Introduction: Wet Molded Credit Card Wallet
Hi guys! I'm going to make a card wallet through wet forming method. Wet forming leather is one of the most interesting techniques of leather crafting. Today, I'd like to show you how to make a mold on your own with split leather. I tried to make it as clear and simple as possible. I hope you find it helpful.
Supplies
- Exterior: a sheet of leather 31cm x 16cm (12in x 6.3in) and 1.5mm (4oz) thick (roughly)
- Lining: a sheet of leather 31cm x 16cm (12in x 6.3in) and 1.0mm (2oz) thick (roughly)
- Mold: Split leather 15cm x 18cm (5.9in x 7in) 2mm (3oz) thick (roughly) X 4 set
- Utility knife /Mallet /Ruller/ Awl/ Tong/ Small clamps
- Pricking iron (5mm spacing/ slanted)
- Hole punch : 5mm / 3mm diameter (for 13mm eyelet snap button)
- Edge beveler size #1
- Needle (John James #4)
- Thread Vinymo #5 (6mm thick)
- PVC Punching board 15cmX20cm (roughly)
- Eyelet snap button/ Setter
- Edge beveler (size #1)/ Sandpaper (400 grit)
- Leather dye/ Piece of sponge
- Wood slicker/ Tokonole (Burnishing Gum)
- Water/ Tray (for soaking leather)
Step 1: Making the Pattern
I usually use Photoshop(CS6) to make patterns. You can use any programs that you find easy to work with (e.g. CAD, Illustrator, MS Paint). The pattern is 4 pages. As usual, paste the pattern on a thick piece of paper.
Step 2: Making a Mold (Part.1)
I'll use split leather to make a mold. Split leather is the inner most layer of leather when a skin is divided into several layers. It can be used in many ways, so make sure to keep this when you buy your leather. I used Buttero split leather and cut the leather according to the pattern. I made 4 pieces of each part, but the number can vary depending on how thick the leather is. The thinner the leather is, the more likely you get the thickness you want. Mine is roughly 9mm thick. (I wish I made it thicker though.) I smoothed the sides with a sandpaper.
Step 3: Making a Mold (Part.2)
I marked around the edge to round out the corners. As you move the mark inward, the mold becomes rounder. Rub the surface until you get the right curve. I put some water and burnished it (not necessary). And, I pasted it on the center of the PVC punching board. You can take it off the board clean later. The mold is ready now.
Step 4: Soaking the Leather
I used two different types of leather for outside and inside (1.5mm thick Pueblo for exterior and 1mm thick Natural Buttero for interior). Cut them according to the pattern, and soak them for 15 minutes.
Step 5: Forming the Leather
After soaking, the leather becomes softer. Put them on the mold, fasten the clamp, and let it dry for a day.
Step 6: Reinforcing the Leather
Next day, you can see the leather well shaped and hardened. Glue the natural leather inside Pueblo leather. Through reinforcement, the shape is well preserved.
Step 7: Making the Front Panel (Part.1)
Mark the button area and upper line on the molded leather with an awl. Then, cut the upper side according to the marked line. You can do this more easily using the mold. Mark stitching holes with a pricking iron and pierce them with a flat awl. Sew the upper side and cut the extra part.
Step 8: Making the Front Panel (Part.2)
Fasten a 13mm eyelet snap button. (You can use other types of button.) Make stitching holes with a pricking iron following the guide line drawn with a wing divider.
Step 9: Making the Front Panel (Part.3)
Dye the edges, and burnish with Tokonole. Then, I stamped my logo.
Step 10: Making the Back Panel
I'll make the backside now. Glue the two leather pieces together, and cut it following the pattern. Make stitching holes around it. The number and intervals of the holes on this backside is identical with the front side. Fasten an eyelet snap button on the lid.
Step 11: Gluing to Assemble
Scratch the surface to glue. Glue the front side and the backside together, making the stitching holes align.
Step 12: Sewing
Sew all around to assemble the two parts (front and back).
Step 13: Finishing the Edges
Smooth the edges with a sandpaper and bevel the edges. Dye all the edges and burnish with Tokonole. Then, it's all done!
Step 14: Done!
Through this project, I wanted to suggest wet molding is possible without ready-made wood or plastic molds. Think outside your mold and create one of your own! Thanks for watching my work and have a great day!
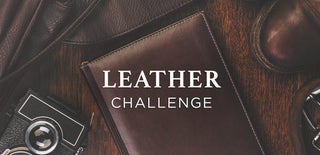
Second Prize in the
Leather Challenge