Introduction: 2 Layer Glow Ring - Batteries Not Included
Just kidding there are no batteries needed 😂 These rings gets there illumination by mixing a glow powder with the resin on the inner layer of the ring. Then by placing this glow resin in a light source for a little while such as the sun or under a lamp it will emit a glow for a short period of time. For this demo I did two rings, one using a neutral green glow powder and for the other one I used a bluish-green glow powder. I personally like the neutral green better as it gives off a brighter glow and shows up longer after it’s been charged from a light source. Be sure to get to the bottom of this instructable for a gallery of other two layer rings I've done. Well let’s get started and thanks for looking.
Step 1: Material and Tools You Will Need
1. Glow powder
2. Resin - for this demo I use a polyester resin
3. Molds - pics show a few choices. I used the pvc for demo
4. Masking tape
5. Sandpaper
6. Calipers
7. Dremel buffing wheel
8. buffing compound for polishing
9. Ca glue - thin and medium
10. Ring sizer
Machines Used
1. Drill press
2. Lathe
3. Dremel
Step 2: Making the Inner Glow Blank for Ring
1. Prepare the mold you plan on using for your blank. I used a 1 1/4 inch pvc pipe with the bottom taped off for the demo.
2. Next I mixed about a teaspoon of glow powder into about 2 ounces of resin.
3. After mixing the resin according to the manufactures instructions then pour your resin into the mold. Make sure the resin and powder are mixed well as the powder may want to settle to the bottom of the mold.
4. Allow the glow blank to harden completely before removing from mold. I waited until the next day.
Step 3: Deciding Ring Size and Preparing the Inner Glow Blank for the Ring
1. If you know your ring size great but if you don’t you can purchase a inexpensive ring sizer for this as shown in the photos.
2. I decided for this demo I would do a size 10 u.s. which you can see by the picture is 19.80mm wide.
3. You will want to drill the blank out slightly smaller then your ring size then sand to the finished ring size. I have found for drilling purposes a diamond tile drill bit works best for me. It doesn’t chip out the resin like some drill bits do.
4. Once I drill out the blank I start sanding the inside starting with a 180p sandpaper and reduce grits ending with 400 wet-dry until perfectly smooth.
5. Next it goes on the lathe and I turn it down the blank until the wall is about 2mm’s thick. Don’t turn the walls down to thin or you will not get as much glow from the ring once it’s completed.
Step 4: Preparing the Outer Layer of the Ring
1. For the outside layer of resin I decided to use a couple pieces of multi color resin that I collected awhile back when I worked at my nephews surfboard factory.
2. First take a outside measurement of the inner glow blank you just finished. This one ended up being 21.80mm.
3. As with the inner blank when you drill the outer blank be sure to drill it slightly smaller then it needs to be then sand larger until the inner blank fits snugly into it. As shown in the photos.
4. Before I glue the pieces together I tape off the inside of the glow blank with making tape to prevent the ca glue from getting on it during the gluing procedure.
5. Next I coat the outside of the inner blank and the inside of the outer blank with a medium ca glue and press them together. As shown in photos.
6. Allow glue to set before proceeding.
Step 5: Turning Ring Blank to Desired Shape
1. Once glue has set I sand the corners off ring blank before putting on lathe.
2. After placing blank on the lathe I turn it down to where the outer layer is thin enough so that when the ring is glowing It shows through the outer layer.
3. Next I take the ring down to the width I want either by turning or sanding.
4. Next I sand the hard edges off the ring and shape the profile to how I would like it.
5. After shaping its time to go through the sanding process. I start with 180p sandpaper and go through different grits until almost smooth.
6. Just before the final sanding I put a couple of coats of thin ca glue on the side of the ring where the inner and outer layers met. This is to seal any small gaps there may be. Probably don’t need to do this step if there are no gaps.
7. If you did apply ca glue you will need to do the sanding process again all the way down to 400 wet-dry.
8. Next I remove the ring from the lathe and give it a good sanding with the 400 wet-dry by hand.
Step 6: Polishing- Final Step
1. Now the fun part starts. This is when all your hard work comes together.
2. For polishing I used a wool buffing wheel On a dremel tool. Shown in photos.
3. I start the buffing using a 3m super duty rubbing compound.
4. Next I switch to a 3m marine compound.
5. Final buffing step is to give it a good rubbing with a soft cloth.
6. Time to give your ring a good charge in a light source and check it out.
The green glow ring finished out as a size 10u.s. and 12.96mm wide
the blue glow ring finished out as a size 11u.s. and 13.85mm wide
Step 7: Here's a Few More Two Layer Rings to Inspire You to Get Started
To check out some of my other resin work either go to resinandwoodworld on Instagram or resinandwoodworld.etsy.com
Thanks for looking
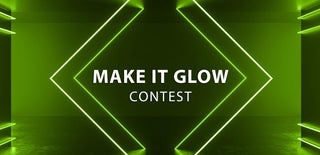
Second Prize in the
Make it Glow Contest