Introduction: Table Saw Drum Mill
Last year I made a new drum shell roller jig for my cabinet saw, so this year I wanted to try a milling attachment idea for rounding the outside face of stave and segmented shells.
There are two common methods rounding these types of drums:
1. Turning them on a lathe manually or with an auto feed setup.
2. Using a router and a DIY jig.
I wanted to determine whether or not it could be done with a table saw and dado stack.
This build is a departure from my usual process, because while I have visualized how the parts assemble, none of the measurements were determined. I'm fitting the parts and notating the measurements as I go, which I'll list in the final step for those interested.
Supplies
3/4" plywood
Screws
Dowels segments
Carriage bolts
5/8" acme rod and nuts
Star knobs
Step 1: Riser Panels
For the front and back panels of what I'm calling the risers, I wanted a dado for a spacer which lands right above the roller jig fences sides. Cutting the dado into the larger panel ensures that it will line up once divided into smaller panels. As you can see in Fig. 1, I cut it on the wrong edge. Fig. 2 is the correct edge.
I didn't have a dado stack for my cabinet saw at this time, so I just made several passes with a 3/16" blade until I had a perfect fit.
The large panels were broken down into a single panel for the inside and two for the outside to span the gusset. This gap doubles as the slot for the threaded axis rod, which will make more sense down the road.
The parts were clamped to the roller jig side in order to get an accurate width measurement for the spacer and top cap.
Step 2: Top Caps and Locking Knob Holes
For the top caps, I opted for rabbet joints. While I had the risers mocked up, I took the time to mark screw hole locations [Fig. 2].
While fabricating the roller jig, I incorporated two captive T-nuts in order to secure future attachments. At that time I made a setup block, which I managed to not lose [Fig. 3]. I used this block to mark the hole locations and then drilled through holes with a small bit.
With that hole as a guide, I used a Forstner bit and drilled a 3/4" on the inside face - deep enough to accommodate a rubber O-ring. This will be the retention ring for the future knobs. The through hole was then enlarged to 5/16".
Step 3: Bearing Blocks
Next parts are the bearing blocks and an auto feed block. These are all 11 7/16" x 3".
Bearing Blocks
These will be the hubs for the threaded rod/axle/spinny bit, as well as the height adjustment to accommodate various shell diameters.
Hole: 1 3/8" hole drilled with a Forstner bit to the depth of the bearing [7/16"] - then a 5/8" through hole.
Grooves: 3/4" groove 1" in from each side - 3/8" depth.
Note: Mating grooves get cut into the inside face of the outside panels and the sides are mirror images, so pay attention. This will make sense down the afore mentioned road.
A section of 3/4" plywood gets glued into the groove and once cured, a 5/16" centered hole is drilled.
Auto Advance Block
Hole: 1" hole drilled with a Forstner bit to the depth of the nut [1/2"] - then a 5/8" through hole.
The shape of the nut is then traced and material removed with a chisel until the nut has a nice friction fit.
Hole Note: The holes aren't centered - they are inline with the straddled gusset, which is purposefully inline with the center of the table saw arbor.
Step 4: Panel Slots
The back panels have the fabricated gap, but the front panel is solid and therefore needs a slot cut.
Once the location was laid out, the top and bottom of the slot was established by drilling a 3/4" hole. The slot was then cut with a 3/4" router bit and you'll notice I took my time to set up and clamp several blocks to the router table top [Figs. 2&3].
The fence is set for the offset/location of the slot. The boards on each side are the stop points for the slot. The board at the front keeps the work piece tight against the fence [Figs. 2&3].
The outside panels then need 5/16" in slots for carriage bolts and I used a similar clamped block setup [Fig. 4].
The last picture should give you a good idea of how the bearing blocks and outside panels integrate.
Step 5: Knobs
For the knobs, I'm using 2" long sections of 2" diameter poplar dowel stock, which were cut using my small parts crosscut sled on the table saw.
Center is found using my shop made dowel center finding jig. 7/8" hole drilled with a Forstner bit to a depth around 3/4" - then a 5/16" through hole.
The carriage bolt was seated with a socket and a hammer and the hole plugged with a section of 7/8" dowel. Once the glue cured, the plug was sanded flush and sharp edges rounded over using the oscillating belt sander.
Step 6: Assembly
I found that the easiest method for assembly, was the clamp the parts in place and use them to self-center themselves.
The spacer for instance. The two back panels were screwed in place with the knobs, the bearing blocks kept them square, and clamps held the space tight within the dado. Then I could drill pilot holes and secure the parts with screws [Fig. 2].
Note: Screw locations were laid out and countersinks drilled prior to this assembly.
The inside panel was then attached, followed by the top cap.
I finished all of the parts with a single coat of shellac. The bearing block runners/keys and mating slots received a liberal coat of paste wax
Then or course I found the risers a home base on the table saw sled/jig wall.
Note: The 1" at the top of the inside face serve two purposes.
1. They are inline with the bearing block slots and bolts, which makes it possible to actually remove the bolts and bearing blocks. I might want to modify them ... or might need to swap a bearing.
2. They allow me to hang the risers on the sled/jig wall.
Step 7: In Use Shots
The drum shell gets clamped between two round plates utilizing long carriage bolts and wooden blocks with imbedded T-nuts [easier to turn]. The acme rod is then threaded through the "infeed riser bearing", through the drum shell assembly, through the "outfeed riser bearing", and into the auto advance nut.
Loosening the two star knobs on each bearing block allows you to adjust the height. You don't need to be concerned with any gauges or racking ... just set a 1/4 board on the saw top and lower the assembly until the drum shell bottoms out.
The Verdict: It definitely works. Once I commit to cutting the acme thread to a shorter length, I think it will perform much better ... eliminate blade chatter. I'll also need a better crank handle.
Additional Uses: The auto advance block could be removed and jam nuts added so that a drum rotates in a fixed position. This could be used for cutting circumferential grooves for inlay banding.
Motorization: Jam nuts could be added to the end of the acme rod so that it could be turned with a drill.
Future: I plan on adding an attachment for milling the inside of the shell, but that will use a track and router.
Crazy Idea: I'd like to test an attachment which mills the outside of the drum using an Arbortech Turbo Plane. I just need one to fall off the back of a truck.
Dimensions
Inside Face: 16 3/4" x 11 7/16"
Outside Large Face: 16 3/4" x 6"
Outside Small Face: 16 3/4" x 4 3/4"
Top: 2 7/8" x 11 7/16"
Spacer: 2 1/8" x 11 7/16"
Knobs: 2" diameter x 2" length
Bearing Block: 3" x 11 7/16"
Step 8: Test Run Video
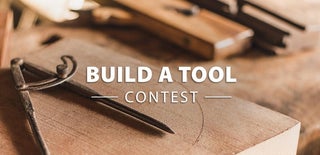
Second Prize in the
Build a Tool Contest