Introduction: Carved, Casted and Plated Heart Shaped Necklace
Carved, Casted and Plated Heart Shaped Necklace
In this Instructable, I will be going over how I created this casted silver, rhodium plated necklace for my girlfriend’s birthday. To create this necklace, I used the traditional method of Lost Wax Casting. This meant; carving the piece out of wax, casting the wax piece, filing, sanding & polishing the casting and then rhodium plating it to prevent tarnish.
Like most of my projects, I gave myself a very short time frame. I completed the whole project in about two weeks from start to finish for around $70. I bought all of my supplies at a wholesale price. This is my first "legitimate" piece of jewelry. I have made some things out of wood before this one. Most of the skills I used to create this piece were obtained from watching my mom who was a jeweler for 30+ years.
Necessary Supplies:
-block of carving wax (I used purple which is right in the middle of brittle and soft)
-a chain of choice
-jewelry caster of choice
-jewelry polisher/plater of choice
Necessary Tools:
-range of files for wax and silver
-range of dental tools and gravers for carving wax
-Precision Waxer (a heated wax tool, very useful for fixing mistakes)
-sanding tools
-flex shaft system (cutting, carving and polishing attachments)
In this Instructable, I will be going over how I created this casted silver, rhodium plated necklace for my girlfriend’s birthday. To create this necklace, I used the traditional method of Lost Wax Casting. This meant; carving the piece out of wax, casting the wax piece, filing, sanding & polishing the casting and then rhodium plating it to prevent tarnish.
Like most of my projects, I gave myself a very short time frame. I completed the whole project in about two weeks from start to finish for around $70. I bought all of my supplies at a wholesale price. This is my first "legitimate" piece of jewelry. I have made some things out of wood before this one. Most of the skills I used to create this piece were obtained from watching my mom who was a jeweler for 30+ years.
Necessary Supplies:
-block of carving wax (I used purple which is right in the middle of brittle and soft)
-a chain of choice
-jewelry caster of choice
-jewelry polisher/plater of choice
Necessary Tools:
-range of files for wax and silver
-range of dental tools and gravers for carving wax
-Precision Waxer (a heated wax tool, very useful for fixing mistakes)
-sanding tools
-flex shaft system (cutting, carving and polishing attachments)
Step 1: The Design
The Design
First thing’s first, we need a design. I sketched out my piece on a piece of paper multiple times after browsing the web for countless different heart shapes. Once I was pleased with my design, I etched it into the surface of the carving wax.
First thing’s first, we need a design. I sketched out my piece on a piece of paper multiple times after browsing the web for countless different heart shapes. Once I was pleased with my design, I etched it into the surface of the carving wax.
Step 2: Cutting the Piece
Cutting the Piece
Ok, so once the design is etched onto the surface of the block of wax, time to cut it out. This is a rough cut, I recommend using a block of wax much larger than needed if you're new at this. It allows for plenty of room for error and practicing with the tool. To cut the piece out, I used a jeweler’s hand saw, with a heavy wax spiral blade. I then worked my way around the shape with a rough cut ½ round file to get started. I then filed the curve of the edges to make the shape outlines clean and follow along my design.
Ok, so once the design is etched onto the surface of the block of wax, time to cut it out. This is a rough cut, I recommend using a block of wax much larger than needed if you're new at this. It allows for plenty of room for error and practicing with the tool. To cut the piece out, I used a jeweler’s hand saw, with a heavy wax spiral blade. I then worked my way around the shape with a rough cut ½ round file to get started. I then filed the curve of the edges to make the shape outlines clean and follow along my design.
Step 3: Drilling Out the Center
Drilling out the Center
I designed my heart to have an open middle. I wanted to remove the middle of the piece early in the shaping process in order to ensure I wouldn’t shape the outer edges too small. To remove the center, I first used a drill bit and the flex shaft. I evenly removed the middle all around with a round burr, making a hole large enough to fit my files into. This hole is much smaller than it will be once it’s finished. I prefer to have plenty of working room.
I designed my heart to have an open middle. I wanted to remove the middle of the piece early in the shaping process in order to ensure I wouldn’t shape the outer edges too small. To remove the center, I first used a drill bit and the flex shaft. I evenly removed the middle all around with a round burr, making a hole large enough to fit my files into. This hole is much smaller than it will be once it’s finished. I prefer to have plenty of working room.
Step 4: Shaping
Shaping
Now using a range of files and graver blades, I worked my way around the heart shaping it to the desired size and curvature. I worked the inside and outside together in order to keep the heart from getting to thin in certain places. I wanted to have the chain run through the heart, so I kept one of the corners pretty big and bulky to drill a hole.
When working with the model, if you accidentally remove too much material there is a why to add wax back. It is a bit tricky and there a few things to keep in mind. You would have to use a Precision Waxer, to me this was like a soldering iron for wax. If you dump the waxer in your wax shavings, you can heat your model and apply the wax to it. By rubbing the wax shavings onto the model you can add material back, then file it smooth. It is very important to heat your model up so that the material is melted on, not just sitting on the surface. If there are any bubbles, the wax will not stick through casting and the piece will break.
Now using a range of files and graver blades, I worked my way around the heart shaping it to the desired size and curvature. I worked the inside and outside together in order to keep the heart from getting to thin in certain places. I wanted to have the chain run through the heart, so I kept one of the corners pretty big and bulky to drill a hole.
