Introduction: Wooden Rings Made From Golf Clubs (Woods)
It seems that everyone has old golf clubs. They live as a future promise - that someday, just maybe, you'll play golf. It seems an amiable goal, but really if you were to actually use these old things, you'd probably give up immediately. So why not turn them into something interesting? I left mine out by the curb for free, and had no takers. Eventually, night came about and I thought it'd be a bad idea to leave items that can be used for vandalism outside, and brought them in. Upon staring at them in my workshop, I thought that at least the wood would be useful, so I cut the shafts off, kept the heads, and waited for an opportunity to present itself.
Golf clubs have to be really, really dense and strong. Of course, there's plywood, skateboards, or other laminated wooden structures to be utilized for this purpose, but the probability of voids in the wood layers, lack of strength, and the uniform layering may make other materials less than desired. Golf clubs like these were formed under tremendous pressure, and given that they're fairly small, the layers of wood to be laminated can be chosen free of voids, whereas it's more difficult to do with large surface area laminate woods. And also because they're compressed into an interesting, non-2d shape, the grain isn't a simple horizontal structure.
The process is fairly simple, and can be done in a variety of ways. You don't even have to use golf clubs. You can substitute a bunch of different materials. The basic method is simple enough for anyone with enough elbow grease, and drills.
Supplies
- Wooden Golf Clubs
- Super Glue (cyanoacrylate)
- Food Coloring
- Drill (Press)
- Isopropyl Alcohol (rubbing)
- Hole Saws and Drill bits
- Sandpaper - 220, 320, 400, 600, 800, 1000, 1200 grit
- Polishing compound
- Hacksaw
Step 1: Cut Off Shafts / Prep
It's quite difficult to drill into a head of a club with the shaft in the way. Just cut it off close to the head using a hacksaw.
Next, you'll have to unscrew the metal base off the bottom. The screws may be quite old, impacted with dirt, or the heads will be stripped. I was successful in just using a simple screwdriver to remove most, but on a few, I had to drill the head of the screw off. After that, It's as simple as prying the metal plate off with a flat screwdriver or similar tool.
You'll want to investigate places in the head where you won't want to drill. Some spots may have leftover screws, lead weights, or parts of the shaft still embedded in the head. You can be creative and drill wherever you desire. For example, I used part of the plastic head face as part of the ring. Maybe you want a part of screw embedded in your ring? Do whatever you'd like.
Step 2: Drill the Ring's Basic Shape From the Club
- You'll require at least two drill bits / hole saws. At least one hole saw will be necessary - a hole saw whose inner diameter is desired for the outer diameter of the ring. You can use any type of drill for the inside diameter of the ring. You will want drill bit based upon the premise of The Price is Right - one close to your ring size without going over.
- You can use a variety of drilling devices - ideally you'll want a drill press and a vise to hold the workpiece stationary. That way you can drill both the inside and outside diameters without the workpiece moving for concentricity of both drilled holes.
- Hold the club in a vise and drill the inside diameter hole (the smaller of the two drills).
- You can get the drill / vise position setup using the hole saw to see where you'll actually be drilling. Then proceed to the next step.
- Drill the inside diameter with the smaller drill bit. Don't move the workpiece.
- Drill the outside diameter of the ring using a hole saw.
- You'll be given a long drill core cylinder in the basic shape of a much too wide ring. You may have not been able to drill it completely from the club if you were worried about the hole saw drilling into the vise holding the club. You may have to crudely saw with a hand saw whatever remaining wood holding the ring core from the rest of the club.
- Drilling tip: the slower the rpm of the drill, the less likely you'll find the metal drill heating up and leaving burn marks in the wood that'll need to be sanded out. Go slowly, lift the drill up and let it cool off if needbe. Sanding burn marks out of wood is a very annoying task and will take way longer than drilling slowly.
Step 3: Cut the Ring to Width
You'll be left after the drilling process with a cylinder that's too long. You'll want to trim the cylinder to be the right width given your desires. Remember, the wider the ring, more of your finger and varying diameters will be covered. Narrower is easier to calculate for fitting your finger. Wider may look nicer, but plan to slightly oversize the ring since it will be wider.
- Cut the ring to width using a fine tooth saw blade. A hacksaw blade will work fine.
- Place a piece of sandpaper on a flat surface and sand the edges of the ring flat trying to keep each side parallel. Pick up the ring every so often and check where the ring is wider than another spot and sand that by holding only that spot on the sandpaper. It truly does not need to be accurate to the thousandth of an inch or anything, just so that your eyes can't tell. I used 320 grit for this step. You could do it faster with 220 or harsher grit.
- Sandpaper tip: the smaller the number, the harsher it is. 320 is finer than 220 for example. Unless you need to sand a whole lot of material off, I wouldn't recommend going below 220. You don't want to leave any large scratches in the wood and it'll stick out like a sore thumb once stained.
