Introduction: 2d Image to 3d Printed Jewelry
Hello,
This is a very basic method of making a 3D printed jewelry from 2D image using free 3D CAD software / tools available.
For this you need an image which is just black and white
Supplies
1) Black an white image
2) Image to 2D CAD converter software or you can use https://convertio.co/
3) Free CAD software like Fusion360 or Draftsight
4) 3D printer, I have used UV resin printer
Step 1: Ensure Your Image Is Just Black and White
I downloaded my image by just googling "angle on moon", there were many images, but we need only black an white image, so I downloaded this from https://www.pinterest.ca/pin/521221356870996665/
Many times we feel the image is black and white, but close to the edge there are grey spots, which might increase confusion for your converting software. For that open your image for editing in Microsoft Paint or similar editing software, save the image as "Monochrome Bitmap" and this will ensure you have just black and white image.
Step 2: Convert Image to 2D CAD = DXF or DWG Format
You can use free image to CAD converting software like "Img2CAD", but I prefer the online solution from https://convertio.co/, upload your image, select to convert CAD > DXF, click on "Convert" and download
Step 3: Converting From 2d to 3d
*Please refer attached video*
I am using Draftsight as CAD software, basically the process will be the same.
Open the file in CAD software and zoom to fit the geometry to the working window. In Draftsight type "z" for zoom and press "enter" or "space bar" button on keyboard, then press "e" or "f" and press "enter" or "space bar" button on keyboard. This will fit entire geometry to the center of the working window.
Now as you can see I have two loops in my geometry, the angle and the star, so you can have one loop either by deleting one loop (the star) or else move one loop close to another loop, such that they overlap and trim and join them, as in the steps mentioned below, or else just continue with the two loops, just ensure that both are closed loop.
In Draftsight, use your mouse wheel to zoom in and out, select the star geometry using your left mouse button and type "M" and press "Enter", select a random point on screen to pick the star and you will see a line starting from that point and the star is moving as you move your mouse, when you feel you are ok click left mouse button again to drop it. I felt that it required some rotation, so type "ro" and press "enter" button. In a similar fashion select the star. (you can select the object and then type the command shortcut like "m" or "ro" or visa versa) select a point of rotation by your mouse left button, mostly a point within the geometry to rotate and you will see a line being stretched from that point and your selected object rotating about that point. Again press the mouse left button to drop after rotation.
Use trim command to remove overlap, type "tr" and press "enter" twice" and select the unwanted edges, such that it forms single loop, add geometries or remove, I had to add a circle to hook a chain, type "c" and press "enter", select a point close to the loop to make an overlapping circle. I made two concentric circle but that made two loops one residing in another, which didn't worked. Now again use trim command to trim away unwanted.
Ensure there is single loop geometry, no overlap or open ends. Type "region" and press "enter", select all geometries and press enter, now you are ready for 3D
Now type "orbit" and press "enter button and use your left mouse button to rotate your geometry in 3D. Type "extrude" press "enter" button, select the loop and press "enter", and you will observe your geometry moving to form solid, either click mouse left button when you believe you got a good thickness, or type a thickness value in numbers and press "enter" button. If you feel that it is not enough thickness, then press "Ctrl" and "Z" to undo and again do the extrude process. to see your model in solid format, type "shade" and press "enter", again type "orbit" and with your left mouse button ensure your solid looks good.
For the hole I have to make solid from it and then do boolean operation of subtraction, similarly I made some stars as well using line command and made solid then subtracted them.
Now export the model to STL format for your printer.
Basically doing same in Fusion360 will be more simple and easy.
Step 4: 3D Print the Model
I am using UV resin 3D printer, if you have one, so I believe you might also know how to use it, so I am not providing those steps, scale your model to the size you require, this option is available in almost all 3D pring software.
Attachments
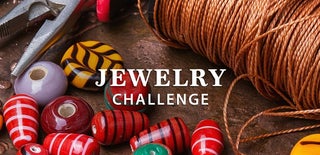
Participated in the
Jewelry Challenge