Introduction: Captain Jack Sparrow's Sinking Ship
I told myself I was going to take a more relaxed approach to Halloween this year ... wear the Jack Sparrow costume I acquired with store credit winnings thanks to Oscar the Grouch in 2015. Maybe a few tweeks here and there with some weathering and a hat that didn't resemble a soggy Dorito.
Then it happened ... my brain decided I needed a sail boat for the front yard. More specifically, the top of the sinking sailboat from Jack Sparrow's introductory scene in Pirates of the Caribbean: The Curse of the Black Pearl.
Slideshow Video
Fabrication Video
Step 1: The Block and Tackle
Fabrication started with the block and tackle, since I figured it would be the most tedious aspect. I sketched out a desirable size and shape on paper and transferred it to poster board to be used as a pattern. In addition to this "side pattern," I needed truncated "end patterns," as well as a disc, for which I just traced around a 3" PVC cap.
I needed three different block and tackle configurations - single pulley, double pulley, and triple pulley. They all use the same parts, just a different quantity.
Single pulley: 2 sides, 2 ends, 1 disc
Double pulley: 3 sides, 4 ends, 2 disc
Triple pulley: 4 sides, 6 ends, 3 disc
Since I needed two of each type, it was a fair amount of tracing onto EVA foam floor mats and cutting with a razor knife. 18 sides, 24 ends, and 12 discs. It goes quickly - just keep your blade sharp. I highly recommend this Kershaw sharpener.
Note: Mark the center point of each side before cutting them out - it's way easier.
Once all of the parts were cut out, I trued up/shaped just the discs, using the oscillating belt sander. Just sanded to the line in order to knock down any angular edges. Once shaped, I used my shop made marking gauge to mark the center of each disc.
Note: Do not sand the side and end parts at this time.
A center hole was punched in each disc and side using a section of 3/4" copper pipe. I used the oscillating belt sander to put a chamfer on one end of the pipe, which is sharp enough to cut/punch through the foam mat with the aid of a rubber mallet.
Assembly is just a matter of gluing parts up and stacking them like sandwiches. My preferred contact cement is Barge. I thin it with Barge thinner for easier/more consistent application and apply two coats - first coat, let dry, second coat, let dry, join the parts.
Note: Use the 3/4" copper pipe to keep the center holes aligned as you add layers [Fig. 3 & 8]
The fully assembled blocks were then shaped using the oscillating belt sander [Fig. 9 &10]
Step 2: The Crows Nest Fabrication
The second EVA foam component was the crows nest, which started with concentric rings. The largest ring I could get out of a mat was 22" in diameter. I marked the center of three mats, set my beam compass an 11" radius, and drew the circles. Measuring in 2" and resetting my compass to 9" radius, gave me the middle sized ring ... another 2" gave me the smallest ring.
Sharpen your blade, steady your hand, and cut out some rings - but not all of the rings ... don't get carried away.
1. Cut out all three large rings - the outside and inside edges.
2. Set one of the three mats to the side.
3. Cut out the medium and small rings from the remaining two mats.
This will leave you with:
Three large rings - glued into a 3 ply lamination.
Two medium rings and one solid disc equal in diameter - glued into a 3 ply lamination with the disc on the bottom.
Two small rings - glued into a 3 ply lamination.
For the riser parts, I drew out a 2" grid on some paper and sketched until I was happy with a shape. Because the rings are concentric, the widths are set, so it's mostly a matter of vertical spacing - then drawing an arch and marking for notches. It'll make more sense during assembly. I cut out my sketched part, made a poster board pattern, traced them onto foam, and cut them out. Since I wanted the risers to be two mat thicknesses, I cut out a total of 12 - 6 from one side of the pattern, flip the pattern, and then 6 more. This creates left and right pairs and makes it possible to hide the textured side in the glue seam [Fig. 5&6]
Prior to assembly, I cleaned up the edges of the disc and riser laminations. The oscillating belt sander was used for the outside edges of the rings, as well as some faces of the risers. For the inside edges, notches, and other hard to access facets, I used a dremel with a sanding drum. I also chamfered the edges of the smallest ring with the dremel (prior to assembly - when it's easy).
