Introduction: Laser Cut Jewelry: Layered Acrylic Rings
I’ve been making gifts for as long as remember. And, although I know people do not want to impose any obligation, the pressure of tradition is there, and sometimes when a gift occasion is coming up, lack of time is a problem. I’ve often said I should first build a time machine to solve this.
Well, lately some devices have become available to the common maker that can play the role of a time machine to some extent: laser cutters, CNC milling and 3D-printing.
The layered acrylic rings presented here are an example on how I use this. While ordering parts laser cut from acrylic sheet of different colours, I added ring sections to the design files. These "prefab" ring parts save a lot of time.
Gluing, sanding and polishing still involves some handwork, so the handmade gift statement is intact ;-)
With the parts cut to the right size it takes only about 20 minutes to make one finished ring (without power tools). And it doesn’t make much of a mess if you work in a basin or something like that.
Obviously the colour combination is chosen to fit the taste of the intended recipient. I find the best effect is reached with transparent colours (here the amber, brown and violet) and translucent colours (like the red here). But opaque colours (white, black) give nice results too. The pictures in the following steps are from the making of a black-and-red ring not shown in pictures above.
If you like this Ible, please give it your vote in the contests.
Well, lately some devices have become available to the common maker that can play the role of a time machine to some extent: laser cutters, CNC milling and 3D-printing.
The layered acrylic rings presented here are an example on how I use this. While ordering parts laser cut from acrylic sheet of different colours, I added ring sections to the design files. These "prefab" ring parts save a lot of time.
Gluing, sanding and polishing still involves some handwork, so the handmade gift statement is intact ;-)
With the parts cut to the right size it takes only about 20 minutes to make one finished ring (without power tools). And it doesn’t make much of a mess if you work in a basin or something like that.
Obviously the colour combination is chosen to fit the taste of the intended recipient. I find the best effect is reached with transparent colours (here the amber, brown and violet) and translucent colours (like the red here). But opaque colours (white, black) give nice results too. The pictures in the following steps are from the making of a black-and-red ring not shown in pictures above.
If you like this Ible, please give it your vote in the contests.
Step 1: Materials
You will need:
Three ring sections laser cut from 3mm thick acrylic sheet of the desired colours (see the next step for the design and sizing). I usually order from Formulor, the German Ponoko partner;
Glue for acrylic parts. I used Acryfix 1R 0192 from Evonik. It gives a good strong bond. Work in well ventilated conditions;
Waterproof sanding paper grit 320 and 1000 (800 probably works too);
Polishing compound for plastics or paint (I used a “renovating” compound for tarnished car paint, which combines a wax with some very fine polishing grit);
A soft cloth or a polishing wheel;
Some non-stick (baking) paper.
Use a plastic basin to work in with the wet sanding paper and the polishing compound.
A calliper comes in handy to take the correct size of an existing ring.
Step 2: Determining the Ring Size
Having the ring sections cut to the right size is crucial to save work. A ring cut to small can be made larger, but it takes care and time.
It’s best to take the size from an existing ring that fits comfortable. The diameter of the inner circle in the laser cutting design is taken equal to the measured size. As the laser cut 0.2 mm wide this means the inner diameter will be 0.2 x ½ x 2 = 0.2 mm wider. As the ring has a wider rim than most rings, I found this is actually good to give a more comfortable fit. Below you find a design for rings with a reference inner diameter of 16.4 mm (my wife’s ring finger size), so giving an laser cut inner diameter of 16.6 mm.
I put two sections next to each other to save cutting costs. I added three sections to designs for other project in different colours. This way I had a choice of colours to make rings from. As you can see I used the Ponoko template and design rules, which in this case simply means using only paths with a 0.1 mm stroke in blue. I make my laser cutting designs in Inkscape. It’s free, easy to learn and is available for most common platforms and as a portable app. I usually work on my designs on the train to and from work, turning travel time to making time :)
It’s best to take the size from an existing ring that fits comfortable. The diameter of the inner circle in the laser cutting design is taken equal to the measured size. As the laser cut 0.2 mm wide this means the inner diameter will be 0.2 x ½ x 2 = 0.2 mm wider. As the ring has a wider rim than most rings, I found this is actually good to give a more comfortable fit. Below you find a design for rings with a reference inner diameter of 16.4 mm (my wife’s ring finger size), so giving an laser cut inner diameter of 16.6 mm.
