Introduction: Router Table Fence
Recently, I built a new router table. Technically, I already have two router tables, but they each have fatal flaws.
Router table 1 is a store bought Skil contraption. It's a good table for small projects or job site work, but I outgrew it rather quickly. The small top with recessed miter gauge track made cutting bearing edges on drums difficult. Milling door/window casings was also a challenge because I'd have to clamp the small table to another surface in order to keep it still. Lastly, the power switch died, which was inconvenient. I affectionately call it, "Little Death" as it's only a matter of time before it kills me.
Router table 2 is my shop made 4' x 4' outfeed/assembly/router table. It's beefy 2x4 construction with a melamine top and a John Heisz designed router lift. Over the years, one corner has developed a subtle downward slope and the lift has just enough play that the weight of the router will pull the bit out of perfect perpendicular alignment to the table. If you are cutting from one side of the bit, it isn't noticeable, but if you are running a drum shell around the bit ... it's not accurate enough. Lastly, I never made a fence for it, so still use Lil' Death for milling casings.
The new table is a 1 1/4" thick lamination of plywood (3/4" + 1/2") with poplar edge banding. It measures 40" x 20", is mounted to a steel stand from Rockler, and has a JessEm Mast-R-Lift II for increased precision. Since I'll still be milling casings and producing other small woodworking projects, I need/want a fence.
I don't want to drill any holes, nor cut slots into the tabletop, so I'm using a design which clamps to the side overhangs of the tabletop [similar to John Heisz's drill press table fence].
Step 1: Dadoes and Rabbet
Since the tabletop is 40" wide and I wanted a 2" overhang on each side, I used a crosscut sled to cut the plywood to a length of 44". This piece will make up the front face, as well as the base of the fence. I want to cut all of the dadoes before splitting it, so that I have perfect alignment.
Note: The width of this board is around 13" at this time. It's wider than necessary, but I didn't want to come up short and have to start over.
The outer most dadoes are 2" in from each edge. I decided on a width of 4" for the middle section and placed a dado on each side. The remaining dadoes were just evenly spaced to fit two more on each half - placement isn't imperative.
In addition to the dadoes, I cut a rabbet into one long edge before ripping the board into it's final widths.
Face Board [side with the rabbet]: 6" wide
Base Board: 5 5/8" wide
Note: Dado blade height was set to 3/8"
Step 2: Bit Hole
For the router bit opening, I marked the center of the board length and then intersected it 1 1/2" from the edge. For the face board, you want to be using the rabbeted edge as the reference. It doesn't really matter for the bottom board ... unless you were inaccurate with the dadoes and the sides aren't perfectly mirrored.
Holes were drilled using a 2" Forstner bit. My technique is to drill from both sides to eliminate blow out - especially when using plywood. Lower the bit until it barely kisses the drill press table, tighten the depth stop, and go to town. The bit will puncture a small hole, which is your alignment point once the board is flipped.
The last step is to elongate this opening by cutting out the waste ... so that it looks like a mouse hole/door from the old Tom & Jerry cartoons. This could quickly and easily be done on a bandsaw, but that's not good enough for my OCD brain, so I used the small parts crosscut sled on the table saw.
Step 3: Drilling Holes
One minor frustration with my drill press fence is that the bottom part of the side clamps is free to spin - so it's usually in the wrong position when I'm trying to slide it back onto the drill press table. This time, I'm adding alignment pegs, which will make total sense once we get to the assembly stage.
On the base board, I marked a line 1" in from all three edges, as well as marking the center of the overall line. The outside holes are drilled to 1/2" and will be for wooden dowels. The center holes is drilled to 5/16" for a bolt.
Note: This is done on both ends of the board.
While I was in drilling mode, I drilled pilot holes and countersinks for screws, followed by a quick sanding to clean up all the edges.
Step 4: Clamping Blocks
A lamination of plywood needs to be made for the clamping blocks and the construction dependent on your tabletop.
As previously stated, my tabletop is a lamination of 3/4" and 1/2", so the top two layers of my block will be the same. Since the fence will overhang each side by 2", the width of these layers will also be 2". The bottom layer is 3/4" plywood, ripped to a width of 3". That provides 1" of grab on the underside of the table, which is enough and also avoids any collisions with the stand or any bolts.
Note: I left the lengths long, so I could cut them down to size and not come up short.
Glue up was simple - spread the glue, stack the parts, flush the long back edge up, pop in a few brad nails to keep the parts from sliding, and then add clamps. After a few minutes, I cleaned up the glue squeeze out.
Note: I made sure to position the brads outside of future cutting paths.
Once the glue was cured, I trimmed off the ends and cut two finished blocks to a length of 6".
Just like with the base board, I marked a line 1" in from all three edges, as well as the overall center. The outside holes are drilled to 3/4" and only go as deep as the 2" wide plywood layers. These will be pockets for the alignment pegs. The center location on the bottom of the block is drilled with a 7/8" Forstner bit - just keep enough to recess the flange of a T-nut. That center hole is then through drilled with a 5/16" bit.
I installed the T-nuts with a hammer and a socket ... because I have no respect for sockets.
Step 5: Gussets
To connect the face and base, and hopefully keep them in a perfect 90 degree alignment for eternity, I'm using gussets - eight of them.
I started with four 6" x 6" plywood squares and then used my Rockler cross cut sled to convert them into eight triangles. They hang past the edges once assembled, but will be trimmed post assembly.
Generally, I make my own table saw sleds, but I will admit .. I like this one. The swiveling, aluminum fence with flip stop is my favorite feature, but the hold down is nice as well - especially with a cut like this, so I can keep my hands away from the blade.
Once cut, I broke all the edges with a sanding block, which keeps the veneer from chipping/breaking out when being inserted into the dadoes.