Step 3: The Crows Nest Assembly
Before getting into the glue, I needed to mark my riser locations. This was done by putting all the rings back together, setting the beam compass to the outside radius, picking a starting point on the outside edge, and marking arcs around the circumference. Once you connect the three sets of opposing marks, you have six equal divisions.
Glue up started with the small ring since it goes on the inside and I didn't want to have to try to squeeze it in place. The large, top ring was my next target and went as smooth as the first phase. The third phase was more difficult because visibility became an issue. I used some contractor paper to keep the glued surfaces apart while I worked my way around the nest - if they accidentally touch, they'll stick and that's frustrating.
The top points of my risers protruded past the ring, so I just trimmed them off with the razor blade. At this point, I did another round of sanding - any faces with which I wasn't happy and chamfering all exposed edges.
To attach the crows nest to the 4" PVC mast, I used a plug/tenon. I glued up a 3 ply lamination and then shaped/sanded it on the oscillating sander, until it was a snug fig in the pipe. The center of the plug was marked and a bamboo skewer was used to align it with the center of the basket during glue up.
Once the barge set up, I drilled a 1" hole through the center of the crows nest and plug, which will be for the flagpole.
Step 4: The Crows Nest Timber Bracing
The crows nest is supported by horizontal timbers, which were created by laminating 2 plies of 1 1/2" foam strips - textured side in. A section of 4" PVC pipe was placed onto the foam plug to achieve the proper spacing for the first two parallel pieces. The perpendicular pieces were then cut to size and glued in place. All lengths were cut to fit (no tape measure) and the angled ends were arbitrary - I just cut the first one by eye and made the rest match.
The second and third tiers were cut shorter than the first with different degrees of taper at the ends, because that's just what seemed to look right. They were glued atop of the segmented first tier to add stability, as well as conceal the joints. The perpendicular strip on tier 3 adds even more stability by holds the sides together and snugly against the PVC pipe.
Note: During rigging, it become necessary to cut out the middle of the second tier. No big deal, but could've been avoided during fabrication.
At this point, I used a heat gun to heat seal the crows nest, as well as all of the block and tackle parts. That was followed by 2-3 coats of Plasti Dip.
Step 5: The Mast
Originally, I was going to attach the rope rigging to the PVC mast using eye bolts, but then I had a epiphany - keyhole slots. I then smacked myself in the head. Just tie a knot in the end of rope and hook it into the keyhole - no buying eye bolts and I'd be able to easily and quickly remove the crows nest from the mast.
With the crows nest still in place, I traced the rectangle opening on each side for positional reference. A 1" spade bit was used to drill two holes on each side. The smaller slot was created using the dremel and sanding drum.
It was at this point, I decided to test fit the flat PVC cap, which didn't fit as they are meant for thinner walled pipe. My solution was to reduce the outside diameter of the pipe ... using the table saw.
I set a stop in miter slot, set my blade to the desired height, and used my small parts crosscut sled. The sled was then advanced into the blade until it met the stop, the pipe slowly rotated to cut the groove, and the sled pulled back away from the blade. The stop block on the sled it nudged and the process repeated until you get the desired depth for this reduction - 1 3/4" in my case. It's a messy process, but easily controllable with short sections of material. I probably wouldn't use this method for anything longer than three feet. Luckily, this section was only 35".
Step 6: The Mast and Flagpole Mounting Socket
The mast components were attached to a timber retaining wall using what I'm calling a socket and pin system. A dual socket for the vertical pipes and pins for the horizontal pipe.
I started by ripping some plywood to a width of 7 1/4". That was then cut into 3 sections - a middle section at 3" and to side sections at 16". A 1" wide strip of 3/4" plywood was glued and nailed to the front, bottom edge of each section, which acts as a positive stop when securing to the wall. Notches were cut out of the front of the center section using the band saw [Fig. 3] - that's necessary for the rope wrap and will make more sense in the next step.
