Introduction: Drum Shell Roller Jig
The common method for cutting drum shells to depth, be that a case of working with an existing drum, or cutting a new shell from a full 24" deep plywood tube, is to ride the shell stock along the table saw fence. More specifically ... while constantly applying pressure towards the fence, advance the shell into the spinning blade, and then use a hand over hand technique (envision climbing a ladder) to rotate it 360 degrees.
I'm all for self-policed safety and risk acceptance, but I do not like this method, nor do I recommend it.
More often than not, the stock is wider than it is deep, which is a recipe for kick back. If the leading edge rocks away from the fence, it’s going to create a pinch point and the blade is going to grab.
Best case: The shell is thrown at you. A stave or segmented shell could separate (explode) into pieces.
Worst case: The shell rides over the blade and pulls your hand right along with it.
Safety concerns aside, any change in rotational momentum creates a stop and start point, which results in burning and/or steps within the cut.
Because of all these factors, I wanted to fabricate a jig to make cutting drum shells safer, as well as more precise. For those who don't already know, I reap unimaginable amounts of enjoyment from the process of jig building - the design process, troubleshooting, finished products that actually work, etc. The only thing better in my opinion, is building a second version of a jig, because it makes it possible revise any shortcomings and add the features you undoubtedly envisioned in hindsight.
Supplies
3/4" plywood
Poplar scraps
Wood glue
Screws
Step 1: Version 1 - Quick Overview
My first table saw was a Ridgid TS2400LS.
My jig parameters were:
1. Accommodate 24" long tubes.
2. Fit within the footprint of the saw's tabletop.
3. A self-contained unit for quick/easy setup and storage.
The basic design inspiration came from a quick clip in a Gretsch factory tour video I found on YouTube [linked below]. My version was built using 3/4” plywood, hardboard and 1/2” PVC for the fence side - figuring it’d be a smoother surface than plywood, but I don’t think it mattered much.
Before I knew individual conveyor rollers could be easily purchased, I decided to make my own using 1 1/2” PVC, 3/8” threaded rod/washers/nuts, and sealed bearings. Inspiration for these came from a New Yankee workshop video where Norm made roller stands for table saw out feed.
One end of the jig hooks over the existing fence, which keeps it parallel to the blade and makes shell depth adjustment quick/easy. The other end is removable so that the rollers can be re-positioned for different drum diameters. These holes are re-enforced with aluminum tubing (bushings) so that the threaded rod doesn’t elongate them over time, which would throw off alignment.
Gretsch Video - 1:39 mark for the table saw jig
Old Yankee Workshop Video - 12:28 mark for rollers
Step 2: Version 2 - Quick Overview
Version 1 was a great first start, but it had a few frustrations:
1. It was a bit heavy
2. The PVC rollers had had a little bit of play up and down, but that doesn’t affect the cut.
3. The captive roller design meant you had to remove the end piece in order to adjust the jig for different shell diameters. Good idea for a self contained jig, but not so good for work flow.
Version 2 was designed and built by my bud, Billy, from Calderwood Percussion. He had acquired a cabinet saw, which created the opportunity to address the frustrations and implement improvements.
1. Upgrade the shop made PVC rollers to metal conveyor rollers with tighter tolerances.
2. Change the captive roller hole design to slots for quick and easy re-positioning.
3. Free up the saws fence so it can be used for it's intended purpose.
You can see Bill's jig being used in the embedded video below:
Step 3: Version 3 - the Concept
Version 2 was/is excellent and I knew once I upgraded my table saw, I would upgrade my jig. Based on feedback from Bill, we identified a few more frustrations:
1. The positioning of the ends is a bit finicky. Setting them parallel to the blade while clamping isn't bad, since you can just use the fence, but front to back positioning has to be dialed in so that the rollers are perpendicular to the blade.
2. Slot locations weren't ideal.
3. The jig was now four separate parts that usually got leaned against a wall when not in use.
Design Enhancements
1. Auto-alignment for quick and easy setup.
2. New slot locations.
3. Storage racks.
4. Expandability for milling operations.
Note: This jig was custom built for my current table saw, which is the SawStop PCS31230 w/ T-Glide 36″ Fence.
Step 4: Dadeos and Patch
I started by cutting off a 35" long section from a full sheet of plywood, using my DIY saw track, and then ripping it down to 24" on the table saw. 35" x 24" is a bit larger than necessary, but since this piece will be further divided into four, it accounts for several saw kerfs and a small margin of error.
The next step was to determine dado locations, which I like to use for auto alignment and strength of the overall assembly. It's difficult to see, but I ran masking tape next to the blade and marked the center of the arbor [Fig. 3]. The center dado is inline with the arbor. The two outer/edge dadoes are inline with the front and back edges of the cast iron top. The two infill dadoes are just centered between the arbor and edge dadoes. A sixth dado is marked on the underside of the sheet, which butts up against the front rail.
Note: The plywood intentionally extends past the front rails on the saw, so take that into account during positioning and layout.