When working with the model, if you accidentally remove too much material there is a why to add wax back. It is a bit tricky and there a few things to keep in mind. You would have to use a Precision Waxer, to me this was like a soldering iron for wax. If you dump the waxer in your wax shavings, you can heat your model and apply the wax to it. By rubbing the wax shavings onto the model you can add material back, then file it smooth. It is very important to heat your model up so that the material is melted on, not just sitting on the surface. If there are any bubbles, the wax will not stick through casting and the piece will break.
Step 5: Hollowing the Piece
Hollowing the Piece
When the piece is casted, it will gain a large amount of weight. If the piece is too heavy, it will be awkward, uncomfortable and even dangerous. To save weight, I drilled out the back of the piece and hollowed it pretty thin. Thin enough for light to pass through. I then with a round bur in my flex shaft uniformly made round divots, much like a honeycomb appearance to save weight. Casting wax to silver will add roughly13 times the wax weight, so my desired finished weight for the wax was .4 grams. This is a delicate step that could easily break the piece. Proceed with caution.
*If doing a hidden bail like I did, you will want to do that before your piece is totally hollowed out, or it will be too fragile. Start maybe half-way, fitting the chain & hollowing.
When the piece is casted, it will gain a large amount of weight. If the piece is too heavy, it will be awkward, uncomfortable and even dangerous. To save weight, I drilled out the back of the piece and hollowed it pretty thin. Thin enough for light to pass through. I then with a round bur in my flex shaft uniformly made round divots, much like a honeycomb appearance to save weight. Casting wax to silver will add roughly13 times the wax weight, so my desired finished weight for the wax was .4 grams. This is a delicate step that could easily break the piece. Proceed with caution.
*If doing a hidden bail like I did, you will want to do that before your piece is totally hollowed out, or it will be too fragile. Start maybe half-way, fitting the chain & hollowing.
Step 6: Choosing the Chain
Choosing the Chain
It really took me a very long time to choose the chain. I sketched a lot and searched through catalogs for hours. I ended up choosing a Round Wheat style chain. It was important for me to choose a chain prior to creating the hole for it so I could ensure it would fit properly. The chain I chose was not plated because I planned to rhodium plate the piece and chain together to keep them complimentary.
It really took me a very long time to choose the chain. I sketched a lot and searched through catalogs for hours. I ended up choosing a Round Wheat style chain. It was important for me to choose a chain prior to creating the hole for it so I could ensure it would fit properly. The chain I chose was not plated because I planned to rhodium plate the piece and chain together to keep them complimentary.
Step 7: Chain’s Hidden Bail
Chain’s Hidden Bail
To drill the hole for the chain, I first had to decide at what angle I wanted the heart to hang. I marked with a scribe 2 spots to drill 2 holes, figuring these spots from the basic curve of a chain. You will want to drill small holes at first, leaving you room to adjust the angle it hangs on. I used a small round burr in my flex shaft to then open up the holes to desired size and shape for the chain. You can use a small piece of cord as a test chain while working on a piece; it’s very handy since you’ll be testing it many times.
To drill the hole for the chain, I first had to decide at what angle I wanted the heart to hang. I marked with a scribe 2 spots to drill 2 holes, figuring these spots from the basic curve of a chain. You will want to drill small holes at first, leaving you room to adjust the angle it hangs on. I used a small round burr in my flex shaft to then open up the holes to desired size and shape for the chain. You can use a small piece of cord as a test chain while working on a piece; it’s very handy since you’ll be testing it many times.
Step 8: Casting and Cleaning
Casting and Cleaning
I did not personally cast this piece. I had a professional metal caster, cast it for me in silver. After receiving the piece back, it needed to be cleaned up desperately. Any imperfections in my wax were escalated and easily noticeable. There was also the sprue (where they connect a stem for casting) on the side of it that needed to be removed. In order to do all this, I worked on the piece with a series of files until it was perfectly smooth all around. I then went to fine emery paper (a jeweler’s sand paper.) I have this on a spindle in the flex shaft, as well as mounted on an emery stick. With the emery paper you get out all the fine lines the file leaves, smoothing out the piece. This is the last stage of shaping, so the shapes and curves and surface of the piece are final at this point. Work it until perfection.
I did not personally cast this piece. I had a professional metal caster, cast it for me in silver. After receiving the piece back, it needed to be cleaned up desperately. Any imperfections in my wax were escalated and easily noticeable. There was also the sprue (where they connect a stem for casting) on the side of it that needed to be removed. In order to do all this, I worked on the piece with a series of files until it was perfectly smooth all around. I then went to fine emery paper (a jeweler’s sand paper.) I have this on a spindle in the flex shaft, as well as mounted on an emery stick. With the emery paper you get out all the fine lines the file leaves, smoothing out the piece. This is the last stage of shaping, so the shapes and curves and surface of the piece are final at this point. Work it until perfection.
Step 9: Plating and Polishing
Plating and Polishing
First is polishing. Since I was having the piece rhodium plated, I took it to a professional polisher/plater. They polished, cleaned and rhodium plated the heart pendant and chain. Rhodium plating prevents any tarnishing and evens out any color differences between the silver of the chain and the pendant. After the plating process was complete, the necklace was a shiny finished piece and ready to be given.
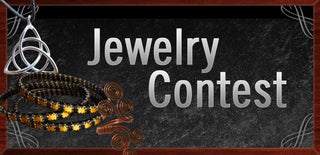
Participated in the
Jewelry Contest