Introduction: Power Carving a 50% Scaled Nimbus 2001
Building things is fun. Harry Potter is fun. Sometimes I like to have double fun. I present to you - my power-carved wooden Nimbus 2001 built from Walnut and White Oak.
Attachments
Step 1: Gather Materials and Tools
The project is actually relatively cheap and easy to make if you have a few fun tools! Although Arbortech's tools aren't the cheapest, they really pay off if you find the value in power-carving as a hobby.
Arbortech Tools:
- TURBO Plane: http://bit.ly/2qli0Zf
- Mini TURBO: http://bit.ly/2qll8Es
- Contour Sander: http://bit.ly/2qlJez9
Other Tools
- SAWSTOP Contractors 30” Saw: https://amzn.to/2Luh91q
- Power Drill: http://amzn.to/2q1l5wn
- Sliding Compound Miter Saw: http://amzn.to/2q1klHw
- Miter Saw Stand: http://amzn.to/2p1072e
- Stationary Bench Sander: http://amzn.to/2q1Cq8k
- 4.5” Angle Grinder: https://amzn.to/2FhtDLe
Step 2: Building Your Core Components
I designed my broom in Illustrator to be a 1/2 scale replica using as many photos as I could find - I think I came pretty dang close! The issue with building something full scale really just came down to price for materials. I ended up only paying about $50 for the hardwoods of this project, and maybe another $20 in other things I already had!
Pics 1-2 show me measuring and breaking down the walnut - the length of the broom bristles ended up being around 15". Pics 3-4 show me breaking down a piece of 6/4 White Oak that I had gotten in a scrap pile from my hardwood dealer - I think it was around 25 inches long. I ripped two pieces to width on the table saw (Pic 5), and then laminated them together (Pic 6). The reason I did this was because the broom handle's shape has a bow to it, and you need extra thickness to ultimately make it.
And I glued them up and let them dry over night (Pic 7).
Step 3: Power-Carving - Round 1
I spent about an hour shaping down the laminated walnut piece using the Turboplane (Pics 1-2). Boy does it make a mess - I suggest doing it outside if you can - my shop was a disaster!
To refine the end of the broom (the part that connects to the handle), I used my stationary belt sander to flatten and round over (Pic 3). I think you could do this with the Turboplane or a flap disc as well - or heck, even a lathe, but this worked best for me. I then switched to a 40 grit flap disc which helps you to smooth out and refine the shape really easily (Pic 4).
Last up, I used the Mini-Turbo to add thin lines to give the impression of broom bristles (Pic 5) - I was kind of shocked at how well that simple little technique worked.
Step 4: Power-Carving - Round 2
Next up was shaping the handle - I again used the Turboplane (Pic 1) and my stationary belt sander (Pic 2) to shape and smooth things out. This technique allowed me to create that sublte bow - note that I referenced my design files quite a bit during this whole process.
To really refine and round over the handle, I switched to the Contour Sander from Arbortech (Pic 3) and was kind of shocked out how well it works to smooth things without over-aggressively removing material.
Step 5: Stirrup Assembly and Power Carving - Round 3
All Harry Potter brooms have feet stirrups for their wizard owners to ride. This part was a little complicated to figure out. To build it, I chose to go with another stack lamination / carving process - I just liked the idea of the whole thing being wood.
I took more scrap white oak I had and broke it down on the miter saw and then glued together individual pieces step by step until I ended up with rough shapes of the two core components of the feed stirrup (Pics 1-3).
I then used the mini-turbo to power-carve the shape roughly. It was pretty quick and easy actually - the mini turbo works just like the Turboplane but allows you to get into smaller spaces (Pics 4-5). I don't show it, but after carving, I did some more sanding to smooth and round over each piece, as well as thin the entire profile of it.
Pic 6 shows me using my router table to add a round over profile to each size. Router tables rule.
The stirrups have two thin strips of wood that connect the two pieces - in the movies they fold up in a fun way - but for the sake of this prop, I just made it structurally rigid. Pic 7 shows me sanding down those pieces thin from more oak. I then used glue and my pin nailer to combine everything, resulting in that fun little stirrup piece (Pics 8-9).
Step 6: Oxidizing and Finishing
The broom handles in the movies are made ebony wood (so expensive - hell no!). Instead, I chose to ebonize oak (the whole reason I chose this species of wood in the first place). Before doing anything, I wiped down all pieces with mineral spirits (Pic 1).