The pins are nothing more than 1 5/8" drywall screws with a short section of sprinkler pipe functioning as a bushing. Each plywood section gets one centered pin - inset 1" from the front edge. Three holes were drilled into the ten foot long 2" PVC pipe - one in the center and then one at each end using a step bit [Fig. 4]. These holes will slide over the pins and that's how the horizontal pipe is supported.
For the dual socket, I used a 4" flat cap for the mast pipe and a 1" coupler for the flagpole. I glued a 3" length of 1" diameter PVC pipe into the coupler and then drilled 1" center holes through the 4" cap [Fig. 5], as well as the center plywood section. The stub of 1" pipe acts as a tenon ... passing through the cap and into the plywood [Fig. 6&7]. A mark was then made on the 1" pipe, so I could cut it off flush with the bottom of the plywood [Fig. 8]. Once I had the final length, I assembled the parts with hot glue. Two screws were then added to the inside of the cap to keep it from leaning and/or pulling out of the plywood [Fig. 9].
Once all of the parts were fabricated, I painted them with black spray paint. It was $1 paint, so it took 3-4 coats.
Step 7: The Rope Wraps and Sail Clips
For the sail rigging, I used 1/2" Sisal rope from Harbor Freight and instead of punching metal grommets into my canvas drop cloth/sail, I used large binder clips as the attachment method. The top of the ship had to be set up in my workshop in order to add the rigging, which was a sight to behold.
I started with a 8 1/2" foot length for each side of the horizontal beam and just glued the first few inches to the back side - running towards the center [Fig. 1]. This will thread through the single pulley later on, so for now, just let it run free. Second phase was adding the rope coils, which will also secure the binder clips, around the horizontal beam. I did six on each side and the left side is wrapped as a mirror image to the right side - they also have an equidistant spacing of 11" ... because I'm insane.
My Method For Wrapping The Coils
1. Cut twelve sections of rope to a length of 33".
2. Hot glue the first inch in parallel to the back of the PVC pipe [Fig. 5]. I'm running them towards the center ... again because I'm insane.
3. Wrap the rope around the pipe towards yourself three times with the direction of travel going back over the glued section WITH the second/middle coil going through the front metal hook of a large binder clip [Fig. 6].
4. On the back side, thread the rope under the coils and under the initial glued down section.
5. Tighten up the coil and add hot glue to keep it in place.
6. Trim off any extra rope with a razor knife.
As an after thought, I decided to cap the pipe ends with a foam disc - attached with barge.
Step 8: The Block and Tackle Rigging
I have no idea how block and tackle is actually rigged on a functional ship, but this is a prop and nothing is bearing actual weight, so I just made it up as I went.
Single Pulley: I looped the end of the rope through the center of the pulley, decided how much slack I wanted, and glued the end to main lead [Fig. 1]. To conceal this seam, I split some rope into individual strands, coiled it around the mess, and hot glued it in place [Fig. 2]. Once I determined my desired length for this pulley rope, I made the cut, knotted the end, and used hot glue to lock it in place [Fig. 2].
Double Pulley: I looped one end of the rope through the center of the pulley, while looping the other end around the horizontal beam. Once I decided on the amount of slack, I cut the length and glued the ends to the center of the rope [Fig. 3]. Individual strand stock was used to coil around this central meeting point and hot glued in place.
Triple Pulley: This was done exactly like the single pulley [Fig. 5].
Threading the Double and Triple Pulley:
I drilled a hole into the top of the double pulley and inserted one end of the rope with a blob of hot glue [Fig. 6]. I then threaded the rope in a path I found visually appealing.
1. Up through the back of the right channel on the triple pulley.
2. Down through the front of the right channel on the double pulley.
3. Up through the back of the left channel on the triple pulley.
4. Down through the front of the left channel on the double pulley.
5. Up through the back of the center channel on the triple pulley.
Any extra rope would hang down in front and be tucked under the sail [Fig. 7-9]
Step 9: The Flag and Flagpole
Instead of buying fabric for the flag, I used three cotton rags, hot glued in series, and colored with spray paint - red for the center section and black for the tip section.