Note: I notated the measurements so I'd know where to set the fence during cutting.
A 6" dado stack set to a height of 1/4" was used to make the cuts. I make the cuts slow and steady with the aid of push blocks, so I can maintain a consistent downward pressure to ensure a flat bottom.
I became so focused on cutting perfect dadoes, that I failed to flip the sheet when cutting the sixth dado. Instead of starting over and wasting plywood, I decided to patch in with a strip of poplar. It was ripped from a 3/4" board, glued in place, and I used a long caul to equalize the clamping pressure [Fig 6&7]. A block plane and orbital sander were used to bring the strip flush with the plywood once the glue had dried. After the repair, I cut the dado on the correct side.
Step 5: Grooves and More Patches
Once all the dadoes were cut, I could split the board into the final four sections. Two bottom plates at 6" and two verticals at 5". I wanted the verticals to lock into the bottom plates, so with the same 1/4" dado height, I set the fence to 1 3/4" away from the edge of the blade, and cut a groove in each [Fig. 3].
Note: Be mindful of the bottom dado and cut the grooves as mirror images [Fig 4]. This will make more sense once it's assembled.
I could've left the front dadoes exposed, but I chose to patch them with more 3/4" poplar stock. The vertical board was placed temporarily for alignment of the patches. They were glued in place and clamped up with cauls. The vertical boards were then removed so that any glue squeeze out could be removed.
You may be wondering, "why cut the dadoes in the large sheet when you could cut out the four pieces first and then cut dadoes?" I have a few reasons.
1.It's faster. 6 passes compared to 24.
2. It's more accurate. I know for sure the dadoes in the bottom will perfectly line up with the vertical because they were the same cut.
3. It's a safer option. 24" of contact against the fence compared to 5" - 6".
Step 6: Gussets
With the vertical face set into the groove of the bottom plate, you can see how the matching dadoes allow for perfectly interlocking gussets. The gussets solidify the structure and keep the fence at a perfect 90°.
Surprisingly, I didn't over-complicate the gusset process with extensive layout and measurements. Instead, I marked the stock in place and made the cuts accordingly. 10 gussets were required in total.
1. Determine the required rectangular size [3 7/8" x 5 1/2"] and cut them using the table saw.
2. Determine the desired angle [35°] and cut them using the Rockler crosscut sled on the table saw.
Note: I let the material run long, so that I could trim them flush after assembly.
Step 7: Screw Layout, Drilling, and Assembly Round 1
I switched back into overthinking mode when it came to screw layout. I used a speed square and combination square to mark the centers of all grooves and dadoes. Then a tape measure and combo square to mark screw locations [Fig. 2]. My methodology was to equally distribute the screw locations, while avoiding collisions from the adjacent face. All screw locations were punched with an awl and then drilled with a countersink bit.
A future attachment for this jig will be side pillars or blocks for milling operations, so I took the time to install two T-nuts within each fence. A setup block was used to mark the locations matched and forstner bits to drill the holes. A shallow 7/8" hole for the flange, and then a 3/8" bit for the through hole. T-nuts were then hammered into place [Fig. 4-7].
Prior to assembly, I wanted to remove all my pencil marks. Instead of killing 3 hours and 17 erasers, I used acetone. It's quick, easy, and effective.
For assembly, I used clamps to pull the parts tightly together, drilled 1/8" pilot holes, drove the screws in most of the way with an impact driver, and finished them up by hand with a screwdriver [Fig. 9-11].
Note: I didn't use glue just in case I want to disassemble and change anything in the future.
With both fences assembled, I could now trim off the excess gusset material using the table saw [Fig. 12].
Step 8: Front Stop and Back Support
The front stop and back support are just 6" x 2 1/2" sections of plywood. The lock into the bottom dadoes and are secured with 3 screws each.
The front stop registers against the front face of the table saw rail. The back support sits on top of the back rail, so that when clamps are applied, the jig doesn't bow under pressure.
Step 9: Slot Layout
With the foundational structure complete, it was time to add the roller slots and I opted to cut them into a separate 4 3/4" x 35" piece of plywood for a few reasons:
1. If I messed up, I just had to remake the one part instead of the entire jig.
2. If in time I determined a different spacing would work better, it could easily be changed.
3. Cutting slots in the existing single face would undermine the purpose built solidity.
To determine the location of the slots, I placed the jig on the saw with the board clamped to the face, and marked the center point of the arbor. The inner set of slots are spaced 6" apart, so 3" to either side of the arbor center point. Additional slots are spaced 2" on center.
Determining slot depth was a bit more involved because I wanted the rollers to sit as low as possible, while still allowing the fence to move underneath. I used some scrap wood blocks to get a rough idea and then made several test cuts until I found my ideal depth of 2" [Fig 2 & 3].
