Introduction: The Secret Valet Box
I'm slowly losing my mind - at least the memorable parts. That is to say ... my memory is fading. There are a lot of random/useless facts and nostalgia rattling around in the ole calcium vault, but those seem to have steady footing. It's the untethered items of everyday life that are suffering due to my absent mind - glasses mostly, but also keys, phone, or whatever object I just had in my hand 5 seconds ago.
I guess I could get a glasses strap, key lanyard, and a wallet chain, but I'd start looking like the rigging on schooner ... or a library custodian.
My current solution is to make a valet box, so I'll always know where to find my stuff ... unless I forget where I put said valet.
My design is a simplistic, rectangular tray, with dovetail keys for miter reinforcement. However, I'm adding a "secret" compartment for items I don't want stored in plain sight ... passport ... ninja star ... prized Gameboy cartridge ... orange tic tacs.
Let's get on with it before I forget what we are talking about.
Step 1: Internal Box Fabrication
I'm starting with the hidden box, so it can be used when making the outside box. Some quick thought was given to dimensions - both the overall and relative flavors. 6" x 9" for the exposed valet storage space tickled my fancy and since I'm using 1/2" stock, that meant 5" x 8" outside dimensions for the hidden box.
Note: I'll add all my dimensions in the last step of this Instructable, for those interested in the minute details.
I started by ripping some 1/2" plywood into 2" wide strips. These are wider than I need, but I'll trim the box to final height after it's built. The box sides were cut using a small parts cross cut sled and stop block on the table saw. Rabbets were cut on each end of the long sides (to accept the sides), as well as the bottom edge of all four sides (to accept the bottom).
The rabbets provide a level of auto alignment, which simplifies assembly. Glue was applied to every rabbet, the sides tacked together with pin nails, and then the hardboard bottom dropped in place. I ran packing tape around the perimeter of the box for a bit of clamping pressing and a small weight pressed the bottom tightly into it's rabbet.
For the bottom lining of this box, I used 1/8" EVA foam. A specifically shaped pocket was then cut into a layer of 1/2" EVA foam. Your storage needs may vary and alternate options could be felt, leather, flocking, nothing, etc.
With my item in place, I was able to determine how far I could reduce the height, and removal was done using the table saw, followed by a few light passes through the drum sander.
Step 2: External Box Fabrication
It's worth mentioning that I reapplied a layer of packing tape to the sides and top of internal box, which will act as a shim while building the outside box. I want a tight, slip fit, but not an immovable plug.
For the outside box, I used a poplar 1" x 6", and the first step was to thickness it to 1/2", which was achieved using the drum sander. The board was then ripped into two equal sections (2 5/8") - again wider than necessary. Each section will become one long side and one short side.
With the table saw blade dialed in at 45 degrees, I used my small parts miter sled to make all the angled cuts. I used the internal box to mark lengths - sneaking up on the cuts as necessary.
1. Cut the initial miter [Fig. 5].
2. Place the stock against the long face of the internal box to mark the cut line.
3. Cut the stock a bit heavy, so as not to over cut and trim until the fit was perfect.
4. Use this piece and a stop block to cut the matching/opposing side.
5. Clamp a finished long piece to the internal box, so you can repeat the process for the short sides [Fig. 6].
Note: It's a good idea to label your parts, so you can keep them in order during assembly - especially if you have continuous grain wrapping around the sides [Fig. 7].
To determine the placement of the bottom, I used the internal box, the bottom stock (3/16" hardboard), and my phone case. I left a little extra at the bottom for sanding/truing, got the measurement, and cut the grooves on the table saw. Since the hardboard is 3/16" thick and the blade kerf is 1/8", I took one pass on all the parts, nudged the fence, and made a second pass. The side were then used to determine the size of the hardboard panel - place it in the grooves, make a mark, adjust the table saw fence, and make the cut - no tape measure needed.
Much like rabbets on the first box, the grooves and bottom panel with help auto align this box during assembly. The miters are end grain, which tends to soak up glue, so I apply it in two stages - first miter coat, glue in the grooves, second miter coat.
Assembly is just a matter of locking the sides onto the bottom panel and ensuring the corners all close up nicely. Packing tape was again used for clamping pressure. I don't think it was necessary,but I used the internal box as a means of keeping the sides square.
Note: The packing tape shim pulled double duty by ensure no glue squeeze out would lock the boxes together for eternity.
Once the glue was cured, I used the drum sander to flush up the two box bottoms, as well as flatten the top edge.