The flag pole is 1" PVC pipe with a EVA foam disc glued to the top using barge. Overall, it's 80" long, but it's in two sections for compactness and easier assembly/disassembly (30" bottom and 50" top).
The flag is attached to the PVC pipe with two small machine screws.
Step 10: The Belt Buckles and Accessories
As stated in the beginning, my initial plan was to make a few improvements to the commercially available Captain Jack Sparrow costume, so I'll quickly touch on those.
The belt buckles are laughably cheap. The plastic is thinner than the tiny drinking cup one uses during a dental visit. I imagine, if worn as is, they would probably rip and fail during the first wearing. My solution was to beef them up with some steal rod and year old casting resin.
The center "bars" of the buckles were the weakest point - one was even starting to tear upon first handling. To add strength and rigidity, I cut 1/8" steal rod stock to size and hot glued it in place. The hollow, plastic buckles were then filled with casting resin and left to cure overnight. The next day, I glued a layer of 1/8" crafting foam to the back of each buckle and trimmed it flush using a razor knife.
Note: Initially, I tried to leave two of the belts attached for speed and simplicity, but it was more of a hindrance. I ended up cutting the belts off and reattaching them later.
You could leave the black craft foam as is, but I added a coat of black paint because I had it out to weather several pirate accessories - two flintlocks, a sword, Jack's compass, the belts, and two rings. The weathering was done with a paint wash (watered down acrylic paint), which was liberally applied to the plastic and then wiped off with a rag. Paint remains in the nooks and crannies, which provides more visual depth. The paint wash was followed by dry brushing with a metallic silver paint. This adds highlights and more visual interest.
Step 11: The Wig, Beard, and Hat
The included wig with attached bandanna is probably the primary failure point of this retail costume - the floppy and undersized had being an extremely close second.
I thought about picking up a $20 wig at a costume shop and modifying it, but instead found a version on Amazon for $56. It's the best one I found for the price point and I actually recommend it because it's adjustable to fit your head, included three sets of beads, and a very nice/large bandanna. The "dreads" do start to unravel, so after a few wears, you'll need to fix them up with some styling wax or something. I added hair wraps by way of twine and strips cut from the failed bandanna [Fig. 2].
The included sail needle is just a shortened chopstick, which is alright from a distance, but since I have a workshop and wood, I decided to make a better version. It's just a strip of poplar with a hole drilled in one end and then shaped using the 1" belt sander. You could always whittle the shape and clean it up with sandpaper. The sail needle gets tied it into the wig with a length of twine.
A leather pirate hat is on my long project list, but not presently in my skillset and time wasn't on my side. I briefly considered making one using 1/8" craft foam, but overruled myself in under 17 seconds. As fate would have it, I ended up stumbling upon one at a party store (looking for a wig). It was just laying on a bottom shelf in a bag with no price tag. It's a faux leather product, very durable, and has an internal size adjustment. It turned out being $24.99, which was well worth the time saved on my end.
Beard braids were a last minute decision. I used a portion of the failed wig - braided it and used superglue on the ends, so it wouldn't unravel. I didn't have any extra beads on hand, so I just wrapped a bit of red fabric around one. A tiny dab of hot glue was used to attach them to my chin ... I know, I know ... it sounds horrible, but it wasn't. I didn't heat the gun up to dragon flame heat. Honestly, I figured removal would be where bad decisions returned to punish me, but I was pleasantly surprised. Rolling the glued area in my fingers loosened it enough for them to be painlessly removed. I lost 2-3 real beard hairs at the most.
Amazon Wig
Amazon Hat
Step 12: Treasure Chest
If I'm a pirate ... on a sinking ship ... I can't very well hand out candy. Obviously, I need a treasure chest for the candy!
Apparently, I didn't take pictures of the fabrication, but trust me, it was simple. It's made from another EVA foam floor mat. The bottom portion is a basic open box with reinforcement strips around the top to keep the sides from bowing out. The lid has more of a barrel shape, which looks more involved, but it isn't - just start with a rectangle base, cut and add the two arched sides, then cut and added the barrel top as one piece.