Step 6: Trimming and Assembly ... Then More Trimming
Prior the glue up, I cut back the lengths of the face board to terminate at the edge of the end dadoes. I considered leaving it full length, but figured the unsupported overhang would just twist over time and its elimination makes for easier access to the clamping handles.
This glue up was surprisingly well orchestrated and low stress. I laid the face board flat on the bench, ran a bead of glue in the rabbet, and used a few clamps to hold the base board perpendicular and flush. Gussets were added one at a time - working my way out from the center.
1. Bit of glue in the dado
2. Pull the gusset in nice and tight - checking for square with a speed square
3. Pop in a few brad nails
4. Drill pilot holes into the gussets to avoid splitting
5. Add screws
I had purposely cut the rabbet a hair wider then necessary, so that I could trim it perfectly flush using a pattern bit on the router table. The excess gusset points were trimmed off using the table saw. I had to use a spacer when trimming the top edge due to the alignment pegs [Fig. 8].
Step 7: Alignment Pegs
The alignment pegs are simply 2" lengths of 1/2" poplar dowel stock. I used a small parts crosscut sled with a stop block to make the repetitive cuts. The small push stick was used to hold the cut of/keeper piece during the cut, so that it didn't bind against the blade and explode and/or kick up into my face.
These pegs are glued into the 1/2" holes on the base board - flush to the top side.
Step 8: Handles
In the past, I've used 1 1/4" dowel stock for handles, but I wanted to switch things up this time. I also thought it would be nice if the handles had a little more visual interest than the mass of lightly colored plywood of the fence. A few seconds later, I remembered the dwindling supply of pallet padauk, which I have been using for accents within multiple projects. It's a mix of the normal red/orange wood and some spalted sap wood.
I had two cutoffs of spalted sap wood - one around 3/4" thick and the other around 1/2" thick. To that, I added a 1/4" thick slice from my last padauk board, which believe it or not was one of the pallet runners. I ran them through the drum sander, slathered them with glue, and gave them the clamps.
Once the glue was dry, I cleaned up the sides on the table saw and ended up with a 1 1/2" x 1 1/2" blank - length around 16 1/2". I tilted the blade to 45 degrees and ripped off the corners in order to end up with an octagonal blank. Due to the varied spalted widths, the accent strip is off centered, which I actually like. I used the small parts crosscut sled to clean up the ends and cut the blank in half - leaving me with two 8 1/8" long handles.
Using my Dowel Center Finder Jig, I marked the drilling target. A screw clamp helped firmly hold the work piece perpendicular to the table, so I could bore a straight 5/16" hole.
I had a few long 5/16" carriage bolts laying around, so I cut them to my desired length (around 6"). The bolts were glued into the handles using two part epoxy. I also took the opportunity to glue a fender washer to the bottoms. They aren't necessary, but I like the look and prefer having metal tighten against wood instead of wood to wood. All said and done, I was left with 2 3/4" of exposed bolt.
Note: The epoxy is in a warm water bath because it was cold in the basement - this help make it flow and mix better.
Step 9: Bit Storage
I've been keeping my bits in a storage caddy, which is in a drawer. It's an alright solution, but I figured having them even closer to the router table would be better ... it just so happened that this fence design lends itself to on-board storage.
Using some scrap plywood, I cut 5" x 5 1/4" pieces to fit within the back openings. I found that I could comfortably fit 9 of my 1/2" shank bits or 16 of my 1/4" bits into a square. I laid out and drilled two for 1/2" shank, one for 1/4", and left the forth blank for future expansion. Instead of worrying about a depth stop, I drilled the holes all the way through. To keep the squares from sliding out over time due to vibration, or falling out when I remove the fence, I added a screw to each.
Step 10: Dust Collection
For dust collection, I cut a piece of plywood to fit the center section (4" wide) and then mitered the ends for a clean look/fit. I used a crosscut sled for those miter cuts and snuck up on the cut until I had a perfect fit. It's held in place with two screws in case it's a total failure and requires a redesign.
The hole was drilled with a 2" Forstner bit and then enlarged using the router bit combo punch. My available rabbeting bearing options left me with a hole a bit larger than the dust collection hose adapter, but that was quickly remedied by wrapping the adapter with a band of electrical tape until I had a tight friction fit.
Router Bit Combo Punch: Enlarge half of the hole depth using a rabbeting bit an then enlarge the remaining depth using a pattern bit.
Step 11: Finishing
My brand/name was applied with a low tech stencil and spray paint. I add it to whatever I make as my signature, but it also pulls double duty as an embedded watermark for photos and video.
For finish, I chose clear shellac and applied it with a foam brush and rag. It dries insanely quick and two coats is durable enough for my needs.
Step 12: Glamour Shots
The fence is ready for service. Time will tell if it stays perfectly square ... things tend to move over time. I figure if it happens, it'll be minimal and a playing card shim (or two) will rectify the situation.
You can see in the first two pictures how the clamps function. The alignment pegs recess into the holes within the clamping block and keep it from rotating. Tightening the bolt will pull the clamping block upwards and pinch against the bottom of the tabletop. Simple and effective.
This design is easily scalable. Smaller for a drill press table or even a micro trim router table if you're feeling saucy. I could easily scale it up for my 49" router table, but I don't have the need ... yet.
Some may ask why I didn't add adjustable face boards, which can slide in closer to the bit and the answer is ... once I set them once on "Lil' Death," I never adjusted them. If I find that I miss them in time, I'll add them on - it's just a matter of cutting a few slots.
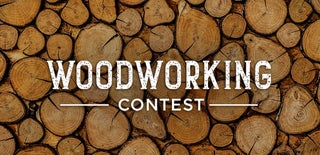
Participated in the
Woodworking Contest