Introduction: Turn Wax to Metal (lost-wax Casting)
WARNING:
Don protective wear when dealing with molten metal (metal can spit and sputter when being poured, so be careful)
Wear a mask when using investment powder (it contains silica, which is very bad for your lungs
SEE ALSO:
It is possible to make or improvise everything in this guide. Even the investing powder I bought can be substituted by homemade greensand.
Step 1: Designing and Crafting
Imagine if you could mold metal like wax, then have it take the attributes of that metal. This is that. Whatever you carve will be made into metal. Pretty cool, right? You can buy specially made wax, but like a true DIY guy, I made it myself;
Wax Recipe: (by weight)
10 parts white wax (tealight wax)
3 parts hot glue stick
1 part crayon (for coloring)
-Heat on medium
-Stir until mixed evenly
-pour into aluminum foil tins
When you make a ring, you want to make the hole first, so use a ring sizer, or just bore it until it fits fine.
I suggest using a mandrel or ring holder when carving, otherwise your liable to crush the ring. (which i did before)
From experience, a sharp exacto knife and a sheet of coarse sandpaper worked the best for carving, but whatever.
Unless you have a centrifuge caster, make sure you have a decent width to your ring, about 1/16 at the thinnest. It all really depends on your setup, so try casting a couple different styles to see what you can handle.
Step 2: Sprue and Powder
When you have carved all the rings you want, now you need to cast the negative mold. You must attach a wax stem, preferably 1/8 inch in diameter or wider, with a funnel shape bottom, onto the lowest or highest part of your creation. When you attach the sprue to the base, you want the sprue to be at the lowest point of the object. If the object has multiple lo points, you must attach a sprue to each. If you don't, the metal won't flow there. Cause metal doesn't flow up. Always leave at least 1/4 inch between sprues and I recommend 1/2 inch distance from wall. People have cast with thinner walls, but they are better than me at this. Once all the sprues are attached to the base, fit the cylinder over the cap, and fill it with the investment powder. This is the kind of Investment Powder that I use. Each brand varies in the recipe, so follow yours closely. Most recipes ask you to vacuum the mixture before and after you pour it, to eliminate any bubbles. A shop-vac and a modified container will suit our purposes. If you don't have a fancy sprue base and cylinder setup, like these ones, no problem. Improvising is the key to success. If you mess up, don't worry. The powder will dissolve in water, but your carvings won't. After the powder has been cast, leave it to dry in a warm (or hot) place for at least 8 hours. If done for any less, you are liable to get cracks. Cracks are wack, so don't do that.
Step 3: Mistakes Can (and Will) Happen
Don't be distraught, even an experienced artist will still screw up. It's completely normal, and it's how we learn. Expect it to happen at least once during your first time. And second time. And third. You know what, it's just gonna happen a lot. Just persevere. Keep on keepin on. This may not seem like a step, but I guarantee you that it will happen, at some point or another. Be fruitful and recycle what you can. No need to waste.
Step 4: Removing the Wax (by Any Means Necessary...)
If you have access to a programmable kiln, like the ones I have at my school, this step is easy. Simply place the mold in one, set to a slow cone 03 (burns organics), and fire away. If not, then keep reading. Being a DIY guy, I had to try out different methods, and using a oven worked fine. Place all the molds on a aluminum foil covered pan, with a slight angle, so the wax can pour out. Remember, the side with the holes faces down. Set the kiln to 400^F for 30 minutes, then done. If you suspect that the wax isn't quite all gone, then keep it in longer. You will smell wax doing it this way, so I suggest lighting up some candles. Don't worry, this should not harm anything. However, I can't account for everything, so use judgement when doing it this way. Alternatively, a propane torch will work, as I have used it before, but make sure not to concentrate the flame, else the mold will break due to heat stress. PLEASE PLEASE PLEASE WEAR PROPER PROTECTION WHEN HANDLING HOT THINGS. I have burned myself countless times, so learn from my mistakes.
Step 5: The Fun Part.
USE CAUTION WHEN AROUND HOT THINGS!!!
I wore goggles, apron, and a pair of kiln gloves when handling the metal, and I still got burned.
The metal can be anything that you are able to melt. Please vent the area if you decide to use lead. It's nasty stuff.
I used zinc obtained from pennies...don't worry, the pennies I used were so disfigured, the bank wouldn't take them. The scrap yard also has raw ingots.
Anyway, I have a Lee lead melter, which has been modified for my use, and a small porcelain crucible to hold the metal. Heat the metal you plan to use for 30 minutes at it's melting temperature before you cast, just so that it's actually a liquid and not superheated slop.
You can also use the torch here, to melt small amounts of metal quickly.
Pour the metal as directly into the holes as possible. Don't try to get all the holes at once, rather heat the metal between casting, and take them one at a time. This is how you get the best castings.
Never handle the molds directly when casting. They can still retain heat hours after casting, so be cautious
Step 6: The Prestige
This is it. You eagerly waited as the metal inside the mold cooled. You slowly place it into a bucket of water with a pair of tongs. A steaming hiss telling you that you did the right thing. You the metal out, and it looks amazing, all shining and gleaming.
Ok, this is not going to happen. When it comes out it's probably gonna look ugly and pitted. Time to shine.
Place the mold in a bucket of water, wait until cool, then scrub with medium to fine brushes. Avoid being heavy handed, wouldn't want to mar the surface or scratch it, just remove any leftover powder.
Wash your hands after messing with the mold, wouldn't want that powder in your body.
Wear eye and hand protection, along with a mask when sanding or buffing metal.
My dad has been to the ophthalmologist more times than I can count, because he didn't learn as easily; Metal in the eye hurts like heck,and is not good for you or your eyesight.
Remove the sprue with a pair of heavy duty snips or pliers. Grind off the rest, or use a coarse file to remove the remains of the sprue.
Either buff the casting with a wire brush wheel or with fine sandpaper. ( this removes most of the pittings and any imperfections)
Polish to a mirror shine with a buffing wheel and some polishing paste (if you have access to one)
If you don't have access to one, talk to a jeweler, I'm sure one would be happy to help you for a fee.
Other people like the pitted surface, saying that is gives an antique or fatigued look. It all depends on whom you are making the ring for.
I know that this isn't the most detailed instructables, or the most "well-done", but I tried my hardest on this one, and all I want to do is spread the knowledge of what I have learned in the simplest way. A month ago, I did not know anything about casting, but now I've written an instructable about it. Anything is possible.
If you found this interesting or creative, please vote for me.-It is possible to accomplish this instructables without spending any money directly on things. The only thing I had to buy was investment powder, but homemade greensand can be used instead.
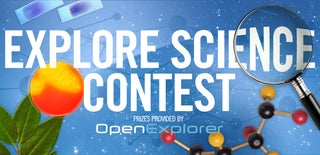
Participated in the
Explore Science Contest
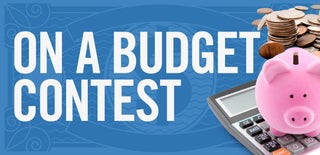
Participated in the
On a Budget Contest
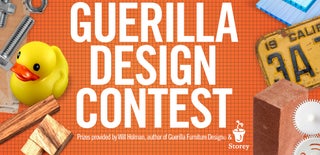
Participated in the
Guerilla Design Contest
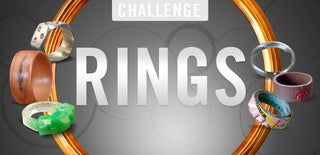
Participated in the
Rings Challenge