Introduction: How to Make a Ring With a Wood Inlay
In this tutorial I will show my process for creating a metal ring with a wooden inlay. For this project I used a steel ring liner from http://www.bangleguy.com/ and a red buck eye burl knife scale from http://www.bangleguy.com/
This is a simple wood turning project that won't require a huge amount of tooling or time and a great way to spend an afternoon in the workshop! Wooden rings make very unique engagement or wedding bands as well as cool accessories for everyday wear.
Feel free to watch the video or skip through the steps to read this tutorial. If you like it then come and subscribe to my Youtube channel for more wood turning projects!
Step 1: First Things First - Measuring
I measured the outside diameter and width of the ring blank with a caliper so I could use my powers of deduction to work out how much wood I'd need to use.
The diameter required was around 21mm and the width of the inlay was 7mm.
The ring blank came from www.bangleguy.com and was made with stainless steel. They make a variety of different sizes and each ring blank comes in two parts that slot together.
I had an off-cut from a knife scale which was definitely big enough for the project and also had a distinctive grain pattern. The knife scale was a stabilised and dyed buck eye burl that I'd been saving for a rainy day.
I quickly drew a line from corner to corner on the off-cut to find the center and moved over to the drill press.
Step 2: Preparing the Wood for Turning
With my measurements done I mounted my wood on the drill press and bored a hole with a 20mm paddle bit. To prevent blow out as I drilled I placed a thin sheet of ply wood under the buck eye burl, and this worked a treat.
I drilled the hole slightly smaller than required but sanded it until the metal ring blank fit nice and snug inside. I did this using a piece of sand paper wrapped around a wooden dowel.
Next I cut a rough shape out of the wooden blank on the scroll saw – just the take the edges off and make it easier to turn.
Step 3: Mounting on the Lathe, Turning & Parting
I needed a way to mount the wood on the lathe for turning so I made a quick jam chuck from a piece of pine dowel. This was pretty simple: I just used a skew chisel to turn a small section at the end of the dowel down to the exact diameter as the inside of the hole in the wood. A digital caliper, trial and error really helped here!
The jam chuck was a pretty good fit but I also held the wood in place with a wine cork from the tailstock. This method of mounting worked nicely and I got to work with a roughing gouge to make a ring shape.
After the initial shaping I once again using a caliper to mark just over 7mm so I could see where the ring needed parting.
I was going to use a parting tool but the thin wood looked pretty fragile so I used my drill press clamp and a fine toothed saw to cut the ring to size.
Step 4: Assembling the Ring
With the rough wooden ring made I did a bit of fine tuning with sand paper to ensure the metal ring blank was a perfect fit.
After a few test runs of assembling the ring I was ready to glue up. I carefully applied a high viscosity super glue to the metal ring blank, inserting one section at a time into the wood.
Both pieces of the steel ring slot together nicely and assembly was pretty easy if you work fast!
Time for a quick coffee and to mount this bad boy back on the lathe for shaping and finishing.
Step 5: Final Turning & Finishing
I made a an adjustment to the jam chuck and used chisels to shape the wooden ring.
After shaping I sanded through a few grits to get a nice smooth feel to the ring.
For finishing I wanted to enhance the colours of the grain and decided against a thick membrane finish like CA glue so I could actually feel the texture and smoothness of the wood against my skin.
I just used a few layers of friction polish on this piece to keep it simple and preserve the feel of the grain.
Finally I scraped away any excess super glue with a craft knife. The end result was a beautiful, tactile ring that I'll be wearing for years to come!
Step 6: Thank You for Watching!
Thank you for watching as always, if you liked this video then help by hitting the like button or even sharing it on social media!
You can find many great turning project kits over at www.bangleguy.com and amazing materials from my fellow craftsmen over at www.emberleaf.com (they make kick ass knives too!).
Did you like this tutorial? I am working on more cool project videos and have a few published on my Youtube channel if you want to see more!
My name is Dan Rees from Zebrano Wood Craft and I look forward to making sawdust again with you soon!
Subscribe to my YouTube channel to see more wood turning projects!
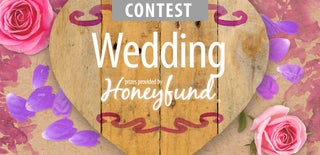
First Prize in the
Wedding Contest 2016