Step 10: Jig Set Up
I recently built a router table jig for cutting precise and repeatable slots. It's actually a multi-function jig, but for this project, I'm just using the slot cutting feature. The quick explanation is that a center rail clamps to the router table and a sled rides on that track, making it possible to advance your work piece into the bit. If you want to see how it was made and how it works, check out the Multi-Function Router Table Jig Instructable.
With the jig in place, I needed to set it up for repeatability in regard to slot depth and spacing.
Depth: I just placed a board of proper width across the back of the jig and clamped it to the table. It's a simple, horizontal depth stop.
Spacing: I cut two 1/2" slots with a 2" on center spacing into a test board and used that to determine the location for an indexing pin. That position was marked using a 1/2" fortsner bit and a light mallet tap [Fig. 3]. The same bit was then used to drill a hole into the sled [Fig. 4]. I ended screwed the pin in place from underneath just to ensure it wouldn't move during cuts [Fig. 5].
Step 11: Cutting Slots
Slot cutting started with the inner set because they are done without the indexing pin. Since I want an identical pair of these boards, I clamped a stop block to the tabletop for matching alignment [Fig 1-3].
Note: It is necessary to clamp the work piece to the sled. Because of how the bit is entering the wood, some climb cutting is taking place and if allowed, the board will be pulled to one side -- into the rotation of the bit. I recommend a clamp on each side.
Once the inner set is done, the indexing pin can be installed on the sled for the remaining cuts. Just register the existing slot onto the pin, clamp the board to the sled, make the cut, move the board, and repeat - just like a box joint jig [Fig. 4]. Since the saw's arbor location is off center in relation to this board, I ended up cutting 5 slots on one end and 6 slots on the other.
The jig lacks dust collection and makes a mess, so I used my respirator and ran the shop vac every few cuts. Placing the boards beside each other as a mirror image demonstrates the achievable precision with this set up [Fig. 6].
Step 12: Screw Layout, Drilling, and Assembly Round 2
Another round of screw layout ... this time using my shop made gauge to mark in 5/8" from the edge and then a tape measure for intersections. Holes punched with an awl and drilled with a countersink at the drill press. I used six clamps to ensure the board was pulled tight to the vertical face and bottom plate before drilling pilot holes and applying screws.
You could apply finish, but I decided to leave the plywood in it's raw state.
Step 13: Glamour Shots and How It Works
Setup of the jig is quick and painless.
The left fence sits flush with the left edge of the saw's tabletop and the front stop registers against the front rail. One clamp on each end holds it securely in place.
The right fence position is determined by the length of your rollers [I used 45"]. After the initial setup, you can just notate the location as related to the saws tape measure and never need to fuss with it again 28 1/8" in my case]. As before, the front stop registers against the front rail and apply the clamps.
The rollers just drop/slide in from the top at your desired location. The smaller the drum diameter, the closer to center the rollers need to be.
Roller Information
- They are available in several diameters, but I went with 1.9" arbitrarily.
- Shaft size options are 1/4" and 7/16". I went with 7/16" because they fit well in a 1/2" slot - no major slop, but also no frustrating binding.
- They are available in a large range of lengths, so building to fit your needs is easy.
- I found them on Amazon and Ebay, but Grainger was cheaper and I had them shipped to the store for no fee.
- This is the exact roller I bought: Galv Replacement Roller, 1.9In Dia, 45BF [You'll need two].
I considered adding integrated clamps similar to my router table fence, but they just added bulk and made storage more of a hassle. The use of standard F clamps is easy and quick enough.
Step 14: Storage
Since I enjoy organization and like everything in my workshop to have a home, I built custom storage racks for the jig components.
The fences hang from a simple ledge, which has a centered gusset for strength. Two holes were drilled into the top board and then plugged with protruding sections of 1/2" dowel stock, which acts as retaining pegs. This ledge was secured to the wall with two screws. Each fence has a correlating 5/8" hole drilled halfway through the back support. Hole slips over the peg, ledge supports the weight, and peg keeps the parts from sliding forward.
Note: 1/2" pegs and 5/8" hole to alleviate binding.
The roller storage is reminiscent of a pool cue rack. A top and bottom plate are connected to a back panel with interlocking dadoes and screws. The bottom plate has gusset for strength since the pair of rollers weigh in at 14 lbs. Using a 2" forstner bit, the top plate gets through holes and the bottom plate gets
Fence Rack
Back: 12" x 2 3/4"
Top: 12" x 2 1/4" [1/4" deep x 3/4" wide rabbit on the back edge]
Gusset: Cut to fit
Dowel Pegs: 1/2 diameter
Roller Rack
Back: 48" x 5 3/4"
Top: 5 3/4" x 2 7/8" - 2" through holes
Bottom: 5 3/4" x 2 7/8" - 2" partial holes with 1/2" centered through hole
Step 15: The Video
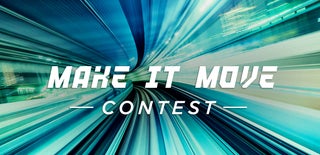
Second Prize in the
Make it Move