Introduction: Tormek ST-250 Supergrind Whetstone Grinder Sharpener AMC77 Update & Upgrade Project
I picked up an early drill powered Tormek ST-250 for just £5.00! (1 pictured above is not mine but it's the same model)
Mine is missing the water trough, tool rest and optional honing wheel but that's no big deal.
I initially intended to sell it but having recently taken up woodturning I thought better of it! So I set about updating/upgrading it.
Step 1: Electric Motor
First thing was to find a small high torque motor.
This is what I found on ebay, a 200w DC treadmill/vibration plate motor with speed controller/AC-DC converter and mains lead sold as a kit by hebdenmotorbits
I had to swap the red/black motor wires around to change the direction of rotation and remove the pulley.
Step 2: Fitting the Motor
I managed to use the existing drill drive support with some simple modifications inc shortening and re-drilling the pivot hangers and cutting off the drill clamp arm.
Step 3: Water Deflector
I made a plastic splash guard out of an old screenwash bottle to cover the back of the motor nearest the water trough.
Step 4: Speed Controller/switch
I fitted the control board into a plastic project box and wired everything up making sure it's well earthed and that nothing can catch the wires.
Step 5: Switch
Next I drilled the case for the mains flex and speed control knob.
Step 6: Re-fit the Wheels
Time to fit the drive wheel and stone,
Underside view of how it all fits.
Step 7: Water Tank
Found a makeshift water trough, an Arial washing pod tub!
Step 8: Honing Wheel
For the honing wheel I used 12mm plywood and cut out 4 disks approx 230mm dia and glued them together.
Step 9: Honing Wheel
I then drilled the centre big enough for the M12 nut and drilled & bolted a large steel washer in place.
Step 10: Honing Wheel
Next I true everything up in my wood lathe and hollowed out the centre like making a bowl.
Step 11: Leather Wheel
I found an old leather belt and used contact adhesive to glue it to the plywood, I cut the joint at 45° rather than trying to skive and overlap the leather to keep it as flat/uniform as possible.
Step 12: Dry Run.
Time to try it!
Step 13: Dry Run
Everything runs true, with the leather fitted the honing wheel measures exactly 220mm dia.
Step 14: Speed Test
Measuring the RPM with a laser tachometer so I can mark the speeds on the dial
Step 15: Water Trough Upgrade
I found an old paint scuttle I adapted to fit the original water trough hangers. I may get a genuine one later? but this will do for now.
Step 16: Rest & Jigs
I bought a horizontal tool rest base and some second hand jigs inc a short tool jig, square edge jig and the gouge jig pictured.
Step 17: Errors!
Mistakes were made!
I realised the switch being on top of the machine wasn't such a good idea! There's a strong chance of water splashing from the stone and pooling on top of the case, not very safe!
Switch now moved under the motor and away from any water splashes.
Step 18: Final Steps
I used leather conditioner on the honing wheel followed by Autosol metal polish as a honing compound.
All I need to do now is to make a shelf for it in my workshop. The leftover plywood from the honing wheel will be just the thing!
Step 19: Now I've Got an Axe to Grind!
Seriously my axe needs sharpening.
Having been ground and honed it's now sharp enough to shave with!
Step 20: New Trough
I found a cheap genuine AWT-250 water trough someone bought in error!?
I wasn't 100% sure it would fit my early machine, but it was cheap enough to risk it! I can confirm it fits the ST-250 perfectly.
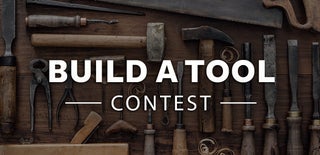
Participated in the
Build a Tool Contest