pressed them into place, and left them to dry overnight. Once cured, the excess spline material was cut off using an oscillating multi-tool and then sanded flush using an orbital sander.
Step 9: Sanding
My initial plan was to use the drum sander to level the sides with the top and then finish up with the orbital sander, but it wasn't meant to be. It turns out that 3" is barely too tall for the drum sander. I tried, but it was too big of a bite and the machine was struggling. Also, because the sides extend past the plywood bottom, support was an issue - instead of laying flat on the feed belt and infeed/outfeed tables, it rocked, which isn't ideal.
Plan B was to level the sides with the top using the belt sander, which worked just as well, but took more time. I just kept the sander moving and regularly checked flatness using a 4 foot level. Once I was satisfied with my planar progress, I switched to the orbital sander in order to smooth out the finish - 100, 150, 220, and then 320 grit.
Step 10: Finishing
I wanted to bring out the depth of grain and color of disparate pallet wood species, but I didn't want the yellow hue which I get when I use the 50/50 boiled linseed oil/mineral spirits blend. I decided to go with clear shellac followed by water-based spar urethane for durability.
Usually, one would thin shellac with denatured alcohol, but I didn't have any and to be honest, I was curious whether or not mineral spirits would do the job. I've heard tales of this combination creating a gooey mess ... not blending and therefore penetrating the wood unevenly ... totally ruining your project, etc. It worked just fine - no catastrophic failures of any kind. It's possible that the human eye might pick up faults in a solid top, but my eyes don't see any issues and I only wear a very low prescription lens for night driving.
Once the shellac was dry, I finished the table with five coats of spar urethane with light sanding at 200 in between. I don't really like this product. It goes on milky, a bit thick, and I could never get rid of all of the brush strokes. I tried thinning later coats in hopes of it self leveling a bit, but no luck. I even tried an ultra thin mix and a wiping technique ... still no luck. I prefer the results of oil-based poly, but don't like the smell, not the yellow hue which develops over time.
Step 11: Glamour Shots
Out with the old and in with the new - proof that pallets can be incorporated in a non rustic design ... not that anyone was denying that fact.
Overall, I'm pleased with the end result. I like mix of color between the different boards, the lighter band provided by the poplar sides, and of course the padauk splines. In hindsight, I'd build it at 2 3/4" thick so it would fit through the drum sander and try a different topcoat product.
The Warden likes the tabletop, but says the wire shelving base has to go - now she tells me. Looks like the next challenge is coming up with a base design, building it, and figuring out a method of attachment ... but that's a problem for another day.
Full disclosure: The Warden says she did tell me ... several times ... but I have selective hearing. "New table" .. not just new tabletop.
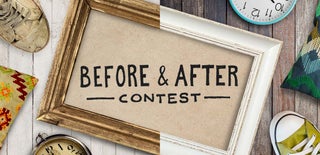
First Prize in the
Before and After Contest 2017