To ebonize oak, mix steel wool (number 0000 preferred) with equal parts water and white vinegar, and let it sit for 5-7 days. The solution will break down the wool over the course of a few days and create a solution that rapidly ages wood - and turns white oak black. It's freakin magic.
Pics 2-4 show me ebonizing the oak - it literally turns black almost instantly and continues to darken over 24 hours. Amazing. I also taped off the "feet" part of the stirrups and ebonized just them. If you look at the real model - the stirrups are made from a silver metal, and the feet parts look like black rubber - this seemed like a good solution for me (Pics 5-6).
To darken the walnut and make it more movie accurate, I used Walnut Danish oil which really deepened the color and bumped up the contrast (Pics 7-8). For the handle and stirrups, I used natural danish oil which gave everything a really pretty sheen (Pic 9)
Step 7: Assembly - Round 1
After all the finishes dried, I measured out and marked where I wanted the stirrup to go (Pics 1-2). I ended up sanding down the inside of the piece at an angle for it to better fit back on the broom (Pic 3).
I then marked one more time and drilled out pilot holes (Pics 4-5) - I was going to use two metal screws to attach as I wanted the metal screws to match the metal wiring I'd wrap around the piece (next step!). Using the pilot hole from the stirrup, I drilled into the walnut slowly, and then assembled everything (Pics 6-8). Finally coming together!!
Step 8: Wiring Twisting!
If you look at the real thing, the broom has a metal ring around it which technically attaches the bristles to the broom handle. Since I don't have metal working tools to make something like this, I thought a cool solve would be to twist some thing MIG welding wire together and then wrap it around the piece.
I first tested this technique to see how I liked it visually (Pics 1-3). Simply chuck up wire in the drill, anchor the other side to something stationary, and then power the drill until you achieve a twist you like!
The test came out great (Pic 4), so I strung out a really long piece and drilled (for about 10 minutes) slowly until I achieved a beautifully twisted wire (Pic 5). This technique to create really pretty simple wire is awesome.
If I had a forge to anneal the wire, I would have, as it would have helped release the tension in the wire. I found that by wrapping the wire carefully around a paint can and letting it rest for a few days - the tension mostly subsided and made it easier to work with (Pic 6).
Step 9: Wrapping the Wire
I thought about this for a while and figured out the best solution for assembly. To attach the wire, I drilled a tiny pilot hole (smallest drill bit I had) into the walnut (Pic 1), and then used gorilla glue (Pic 2) to attach it to the wood (Pic 3). It was fast curing, so it only took a moment for me to move to the next step.
I then slowly moved the wire off the paint can onto the broom (Pic 4) - it was actually easier than I thought - it just required a bit of focus and attention to detail to keep the wire tight to the wood, keep the pattern clean and straight, and ultimately not let my hands slip and have the wire completely unravel. Pic 5 shows me using the same drill / gorilla glue technique to attach the other end. I was careful to be precise with this and attach on the bottom on both ends so it would be hidden technically when it is sitting upright.
It looked good no matter what, but I wasn't sure, so I went with this technique. One thing I don't show is that I had the screws that would later attach the stirrups in the entire time - that way I could wrap the wire around those screws, maintain the design integrity, and also have the holes then available to drill the screws back in later on.
Step 10: Assembly - Round 2
To attach the handle to the broom bristles, I drilled out a half inch hole on each piece (Pics 1-2). The tough part for this was just keeping the drill as perpendicular as possible so the dowel would be straight and things would line up (this required a bit of finagling). I chopped up a dowel on the miter saw (Pic 3) and then sanded down the edges to make it easier to hammer in (Pic 4).
I then put wood glue in each end, hammered in the dowel, and connected the two pieces (Pic 5) - so stoked!
Then I used my longest clamp to carefully clamp things together (Pic 6) - the key here was to be gentle and do it slowly so that it cured straight and evenly!
Step 11: Final Assembly
I took the screws out of the walnut piece that I had left in when I attached the wire, and then used just a screw drive to slowly insert the screws back into the stirrup and then into the open holes (Pics 1-2). Little bit of planning went a long way here!
Step 12: DONE!
Um - this thing came out DOPE.
Hope you enjoyed the video and the process - I can't believe how cool it is. Like most props, this serves literally no purpose, but I love building things and I love Harry Potter, so hey - why not!
Thanks for reading - make sure you check out the video in the first step on my YT channel!
See you around! Zach
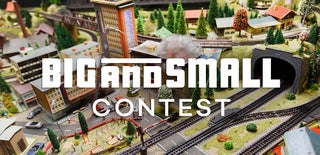
Participated in the
Big and Small Contest