1/8" craft foam is used to create the faux metal banding. The sections over the arched ends are one piece, but everything else is just 1" strips glued onto the box. The lock is just a circle punched with the 3/4" copper pipe and a keyhole cut out with a razor knife.
The paint job is two coats of Plasti Dip, followed by two coats of a metallic iron paint, and then a dry brushing of metallic silver.
To keep the lid loosely attached, I used 1/4" paracord. One end was knotted with a dab of glue and then pushed through a hole in the underside center of the lid. The other end was glued into a hole within the back reinforcement strip, inside the box.
Step 13: The Warning Sign
If I'm a pirate ... on a sinking ship ... with a treasure chest full of candy in close proximity ... it can't just be floating in the ocean. Obviously, I need a dock (made from a pallet) ... and that dock needs a warning sign for pirates.
The sign is seen early on in The Curse of the Black Pearl and I found a screen grab online. It's made from three pallet slats, cut to 14" lengths, and two shorter boards were glued and brad nailed to the back. The bandsaw was used to create the raggedy damage on each end and an angle grinder used to add more damage.
Like the movie, I painted the text in black, but since it was difficult to read (even in daylight), I went back over it with white.
Step 14: Assembly
Trick 'r Treat hours in my town are 4:30pm - 7:30pm, so I assembled the boat and dock in the early afternoon. As you can imagine, passing motorists were perplexed. I had the order of assembly planned out in my head, so it went rather quickly.
1. Secure the center socket assembly to the top of the retaining wall with screws [Fig. 1].
2. Place/hang the horizontal PVC pipe onto the center pin [Fig. 2].
3. Insert the side pin assemblies into the holes on the PVC pike to easily determine proper placement and then secure it to the top of the retaining wall with screws [Fig. 2].
4. Hang the canvas drop cloth from the binder clips - I started from the center and worked outward [Fig. 4].
5. Insert the flagpole bottom section into the socket [Fig. 5].
6. Insert the mast section into the socket [Fig. 6].
7. Thread the flagpole top through the crows nest [Fig. 7].
8. Insert the flagpole top into the coupler on the bottom section [Fig. 8&9].
9. Slide the crows nest down onto the mast. The foam plug locks everything in place [Fig. 10].
10. Hang the triple/double block and tackle assemblies from the mast [Fig. 11&12].
11. Hang the single block and tackle assemblies from the mast [Fig. 13&14].
As mentioned, the boat dock was a shipping pallet. A short length of 2x4 was screwed to the front side and a piece of OSB onto the top, to serve as a platform for the candy filled treasure chest [Fig. 15]. An eight foot long 2x3 was screwed into the back side, which was for attaching the warning sign, as well as several LED clamp lights. The electrical cords were concealed behind the sign and three cable staples secured the extension cord to the 2x3 [Fig. 16]. The longer extension reel was hidden behind the sail [Fig. 17].
Step 15: Glamour Shots
Finally ... time to be a pirate!! Definitely more work than anticipated, but well worth the reactions from the kids, as well as parents. I have a local reputation for my Halloween efforts, so some people make a trip to the neighborhood just to see spectacle - and take pictures.
A few small children cried briefly, others were thrilled to see Captain Jack ... one even insisted on being aboard the ship for his photo op. Then there was the Mini Captain America who couldn't decide if we were friend or foe.
As I say every year ... I'm going to retire on a high note, but we'll see what happens next October.
I have included a PDF version of the templates I made for the block and tackle, as well as the crows nest risers - just in case anyone needs a jump start on foam sailboat fabrication.
Halloween Past
Mikey from Teenage Mutant Ninja Turtles [2017]
Marvin the Martian [2016]
Oscar the Grouch [2015]
Animal from the Muppets [2013]
Bender from Futurama [2011]
Edward Scissorhands [2010]
Step 16: The Build Videos
Fabrication Video
Slideshow Video
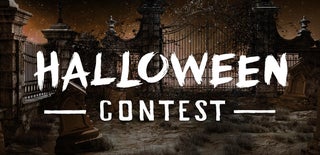
Runner Up in the
Halloween Contest 2018