Introduction: Always Set Edge Marking Gauge
I don't know about you, but I hate having to constantly change the settings on my marking gauges. Heck, I hate changing my mind, the channel, and my clothes, but I do it because my Momma taught me manners (um ... what?).
I've been building some stools and jigs and a recuring theme is the need to measure 3/4" in from the edge of a board. No problem right? I mean I have a 6" combination square. Then I change the setting for another measurement only to need 3/4" a few beers, I mean minutes later.
Sure ... I could go to the big box store down the street and buy a case of combination squares, but if you saw my herb garden build, you know my attention span thwarted me from planting a money tree. This problem calls for some scrap wood and a few minutes of my time.
Step 1: Collect the Parts
I'm predominantly dealing with 3/4" stock, be it plywood or solid wood like poplar or oak from the box store down the street. Due to this fact, I want a little more room so it doesn't bind up and annoy me even more.
On my scrap/off cut shelf, I found a 1 1/2" lamination (2 layers of 3/4" ply from a sled fence) and some hardboard .. weird right?
Step 2: Rip the Parts
I first ripped the plywood lamination to 7/16" with the veener facing up. This will be the inside width of the gauge. I then rotated it 90 degrees and ripped it to 1" for easy measurements and comfortable size (hey now).
The hardboard strips were ripped to 2" and 2 1/4" respectively. These aren't final widths, I leave everything long and trim to finish measurements whenever possible.
Glue a strip of hardboard to each side of the plywood. Be mindful of the plywood orientation. We want the smooth veener side facing up from in between the hardboard sandwich. I used glue, pin nails, and spring clamps. I also used my table saw top to keep it all flush during assembly.
Step 3: Trim to Final Widths
My "bottom" is flush (don't be fresh) and I know the "depth of my plywood is 1". I want my gauge to be 3/4" on one side and 1" on the other side. So, I trim my sides down to 1 3/4" and 2" respectively. To be honest, I snuck up on the first side and checked it on scrap wood to make sure everything was working out, which it was/did/is/will forever!.
Once ripped to width, I trimmed the length on the miter saw. This left my gauge at a little over 14", so I turned it into two gauges! It's just like TV where they give you something free to make it seem like a better value.
Step 4: Ready to Layout Lines
I now have a 12" gauge and a 2" gauge, which are fast and I never have to adjust. Obviously, you can customize the width and length to meet your needs.
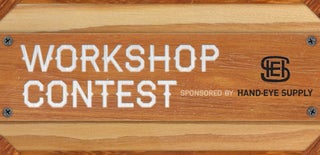
Participated in the
Workshop Contest