I put two sections next to each other to save cutting costs. I added three sections to designs for other project in different colours. This way I had a choice of colours to make rings from. As you can see I used the Ponoko template and design rules, which in this case simply means using only paths with a 0.1 mm stroke in blue. I make my laser cutting designs in Inkscape. It’s free, easy to learn and is available for most common platforms and as a portable app. I usually work on my designs on the train to and from work, turning travel time to making time :)
Step 3: Gluing
Peel the paper from the laser cut sheet to remove the parts. Remove the protective foil on both sides (If it didn’t come off with the paper).
Bring a good full layer of glue on the first section and put on the next section, squeezing out the excess glue. If any of the sections is transparent, make sure there are no air bubbles trapped in between (If so take apart and glue again, using more glue).
Do not let the glue set but continue immediately, repeating the gluing for the third section. With the three sections together, wipe off the excess glue and carefully align all three sections. I found this easiest with the flat face down on some non stick paper on the table. Don’t mind the glue traces all over the ring, these sand off of easily.
Let the glue set for at least a couple of hours.
Bring a good full layer of glue on the first section and put on the next section, squeezing out the excess glue. If any of the sections is transparent, make sure there are no air bubbles trapped in between (If so take apart and glue again, using more glue).
Do not let the glue set but continue immediately, repeating the gluing for the third section. With the three sections together, wipe off the excess glue and carefully align all three sections. I found this easiest with the flat face down on some non stick paper on the table. Don’t mind the glue traces all over the ring, these sand off of easily.
Let the glue set for at least a couple of hours.
Step 4: Sanding and Polishing
Start sanding with the 320 grit sandpaper, in a basin with some water. If the alignment didn’t work out so well, it can be worthwhile to start with a coarser grit and continue with the 320 grit afterwards.
Make sure all glue traces are removed, all surfaces (in and out) are flat and all edges (in and out) are rounded. If possible, test the fit before switching to a finer grit. Enlarging the inner diameter is possible with cylindrical sanding tool on a Dremel or power drill and/or coarser sanding paper. Do it in small steps not to overdo it en to keep the cylindrical shape.
Using 1000 grit sanding paper, sand all surfaces to remove the traces of the coarser sanding. Continu to work in water, but you will need to dry off the surface once in a while to see the difference.
Finally, with a polishing compound and a cloth (or polishing wheel) rub the surface to a shine.
The acrylic sheet sands and polishes quite easily and starting out with near finished laser cut parts, saves a lot of time. Once you get a feel how long to do each stage and you got the right size, one ring takes about 20 minutes. For a more information on how to polish plastics, check out this excellent Ible.
I hope you enjoy this Ible and the project's result.
Make sure all glue traces are removed, all surfaces (in and out) are flat and all edges (in and out) are rounded. If possible, test the fit before switching to a finer grit. Enlarging the inner diameter is possible with cylindrical sanding tool on a Dremel or power drill and/or coarser sanding paper. Do it in small steps not to overdo it en to keep the cylindrical shape.
Using 1000 grit sanding paper, sand all surfaces to remove the traces of the coarser sanding. Continu to work in water, but you will need to dry off the surface once in a while to see the difference.
Finally, with a polishing compound and a cloth (or polishing wheel) rub the surface to a shine.
The acrylic sheet sands and polishes quite easily and starting out with near finished laser cut parts, saves a lot of time. Once you get a feel how long to do each stage and you got the right size, one ring takes about 20 minutes. For a more information on how to polish plastics, check out this excellent Ible.
I hope you enjoy this Ible and the project's result.

Participated in the
Pocket Sized Contest
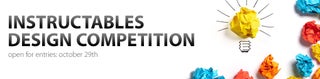
Participated in the
Instructables Design Competition
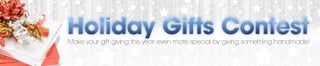
Participated in the
Holiday Gifts Contest