Step 3: Cutting Dovetail Slots
In order to cut the dovetail slots using the router table, I made a small sled from shop scraps. It's just a 3/16" hardboard base with two mitered wedges (the thicker the base, the more accessible bit height is lost). Ideally, you'd have your height determined and have a true zero clearance situation, but I was winging it, so my fences got chewed up. I also had to add a spacer to get the box into the cutting field. Lastly, I made a scrap wood holding block to keep the box held firmly in the groove of the sled AND keep my fingers away from the bit path.
Most of the time is spent setting up the cuts, then it's just a matter of advancing the sled and work piece through the bit. Resist the urge to pull the sled backwards - just make the full forward cut, kill the power, let the bit come to a stop, and then remove the work piece. Now you can reset the sled, rotate the box to a new corner, and repeat.
Tip: Precut your sled so that the end position of the bit is buried in in the back fence. This is for safety, but also eliminates the chance of taking a bite our of your work piece if you move it before the bit stops.
Tip 2: Use a stop block for the end position, to eliminate any second guessing - more safety and work preservation.
Tip 3: Clamp a secondary fence to your table, which hold the sled against the fence. This eliminates any wandering and elevates precision - same principle as a feather board.
Step 4: Locking Peg Slot
For the locking peg slot, I just changed to a 1/4" straight bit. The sled was centered over the bit and then a stop block clamped on each side. The selected corner was placed into the slot, bit slowly raised until it pierced through to the inside, and then the sled moved to the left and right to cut the slot.
Note: The height of your bit will be equal to the future locking peg length. You want enough to actually lock/hold the internal box in place.
Note 2: Be mindful of your left and right travel. Set the stop blocks closer than you think necessary at first and adjust for a second cut if needed. You want the peg to be able to slide left and right out sight, but you don't want the slot cut width to exceed your dovetail slot on the exterior. Ideally, my slot should've been more narrow.
Step 5: Cutting Dovetail Key Stock
Milling the dovetail keys is a surprisingly simple process. In fact, the hardest part was deciding on which wood to use. I narrowed it down to my dwindling supply of pallet padauk, but still had to choose between the orange/red heart wood and the spalted sap wood. In the end, I decided to save the cool spalted wood for some future project using darker wood.
I ran test cuts with poplar to figure out my process, as well as determine the size of stock with which I'd need to start (11/16" width x " height x 18" length). My supply of pallet padauk is drying up and I don't want to waste more than absolutely necessary.
Side 1 - The Quick Side
Set the fence so that your work piece makes full contact with the cutting edge. If you end up with a flat area at the bottom of the work piece, the fence is too far back [Fig 5]. If that's the case, just move it forward and take another pass until you get a crisp bottom angle [Fig. 6].
Side 2 - The Precision Side
Move the fence back more than the width of the desired finish key. Don't even try to get a perfect cut out of the gate - messing up isn't worth the risk. Just take a pass, test the fit with your box, nudge the fence forward, take another cutting pass, test the fit. Repeat until you get a nice snug fit.
Note: I milled both a test piece and finish piece for each step, so that any mistake occurred on the sacrificial stock. I'd cut a length of poplar and test the fit on the box. As long as the cut didn't remove too much material, I'd make the same cut on the Padauk and then adjust my fence. If the fit was too loose, I just saved myself a lot of frustration.
With the key stock slab finished, it's just a matter of slicing it into individual keys. Again, I'm not going for a perfect fit. I'd rather have extra that can be trimmed and flushed up to the box once the glue dries. I decided on 1 1/4" lengths and made the cuts at the bandsaw using a sled.
Note: Before slicing and dicing, I cut off the unused portion of the paduak board to live on in the scrap bin and future projects - waste not, want not.
Step 6: Key Glue Up, Trimming, and Sanding
Glue up is easy, but I took a minute to prepare for the operation because I know my brain ... it likes to throw wrenches. One of these keys will be a sliding lock, so we don't want to glue it in place. One could simply set one of the eight to the side and carry on with business, but not me. My mischievous gray matter would wait until I'm distracted ... probably singing along to the freshest K-Pop track ... and BOOM - I'd spread glue in all eight key slots. Not this time, man in gray ... I taped over the slot.
Spread/brush glue into one of remaining seven slots, spread/brush glue onto one of the seven keys, slide the key into a non-taped slot, repeat six more times, queue up a K-Pop playlist and wait for that glue to dry.
To trim the excess key stock, you could use a flush cut hand - otherwise known as a pull saw. I find this to be inconvenient and prone to mistakes, so I usually opt for the bandsaw. However, my bandsaw suffers from chronic drift and chatter, so I now prefer to use the table saw. A low profile spacer fence solves the problem of the protruding keys not being able to register against the fence [Fig. 6]. With a high tooth blade and accurate fence setting, you can get flush cuts that require minimal sanding.
Note: If you aren't comfortable with this type of cut, you could clamp the box to a sled - as long as your blade height is able to accommodate both the sled and box.
