Introduction: 3D Printed Leather Mold
For this project, I created 3D Printed tools to make a custom leather mold.
Step 1: Design and Print the Mold
I wanted to make a pair of earrings whose core would be solid but the outer side would be made of leather. So I started designing a mold on Tinkercad that consists of a core and a cavity in the shape of a dome. The tricky part in this process was that leatherworking it’s an old craft with lots of tradition and terminology, so it can also be confusing for amateurs like me. When buying leather, you want to make sure you know what you’re paying for. This often means wading through marketing and learning some of the common terminologies when it comes to different types of leather.
I ended up choosing lamb leather for the following reasons:
- Softness, cow leather has a relatively rougher feel.
- Thickness, cow leather is thicker.
- Stretchability, cow leather is more rugged
Step 2: Leather Pressing
In this step, I just cut a piece of leather, I applied leather glue to the 3d printed core and with the help of a clamp I pressed them all together leaving it like that until the glue is dry.
Step 3: Trimming
Τhe process leaves leather that must be trimmed. Using a blade, I was able to trim through the leather in a single pass. Depending on the thickness and hardness of the leather, you may need to score the leather with a pass or two before fully trimming off the excess material.
Step 4: Summary
Some argue that the 3D Printed objects often feeling cheap or flimsy, but using them as tools can lead to creative solutions with a variety of materials. With the flexibility of digital design and fabrication with materials like leather, we can create objects useful in every day life and personalized to our needs.
Step 5:
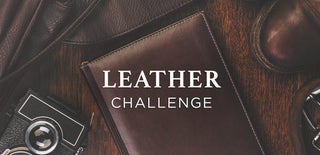
Participated in the
Leather Challenge