Introduction: Make a Ring From a Nut
In this Instructables learn how to make an awesome ring from a common steel nut. It takes a minimum of tools to make but power tools can be utilized to make the process faster. So to make this ring anyone can do it with some common tools (a round and flat file) and elbow grease.
If you like this Instructable vote for me in the Metal contest :)!
Step 1: Watch the Video
Check out the video to see how to make the ring from start to finish. The written steps follow.
Step 2: Tools and Materials
The tools used are:
- File: round and flat
- Dremel or Rotary Tool (optional)
- Wet/dry sandpaper
- Metal Polish
- Blow Torch (optional)
- Vice
For materials all you need is a steel nut, once could make it out of stainless steel but if this is your first ring stick with a mild steel nut. Find one that will be large enough for the finger that will eventually will be the ring's home.
Step 3: Anneal the Nut - Optional
Using a blow torch anneal the nut by heading it up to red hot and allowing it to cool in the air. This step is optional if you don't have a blow torch but it does make working with the metal easier.
Step 4: Enlarging the Ring Hole
There are a few options to enlarge the center of the nut to fit your finger. At the most basic level you can use a file or you can use a rotary tool with a grinding bit which will make things much faster and easier.
If you are using a round file start working away at the hole and don't work at one spot for too long or you may make the hole uneven. So put on some music and keep at it!
I started with a file but switched over to my rotary tools to speed things up. Test you finger occasionally, once the hole is starting to get close to fitting your finger you want to slow down and take your time as if you oversize the hole, there is no easy way to resize steel rings unlike precious metal rings that can be cut and soldered or resized on a mandrel.
It is better to leave the ring a bit tight fitting at this step as you can enlarge it later after the final shaping.
Step 5: Drawing the Outline
Once the ring is roughly sized to your finger, the next step is to draw an outline for the ring. I wanted to keep a flat side of the ring for the face but if you want to make a completely round ring you can draw what ever shape you want.
I ended up leaving the flat side of the ring to be wider than the rest of the ring and put a taper on the ring, see the pics, it's easier to see than explain.
I used a fine marker and ruler to drawn the outline and just eyeballed it but if you wanted to get precise you could measure each side.
Step 6: Cutting Out the Ring Outline
To cut the ring out of the outline that was drawn in the previous step you can do it two ways, option one is to use a flat file and just file at it. Or the second option is to use a hacksaw and cut away the excess material. It sounds like it will take a while but it really only takes a few minutes. Filing on the other hand will take you significantly longer but is totally feasible.
Step 7: Cleaning Up the Top and Bottom
After cutting out the ring from the outline, the top and bottom was flattened. This can be done with a flat file or in my case I used a belt sander. Here you can do some shaping as well to make the ring in to the profile that was drawn in earlier.
Step 8: Shaping the Ring
Once the ring has been flattened, the shaping can start. The points of the nut were filed down flat and then rounded. Most of this was done with a file but I did use the belt sander to do some of the stock removal. Again this can be completely done with a file. The front of the ring was left flat and the rest of the ring was rounded and smoothed. The inside of the ring and the edges of the ring were rounded as well to it would have a nice comfort fit and not catch on things.
Step 9: Wet Sanding and Polishing
Once you are happy with the shape of the ring, the final step is to wet sand and polish. Starting with some rough wet dry sandpaper and start sanding the ring, wet the sand paper this helps remove the sanded metal away. Do the flats of the ring first then move do the rounded sections. Be sure to sand the inside of the ring so there are no rough edges.
I like to start with 220 then move to 320, 400, 600, 800, 1000, 1500 grits. You don't need to spend too much time with each grit, you are just removing the sanding marks from the previous grits. Once you get to the 800 grit the ring should be very shiny, if it isn't re-sand with the previous grits.
Polishing the ring can be done by hand or with a rotary tool and buffing wheel. Use a good quality metal polish, you can find good ones for polishing car rims. Load the buffing wheel with some metal polish and buff the ring, including the inside of the ring. I polished the ring in a container to keep the polish from flying all over the place.
Step 10: The Finished Ring
The polishing will bring out a super luster to the steel. It is as shiny as a mirror.
The ring is finished! Re-polish when it starts to tarnish.
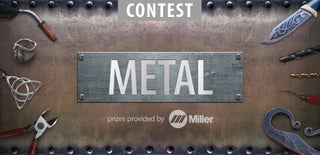
Participated in the
Metal Contest 2016