Bandsaw method example can be seen in The 2 Player Shut The Box Game Instructable.
Most of the smoothing work was done by the table saw and/or drum sander, but I did finish sand both boxes with 150 and then 220 grit sandpaper. The locking key was finessed independently because it kept moving and I didn't want to nick up the edges. I'd just drag each side across 100 grit sand paper a few times, test the fit, and repeat until almost flush [Fig. 10]. The final flushing and smoothing passes were made with the key installed and I found that pressing a piece of wood against the adjacent edge was enough to keep it from moving [Fig. 11]. A tack cloth was used to remove all the dust.
Tip: I recommend hand sanding with the grain. The orbital sander tends to drive the fine paduck dust down into the pores of the poplar, which results in a blotchy pink hue. I know from experience and I don't like it!
Step 7: Finishing
The bottom of the internal box had a few voids in the plywood, so I plugged them up with wood filler, sanded the patches smooth, and hid the atrocity with black leather dye - Fiebings USMC Black.
For finishing, I'm going with clear spray shellac - emphasis on the "spray." If you try to wipe on the finish, you will get color transfer from the padauk to the poplar - lovely pink streaks ... another lesson I've learned the hard way. I recommend two separate and very light "seal coats." If you go too heavy, you'll get runs and guess what? Yep, the padauk will bleed red into the poplar. After the seal coats, you can switch to wiping finish with a rag, but I stuck with the spray.
Two light seal coats of shellac, light sanding with 220, another coat of shellac - repeat until you are satisfied.
Once that drid, I applied a coat of renaissance wax, let it haze up, and buffed it out.
For the lining of the top box/tray, I went with a timeless black suede. I did test a reptilian patterned felt, but it was rather thin and I wanted more noise dampening for when dropping keys and such into the valet. It was cut to size with a razor knife and the accuracy aid of a straight edge.
Step 8: Locking Mechanism
The locking mechanism is a simple retention peg, which engages with a notch in the internal box. Layout and assembly can be a bit finicky, but it's not bad.
Notching the internal box
I supposed you could cut this notch at the same time you cut the slot into the external box, but you'd be raising the bit blindly and I didn't want to risk it. Instead, I nested the boxes and used a pencil to mark the area to be notched. I made the cut on the table saw since I have a sled to do so, but it could also be done on the router. I generally find the table saw to have more control and I really didn't want to risk any plywood blowout or other possible mistakes at this point. I did a few test fits with a 1/4" dowel and refined/enlarged the cut as necessary.
Layout
To accurately mark the hole location in the sliding key, I just used a 1/4" brad tip drill bit. Once I obsessed over its "perfectly centered placement," I pressed it into the key to leave an impression. I then used the drill press to bore the hole, using the cutting sled to hold the key perpendicular to the quill.
Peg
I started with a random length of 1/4" dowel, inserted it into the key hole, and marked the desired cut length, which was made using the bandsaw sled. A test run revealed that the peg was dragging at the top, so I sanded in a bit of a flat [Fig. 12].
Assembly
Once I was happy with the fit, I added glue to the peg hole, wax to the key and slot, inserted the key into the slot, and then pushed the peg into the hole form inside the box. At that point, I let the glue dry before further fiddling. Further fiddling entailed sliding the key to it's furthest left and right positions and sanding the peg flush to the box interior, so as not to restrict the interior box from sliding in and out.
Note: Go easy on the key/peg glue. Too much squeeze out and you may just lock it all in place.
Step 9: Glamour Shots
I'm pretty happy with the end result. It holds all my stuff, so it can expect a glowing service review and a raise next year. The lock mechanism is simple, yet effective ... and was fun to make.
Obviously the overall height of the box may raise some flags regarding unused space below the upper tray, but really ... how many people are walking around your house with that level of analysis? Is Sherlock Holmes or Monk coming over for dinner? To be fair ... I am such a guy, and I'd probably notice it, but this is in a bedroom on a nightstand - not in a hallway or living room.
Dimensions [Thickness x Width x Length]
Internal Box Finished
Long Sides: 1/2" x 1 1/4" x 9"
Short Sides: 1/2" x1 1/4" x 5 1/2"
Bottom Panel: 3/6" x 5 1/2" x 9 1/2"
External Box Finished
Long Sides: 1/2" x 2 9/16" x 10"
Short Sides: 1/2" x 2 9/16" x 7"
Bottom Panel: 3/16" x 6 3/8" x 9 3/8"
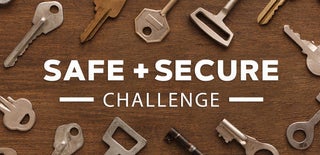
First Prize in the
Safe and Secure Challenge