Introduction: Resin and Star Anise Jewlery Set
Nature patterns are amazing, and you can find them everywhere.
My husband likes cooking, so I decided to make a jewelry set with something i can find from the kitchen for my chef and myself.
Step 1: Tools and Materials
I used very limited tools, including
- Cordless power drill
- Hand saw with fine blade
- Sanding paper from 50 grit to 2500 grit
- Buffing kit for power drill
- Hole blade or hole saw which matches the ring size
- Small weight scale
Materials
- Resin (polyurethane, unsaturated polyester or hard epoxy, will talk about this in the next step)
- A pair of earring hooks and some leather string
- Disposable containers for resin
- Some dry stuff that you want to out into the resin
- Dust maskes and Band-aids
- Food color
Step 2: A Little More About Resin
When talking about resin, in the world of art and craft it usually means polyester, epoxy or polyurethane. They all have their own pros and cons that fit different proposes, so there's really no such thing as The Best Resin.
All the casting resins usually come with two major components - the resin itself and the hardener. Curing is a chemical reaction, it is almost irreversible, the bigger volume cures faster. Curing is an exothermic reaction, which means it will release some heat from the reaction, bigger volumes may face some overheat issues.
In general, epoxies are the most friendly for beginners. They have almost no odor, cure slowly so you have enough time to operate and don't need to worry too much about the heat. there are many companies making small batches for hobbies. However, most epoxies are kind of soft or stretchy, it is hard to sand or polish the surface.
Polyesters also know as fiber glass, are harder and cheaper. But they have nasty smell, and can not easily form a smooth surface, so people usually use them in a more professional and industrial scale.
Polyurethanes are cure hard so you can sand the surface afterwards, it's relatively easy to operate, but also the most expensive. They vary the most depend on their different components to meet different requirement. Generally they cure faster than the other two.
I have found some useful links that explain the difference among the resins.
What are the different types of resin?
What kind of resin should I use?
No matter what kind and brand of resin you choose, always remember the most important thing,
READ AND FOLLOW THE DIRECTIONS
Step 3: Get Your Resin
First of all, get your resin.
The resin i used is XTC-3D, it's a epoxy, but since it's designed for 3D printing finishing, the epoxy is made to be hard and cures fast. Another reason is this resin is translucent, so the final pieces may hopefully look like the stars in the soup.
I'v used Easycast and Artresin before, they are both soft and stretchy, almost unable to be sand.
I also bought some Alumilite polyurethane resin, will play with it after it arrived.
Step 4: Find the Stars
Find something to put into the resin. It need to be dry and solid, better that can not absorb any resin.
Now let's make.
Step 5: Mix the Resin and Pour
I made a mold with cardboard and applied packing tape all over the inside. Epoxies won't be stick to the non-sticky side of the tape.
I will cut the block into pieces and reshape them later, so it does not matter what shape or how imperfect the mold is.
Layout the stars on the bottom of mold.
As I mentioned before, curing is exothermic reaction. The faster the resin cures, the more intense the reacting will be. Overheating will lead to the resin cures too fast that you have no time finish the pouring or let the air bubbles release. I placed some ice cubes underneath the disposable cup to mix the two components to cool it done after matured.
I added a little blue food color to tilt the light yellow tone of the resin.
After mixed thoroughly, let it still for couple minuses to let the air bubbles to release. But watch out, pour the resin within the recommended pot life (you can find the pot life on the data sheet comes with your resin.) Once it starts to cure, it well become solid very quickly.
Step 6: Demold
The first one i made looks not cool enough, so i made another one with more food color.
Demold is easy, just tear the cardboard off.
Step 7: Manage and Cut
The first one was not good, so i cut is as will without any layout design.
For the second one, I want to make a ring for him, a pair of earring and a pendant from it.
I used a hand saw with fine blade. You can also use jig saw or other cutting tools. Don't cut too fast, when the epoxy becomes hot, it will be more stretchy or even sticky to the saw blade. If you feel the saw moving sluggish, better to pause.
Step 8: Drill a Hole for the Ring
I haven't made any kind of ring before, so I want to start from it.
At the beginning i thought I could measure the ring size with socket wrench, but then i found his ring perfectly fits my left thumb, things became much easier.
I drilled a hole that smaller than I need, because i didn't have the certain sized hole blade.
Btw the chips removed from the hole looks beautiful, it may be used in my other projects.
Step 9: Reshape the Pieces
Now I need to remove the square edges to make the more gem-like, but unfortunately I didn't have any handy small cutting tool. after a serial of painful attempts with hand saw, X-Acto and utility knife, I decided to jump to the sanding section directly.
The first picture is after cut, the second one is after 50grit sanding.
Sanding will generate heat that make the resin hard to be sand, so don't stick on one side one than 30s. when the surface feels warm, turn a side or switch to anther piece.
Step 10: Keep Shaping by Sanding
Wet them if you can not sea clearly where inside it.
Mark the parts you want to remove with pencil.
When you feel ok with their shapes, move to higher grit sanding papers. I used 100, 220, 400, 800.
Step 11: Enlarge the Hole of the Ring
Since the outline shaping is done, now i can keep working on the "inside" of the ring.
I cut the resin off with X-Acto, it was not as hard as i expected, for the resin is kinda soft and smooth, it's easy to remove chips off as long as the blade is sharp.
Step 12: Dill Holes for Hangers
Step 13: Reapply Resin Coat
After the cut and sanding, some parts of the star anises have been exposed, we need a layer of resin to protect them.
Again, follow the instructions of your resin.
Thin layer of resin cures much slower than bigger volume, so i gonna take a break here let it to cure overnight.
Step 14: Sanding, Sanding, Sanding
If you like the glossy finish of the resin coat, you can stop there.
I prefer matte finish, so i gonna sand them again. This time I will do wet sanding, water can help slower the heating.
Start from 400 grit then move up to 2500 grit.
Step 15: Polishing
Polishing. Not much different.
Inner peace.
Meditation.
Step 16: Finish the Jewlerys With Earring Hooks and Leather Strings
Step 17: And... You Are Done!
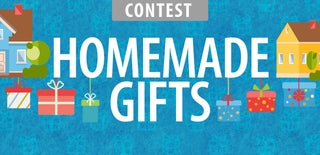
Participated in the
Homemade Gifts Contest 2016