Step 4: Sand the Ring to Final Dimensions
- Sand the outside using 220 grit or 320 grit paper. Carefully shape the ring how you want it - contoured / rounded edges vs. completely square, having a large radius on the outside for example. It's up to you. I recommend sandpaper for this because it's really slow, and reduces the opportunity to remove more than you want.
- Sand the inside of the ring via the same method. If the ring is really small in diameter, you can use a piece of sandpaper wrapped around a pencil.
- Ensure the ring fits your finger. If it's too tight, sand the inside more until it does. Remember the superglue finish will add a tiny bit of material, making the ring fit tighter. So, if the ring is way too tight, expect it to be tighter later.
- Finish sand all surfaces with 320 grit.
Step 5: Stain the Ring With Food Coloring.
- Get a small bowl that won't stain and add maybe 1-2ccs of rubbing alcohol.
- Add maybe 1-2 drops of food coloring per CC. This isn't extremely critical. If you want darker colors, add more.
- Put your ring in the food coloring mixture and swirl it around. periodically pull it out of the mixture to check color. If you want it darker, leave it in longer or add drops to increase the concentration of food coloring. If you want lighter, add less food coloring and pull it out sooner.
- clean it off with whatever, a Q-tip or paper towel to really check color. It can be deceiving when in the mixture since dye will be on the outside of the ring but not really absorbed making it look darker than it is. Let it dry and see what it looks like. You may want to put it in the dye longer. It'll appear lighter when dry and darker once superglue is applied.
Step 6: Seal in the Dye With a Clear Coat / Super Glue
- Use super glue to seal in the finish. I used Gorilla Glue that has a brush. I find that's easier. You'll want a runnier super glue rather than a gel. Cyanoacrylate is cyanoacrylate no matter what the brand is. If it's that, you'll be alright.
- Starting on the inside, apply a thin layer of super glue to the inside while touching the outside. Refrain from getting it on your fingers. Set down in a way for it to dry for at least a few minutes. Add multiple thin layers.
- Now that the inside is done, you can touch the inside and work on applying layers to the outside. Set up to dry by setting the ring on a stick of some sort. I used an empty pop can and a q-tip.
- If you mess up, drop it on the ground and get it covered in dirt or hair, use some fingernail polish remover on a q tip and wipe it away once the super glue is dry. It's not ideal, but better than throwing your work so far in the trash.
- Let dry overnight. It's important to let each layer fully dry prior to additional coats. Once completely done, you want to insure it's completely dry before sanding. If you don't, under layers can still be tacky and sanding will go pretty poorly.
Step 7: Final Sanding / Polishing.
- Finish sanding the superglue down to it's smooth and final dimensions with some courser sandpaper, maybe 320 or 400 grit. Be extremely careful not to sand through the superglue! Add a very thick layer of glue to reduce your chances of doing this. Starting with finer paper also reduces this risk.
- You'll need to sand progressively from course to very fine grit. Bear in mind that the courser the paper you start out with increases the deeper scratches to be removed with finer grits. I'd recommend starting with 400 depending on your glue job. If it looks pretty smooth, start with a finer grit, like 600 or 800.
- After removing scratches from the previous grit with a finer grit, move onto another finer grit, and so on. 400 to 600 to 800 to 1000 to 1200. This is fairly time consuming, but thankfully rings have a very small surface area.
- Once you get to 1000 or 1200, find a soft cloth and use some car paint polishing compound ( doesn't need a lot) to give it a nice shiny luster. You can increase the polish with a felt tip polishing mandrel on a drill or low speed rotary device. Be careful of high rpm tools in case the buffer heeats up and just melts the surface you're trying to polish.
- If you happen to mess this portion up - sand through the glue for example, stick the ring back in the dye solution for a long time, re-coat the super glue, and re-sand. This is not ideal, but if it happens, it's better than throwing the item away.
Step 8: Options:
- Some of my rings have metal on them to make them more interesting. I thankfully have a metal lathe to make such things. Ones with edges above the wood were made with two halves of some stainless steel I had. The two halves get glued to the center wood ring cylinder. Once dry, I stained and superglued the wood.
- If you can find a metal ring, like a piece of copper pipe, or stainless, or brass, or ceramic, or whatever you can think of with the right diameter to fit over your finger and outside diameter to fit inside your wooden ring, you can just slide it into the ring and glue it in place. However, it may be difficult to obtain. But if you have it, why not experiment? I machined a hoop out of stainless for one like this for an example.
- You don't have to stain, and can leave a natural finish.
- You can leave it a matte finish by sanding the superglue down with fine paper, like 800 grit and stopping there. It'll be matte, but it'll be less transparent and harder to see the wood grain underneath.
Step 9: Clean
- Clean the polishing compound off by washing with soap and water.
- You can wax the ring with car wax if desired. Follow the instructions on the bottle.
- You're done! Enjoy the ring(s)!
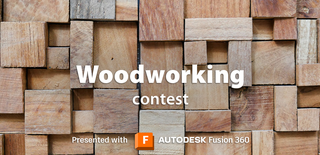
Participated in the
Woodworking Contest