Introduction: Next Gen Home Automation Using Eagle Cad ( Part 1 - PCB)
Introduction:
- Why do i say its next generation: because it uses some components which are way better than traditionalhome automation devices.
- It can control appliances by:
- Google Voice Commands
- Touch Panel on the Device
- Control from app
- Control On and Off Along with speed of Fan
- Total Appliance:
- 2 On Off control devices
- 1 Dimming or Fan Speed Control
- How triac better than traditional relays
- No mechanical wear-out
- Easier to switch on zero-crossing. (Can also be done with a relay, but less accurate due to the switch-on delay)
- Can be used in dangerous environment, particularly in explosive sensitive environments where sparking relay contacts are absolutely out
- No EMI due to switching sparks/arcs
- No magnetic interaction with nearby inductors.
- Often more compact
- High frequency of switching
- It can control appliances by:
Step 1: Components Required
- Smps mini -5v
- MOC3041
- MOC3021
- Rectifier
- Triac-BT136
- Resistors
- Header Pins
- 4N35
- Touch Sensor
- D1 Mini Esp8266
Step 2: Choosing of Microcontroller
Which Micro controller to Choose:
We will be needing wifi control hence popular choices are either Raspberry Pi or Esp 8266.
As cost of raspberry pi is high, for this project i choosed Esp 8266. Now the question comes which variant of 8266?
- Esp-01
- Esp 12e
- NodeMCU
- D1 Mini
Now as i needed 10 controllable digital pins and size was an important factor i choosed D1 mini as it has sufficient no. of pins for my project and is small size.
Step 3: PCB Designing Using Eagle Cad (Part -1)
(Introduction):
- Open New Project, Name your project. Right click on it and select "New Schematic"
- Eagle Cad uses 2 files:
- Schematic file - For designing the circuit connections
- Board file- For final board design.
(Add Parts):
- Click "Add Part" as shown in the picture.
- Search each components and Press Ok.
- Place each components on the schematic.
Step 4: PCB Designing Using Eagle Cad (Part -2)
(Connect the components):
- According to the Circuit diagrams, each components should be wired accordingly.
- "Net Tool" is chosen and wires are made as shown in the picture.
Step 5: PCB Designing Using Eagle Cad (Part -3)
(Convert it to board file):
- Click "Generate to board" button on the left top as shown in the picture.
- Click "Create from schematic".
- Place the components as you wish to be on the final pcb.
Step 6: PCB Designing Using Eagle Cad (Part - 4)
(Connections in the board):
- Use "Routing" tool to make the trace connections between the components.
Step 7: PCB Designing Using Eagle Cad (Part - 5)
Generate Cam:
- PCB fabrication requires a lot of cam files.
- So by clicking on the "Generate Cam Data" button, the software will convert your project into files which can be read by CNC machines used for fabrication of pcb.
Step 8: Testing PCB by Home Made PCBs
As cost of pcb fabrication is high, i wanted to check if its correct or not i made 3 similar circuit before sending it for fabrication.
- First one was done on the bread board.
- Second one was done by soldering components on stripboard ( or soldering board)
- Third one was done on the copper board by using the same pcb file and was made by cnc engraving present in my college campus.
After checking fully i send it for fabrication in PCB way
Step 9: Check Gerber File and Send for Fabrication
Checking:
- For Checking Gerber file go to : (http://mayhewlabs.com/3dpcb)
- Copy all the Gerber files and launch the gerber viewer
- Check How the final pcb will look.
Send for fabrication:
- I fabricated the pcb from (https://www.pcbway.com/)
Attachments
Step 10: Getting PCB and Soldering of Components
After getting the pcb, components are soldered and tested.
Step 11: Touch Sensor and Microcontroller Layer
As this home automation project has touch capability, it require touch sensors. Hence we had to fabricate another pcb for touch sensor.This time I fabricated it in College CNC and not from PCB Way.
Step 12: Schematic File and And Getting It Fabricated.
Attachments
Step 13: Finishing PCBs
Both the layers are fixed one, top of another.
Step 14: 3d Printed Case
Casing is done by using 3d printer. Explanation of that would be on Part 2 of Instructables.
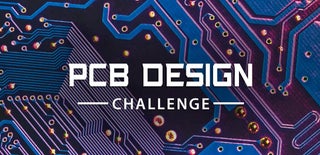
Participated in the
PCB Design Challenge